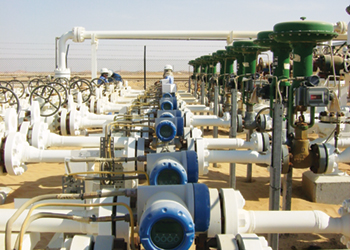
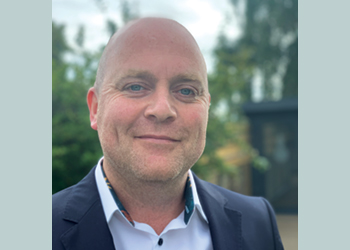
Since achieving Aramco approval, drilling contractors across the country have first trialed, and then implemented, the use of Duraband on their drill pipe and other drill string components to protect them from wear
The demand for hardbanding in Saudi Arabia continues to grow, as wells become more directional and wear on the drill string increases.
The growth in the use of Duraband NC® hardbanding in the Kingdom since it was first introduced in 2018, has been significant.
Since achieving Saudi Aramco approval, drilling contractors across the country have first trialed, and then implemented, the use of Duraband on their drill pipe and other drill string components to protect them from wear.
The product is applied and reapplied 100 per cent crack-free, meaning there is no need for costly removal before it’s reapplied.
Oil company professionals are involved in decisions regarding hardbanding choice, since they are concerned about wear on casing.
The correct material not only protects the drill string, but also reduces wear on the casing by up to 50 per cent in comparison with ‘un-banded’ tool joints.
Drilling managers also want to decrease the overall cost of the drilling operation and are encouraging their contractors to use more reliable hardbanding materials such as Duraband NC.
![]() |
Training and support from the hardband material manufacturer is vital |
The lessons being learned in Saudi Arabia as it embraces Duraband can be useful. It is a mature market for hardbanding where older, less reliable and more costly products are still used.
Written specifications on drill pipe may not always be updated in time to keep pace with new approvals, but through collaboration between providers and end users, costs can be reduced immediately.
Duraband NC has been widely used around the world for almost 14 years, and it remains the most popular choice in most drilling regions today.
Every hardband material is unique, with a different chemistry that determines wear resistance, casing friendliness, reliability (susceptibility to cracking and spalling), and re-application capability.
The owners of drill pipe have a decision to make; which material will deliver the highest cost savings and the guarantee of reliable protection for the entire life of the drill string?
A choice of hardband is made when purchasing new drill pipe and again whilst choosing the material for re-application during drilling operations.
There are several factors that should be considered when selecting a hardband material.
CHEMICAL COMPOSITION
![]() |
Cracked hardbanding should be |
The base matrix and carbides used for wear resistance and casing protection are unique to each product. Carbides used include niobium, titanium, boron and chromium and they are found in varying percentages in the overall chemical footprint of the deposit.
Although some hardband materials are compatible, care should be taken when applying one product over another, as conflicting chemistries may cause the hardband to crack and fail.
Similarly, some products have a chemistry, which is stable after the first application, but can fail after reapplication when the effects of dilution from the softer tool joint material are reduced. Laboratory testing has shown that some elements, for example, boron, are unstable in higher percentages and result in cracking.
EASE OF REAPPLICATION
The hardband will eventually wear during drilling operations, with the rate of wear determined by well profile, formation characteristics, drilling methods and other factors.
When inspection reveals the height of the hardband has fallen to 0.8 mm or less, it should be sent for reapplication.
Different hardbanding materials will wear at different rates under the same conditions.
Depending on the worn hardbanding material previously applied, reapplication can be straightforward and simple, or it can be more complicated.
During welding, the material being applied penetrates and mixes with the base material it is being applied to.
On the first application to a new tool joint, the hardbanding layer will have some dilution from the base tool joint material and contain a percentage of both the softer and harder chemistries.
With reapplication, the weld material is being applied over the previous partially diluted hardband, and so the result is a higher percentage of hard material.
Dilution is an important consideration because the chemistry of different hardbanding products varies greatly.
The wrong chemistry can result in cracks and defects as the percentage of hard material rises.
When this happens the hardband must be removed and the tool joint repaired, a costly and time-consuming process. Advice should be sought from the hardband manufacturer before reapplication over a different product.
TECHNICAL SUPPORT
![]() |
Hardbanding applied 100 per cent crack free |
As well as having a quality material, there is much more that any company protecting their drill pipe with hardbanding should expect from the manufacturer, to ensure they get the greatest benefit from this technology:
• A network of drill pipe manufacturers for application on new drill pipe and local service companies who have been trained and licensed accordingly to re-apply the product, through a strict qualification programme. There are currently more than 200 certified applicators of Duraband NC worldwide.
• Local, continuous, training and support: Technical specialists spend many weeks per year visiting applicators and end users around the world.
• Material certificates from third parties: Duraband NC has achieved excellent results in casing wear tests and holds NS-1 certificates for first application and reapplication over itself and other products.
CONCLUSION
"There has been a perception that cracked or damaged hardbanding is inevitable, and expensive remove and repair procedures are necessary. This is simply not true. With the approval of Duraband NC, direct defect-free reapplication is normal and is already saving very significant costs for both the drilling contractor and for the oil company," says Colin Duff, Global Director of Hardbanding Solutions by Postle.
"The development of the hardbanding market in Saudi Arabia gives us the opportunity to learn more about the importance of hardband material selection," he concludes.
Duraband NC is stocked in Dammam and available from eight certified applicators across the Kingdom.