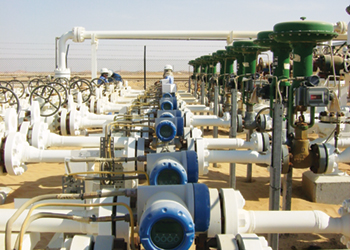
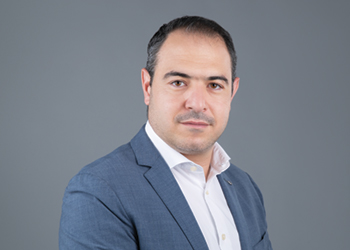
Digitalisation can enable the chemical industry to get more from less while embracing the new norms and following through with the sustainability commitments, Tariq Bakeer, Regional Managing Director, Endress+Hauser Middle East, tells OGN
The chemical industry has always stood out in terms of diversity and complexity. This is mainly driven by the wide variety of chemicals produced and their characteristics, and how this reflects on the widely varying requirements in process, compliance, and safety, among others.
With such a variety of chemicals coupled with the major slowdown the industry has witnessed over the past few years, according to a recent study by Mckinsey, in addition to growing competition, significant cost pressures, growing energy demands and the fast changing environmental and customer landscape, three topics rise on top of the industry’s priority list: Safety, process excellence and digitalisation.
This makes the chemical industry a very attractive industry only for companies with deep understanding of highly demanding processes; those that do not shy away from complexities; that live safety as a culture not as a compliance; and finally those companies that cherish innovation and the role of technology in increasing plant availability, safety, productivity as well as optimising and simplifying the maintenance cycles.
![]() |
Reactor vessels at a chemical plant |
Simple and incremental improvements, while still necessary, are no longer sufficient. No wonder then that the chemical industry has been one of Endress+Hauser’s strategic industries for the past many years, with a long experience developed through working closely with industry pioneers like BASF, Solvay, SABIC, Borouge, Equate, QChem and many others.
Endress+Hauser continues to innovate its approach and align it with the trends and technologies, by reshaping its offerings to ensure customers achieve their targets.
The company’s focus has been on areas like safe in-process cleaning and calibration, self-diagnostics and effortless proof testing with integrated Heartbeat Technology; unplanned shutdown prevention with advanced diagnostics, and best-fit instruments with intrinsic safety and high accuracy that provide reliable data and safety to the process, in compliance with IEC standards for Safety Instrumented System (SIS) and functional safety for related electrical/electronic/programmable electronic, and where Safety Integrity Level (SIL) instruments play a pivotal role as part of the overall safe system.
Starting from the handling of raw material, going into production, followed by storage and transportation, precision, reliability, efficiency, and safety are all differentiating factors for companies that will grow sustainably in the chemical industry.
Handling and transport of chemicals and other hazardous liquids can carry risks to people, assets, and the environment, particularly when loading and offloading.
Mitigating such risks through rigorous safety measures whilst ensuring efficiency is a major challenge for the chemical industry worldwide.
Conducting complex processes at scale is a key chemical industry challenge. Precise measurement and control are vital for optimal efficiency and transparency. With intense competition, maximum uptime is essential, as is safety of personnel.
The chemical industry is characterised by highly complex processes. Plant managers must ensure consistent availability of raw materials, often stored in various types of tanks, and delivery of the right quantities at the right time.
Stock level transparency is vital, which relies on timely consolidation of accurate measurements from multiple sources, a key challenge for many companies.
To achieve all of the above mentioned, getting data from the field is of utmost importance.
As per findings, 90 per cent of the Endress+Hauser portfolio is already digital, however, 97 per cent of data remain unused. This provides a wide space to smarten the plants and empower the field.
Following a data analytics approach will enable the sector to tackle the issues associated with transfer and storage of chemicals, inventory monitoring and supply chain.
It will also increase plant availability and lower downtime through predictive maintenance, as well as increase safety in processes and strengthen decision making with real time data.
In brief, digitalisation allows the chemical industry to get more from less while embracing the new norms and following through with the sustainability commitments.