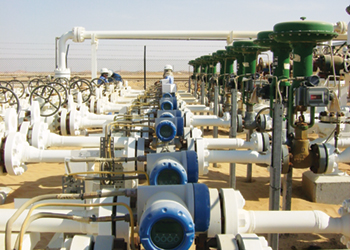
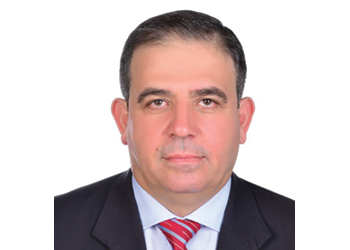
Sulzer Chemtech has revamped the largest aromatics extraction plant in the world using its renowned technology GT-BTX®.
Besides licensing the technology to operate the plant, the scope of work included basic engineering work, supply of proprietary equipment and critical process equipment, and provision of technical services for project planning, commissioning, as well as plant startup.
"GT-BTX is an extractive distillation process utilising a proprietary solvent named Techtiv®, which is far superior in performance to other available solvents," Dr Rafic Traboulssi, Sales Director - Technology Licensing, MEA region, Sulzer Chemtech, tells OGN.
He explains: "Techtiv provides the highest extraction efficiency than any other solvent and enables significant capacity increase and operation over a wide feed range including reformate, pygas, COLO, and naphtha."
Over 70 reference units around the globe have been licensed to use GT-BTX technology, including both revamped and grassroot plants.
OBJECTIVES OF THE REVAMP
![]() |
Schematic representation of aromatics extractive distillation plant |
Dr Traboulssi says the customer aimed to increase plant capacity by 10 per cent while also reducing benzene losses in raffinate to below 1 per cent w/w noting that the benzene content in raffinate was approximately 20 per cent w/w.
In addition, it wanted benzene and toluene to be produced at high purities (over 99.5 per cent w/w).
SELECTING THE RIGHT SOLUTION
Based on feed content in benzene and toluene, the solution was engineered based on the GT-BTX technology to replace the third-party technology then in operation.
Basic engineering design was carried out after identifying necessary but minimal changes to existing plant setup.
No major process equipment is required. Besides replacing existing solvent with Techtiv, a water loop was added since it is required for Techtiv, and the solvent recovery column reboiler was upgraded.
The engineering work took about five months, and the necessary modification work was implemented during a shutdown of four to six weeks.
REVAMP RESULTS
![]() |
After startup, the new revamped plant was able to achieve the following improvements:
"The superior performance of GT-BTX technology is very well evidenced through the better quality of benzene and toluene products, the impressive reduction of benzene in Raffinate, and the reduction of the steam consumption of 7 per cent to 12 per cent even though plant feed rate was increased from 210 kTA to 240 kTA (an increase of 15 per cent)," says Dr Traboulssi.
"The customer is very satisfied with the performance of the GT-BTX technology to the extent that it has considered and implemented an additional technology from the GT-BTX series," he concludes.