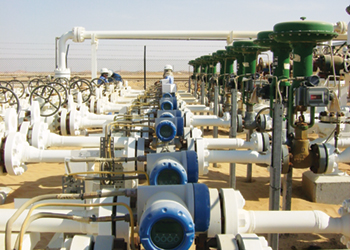
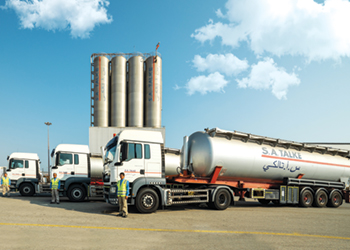
With a wealth of industry knowledge backed by a German/Saudi heritage, the company has gained its reputation as a world-class logistic service provider for the chemical/petrochemical industry, Managing Director Makhlouf Benzahia tells OGN
S.A. TALKE has grown in strength in Saudi Arabia — expanding both its footprint and operations — to establish itself as a unique and reliable logistic partner in the chemical and petrochemical sectors.
This March the company reached a milestone for serving the Saudi market for almost two decades.
Today S.A. TALKE is a major regional player offering a diverse range of services to meet the needs and expectations of clients.
It serves a number of industry leaders of the petrochemical industry and currently operates over 15 projects providing a diverse service portfolio to clients in the Eastern and Western regions of the Saudi Arabia.
Established in Saudi Arabia in 2004, S.A. TALKE represents a strong partnership in its inception — between Saudi Arabia’s Al-Jabr Group of Companies and Saudi Industrial Services Company (SISCO) with their German partner Alfred Talke Logistic Services, a 75-year-old global logistics services provider.
"Due to its wealth of industry knowledge and German/Saudi heritage, the company has gained its reputation as a world-class logistic service provider for the chemical and petrochemical industry," says Makhlouf Benzahia, the company’s Managing Director.
S.A. TALKE’s services include onsite operation, packaging, plant operation, maintenance of packaging lines, and various sophisticated and complex machinery such as robots and high-tech cranes, specialised transportation, container yard management, silos storage, and bagging.
With its unique expertise and global reach, the company can support its clients in designing plants and logistics facilities that meet all industry-related standards.
Over the past years, S.A. TALKE has evolved considerably. It has expanded its footprint in Jubail, gaining new clients, growing with existing ones, and has established a footprint in the Western Region. It has built a strong team of over 2,100 employees in Saudi Arabia.
The company has built its knowledge and capabilities to offer more unique services to customers.
A unique selling proposition of S.A. TALKE includes bagging machine overhaul services and spare parts warehouse management services. The spare parts warehouse management services include:
• Manage all inventory control activities through SAP and ensure 100 per cent accuracy.
• Manage the spare parts receiving process from the suppliers.
• Arrange gate pass for deliveries.
• Perform quality inspections and putaway according to the predefined strategy.
• Validate purchase requests created by SAP and submit them to the purchasing department.
• Manage the issuing process and fulfill end user requests.
• Consider shelf-life of batch managed items.
• Prepare discrepancy reports and investigate them thoroughly with the suppliers and buyers.
• Manage OSDRs.
• Daily physical inventory for all the items received and issued.
• Manage cycle count process.
• Prepare weekly inspections reports, monthly operations reports and export reports.
• Prepare extensive analysis and propose continuous improvement initiatives to customer.
Bagging machine overhaul services: S.A. TALKE offers a variety of cost-effective bagging machine technical services and parts options with certified technicians to support customers’ needs.
These include local dispatch programmes, equipment installation and startup, operator and maintenance training, machine evaluation and performance optimization, rebuilds and retrofits, and parts programmes.
"At S.A. TALKE, we are committed to listening closely to customers to understand their needs and requests. We treat each equipment repair process as unique," says Benzahia.
He adds: "Our packaging equipment service specialists combine years of field experience with unrivaled packaging machinery knowledge to deliver expert service and consultation to clients."
S.A. TALKE technicians help customers diagnose and repair their bagging equipment and train them in proper operation and maintenance.
The company services several legacy brands including W&H, Beumer, Haver, Boecker, Yaskawa Motoman, FANUC ROBOTPAC, and Möllers.
Benzahia says: "Our technicians have expert knowledge of bagging machine parts, product handling, bag sizing, and machine features that affect bag weight accuracy. Our senior technicians can also diagnose problems that have no apparent electrical or mechanical cause."
Additionally, S.A. TALKE offers preventive bagging machine maintenance. Its overhauling team includes expert matter technicians from different fields, such as mechanical, electrical, PLC specialist, EHSS officers, support team, and planning and supervision.
"Our team has successfully conducted an overhauling activity of two packaging lines at one of SABIC reputed plant sites," says Benzahia.
In the engineering, procurement, and construction (EPC) segment, S.A. TALKE has executed a 10-year design, build, and operation project of a multi-user facility for a key client in Jubail Industrial. The project has been running successfully for the last nine years, meeting its design criteria.
Furthermore, S.A. TALKE is well known for first-class standardisation and management processes — a pool of knowledge it has built over the years.
These processes cater to most of the petrochemical’s business requirements. "So now, when we win a new business, we have 70 per cent of our processes that plug and play. The company’s strong safety culture is well recognised," remarks Benzahia.
Additionally, S.A. TALKE is assessed according to Gulf SQAS for transport and warehouses in Saudi Arabia, and is also a member of Responsible Care, the chemical industry’s unique global initiative that drives unceasing improvement in environment, health, safety, and security (EHS&S) performance, together with open and transparent communication.
"Safety is a core value and a top priority in every aspect of our work. We have created a work environment where our people are empowered to take action, new ideas are recognised, and success is achieved and celebrated together.
"With open communication, we have built a relationship with our people based on trust and mutual respect, and we have developed a ‘can-do attitude, enabling us to continue improving as a team," concludes Benzahia.