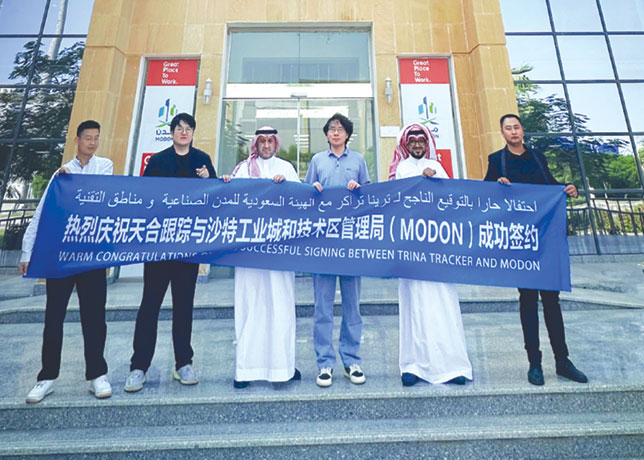
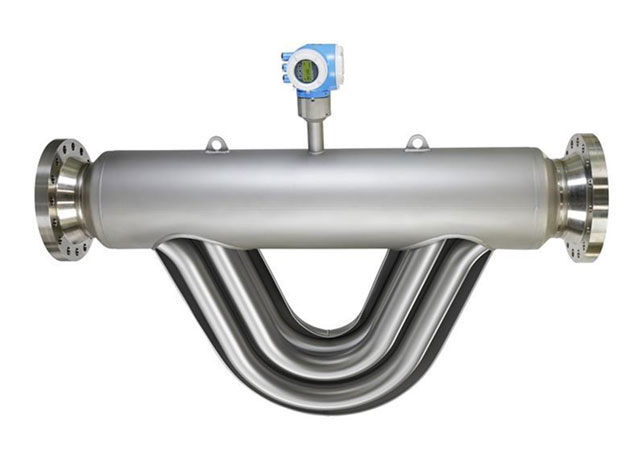
Multi-Frequency Technology compensates errors caused in Coriolis mass flowmeters by bubble and resonator effects in gas-liquid mixtures, ensuring precise density and flow measurements, Rodrigo Quintero Bejarano tells OGN
Coriolis mass flowmeters are widely accepted and used in various industries because of their high reliability and accuracy for density and mass flow rate measurements.
These meters can achieve an accuracy of ±0.1% o.r. or even ±0.05% o.r. for mass flow rate, while density measurements can reach ±0.1 kg/m³ under reference conditions by some manufacturers.
ADVANTAGES OF CORIOLIS MASS FLOWMETERS
The Coriolis measuring principle offers a distinct advantage over other meter types as it directly measures the true mass flow rate instead of volumetric flow rates (Figure 1). Most other flowmeters measure flow velocity, which requires further calculations to determine mass flow. As explained by Rodrigo Quintero Bejarano, Advanced Expert Industry Manager Oil & Gas at Endress+Hauser, this principle makes Coriolis meters highly effective in various applications.
![]() |
Figure 2 ... motion of a bubble in a measuring tube filled with liquid |
These advantages stem from the measurement principle based on the Coriolis effect, which reveals the fact that a Coriolis force is generated when an object on a rotating body moves away or towards the centre of rotation.
This force is related to the inertia of the object and has a direction perpendicular to both the velocity of the object and the axis of the rotation body.
Challenges: In practice, Coriolis flowmeters are usually only used for single-phase fluids, that is, liquids or gases, as it is known that their accuracy can be affected by the existence of entrained gas in a liquid flow.
Extensive research has identified, among others, two primary sources of error; the bubble effect and the resonator effect (also known as the compressibility effect).
UNDERSTANDING THE BUBBLE EFFECT
Bubble effect theory was developed and later extended to viscous bubble theory by Hemp et al. The essential idea for the root cause of the bubble effect is that a gas bubble in the measuring tube of a Coriolis mass flowmeter does not strictly follow the oscillation of the surrounding liquid with the same amplitude if the liquid cannot "hold" the bubble well.
This is a result of the density difference between the gas (ρg) and the liquid (ρl), which generates a relative motion between the bubble and the liquid.
A secondary flow (Figure 2) around the bubble is induced by this relative motion and causes a different inertial effect from the one that Coriolis mass flowmeter utilises to sense mass flow rate.
RESONATOR EFFECT and its impact
Compared with free bubbles, suspended bubbles are much more difficult to eliminate from the process.
Although causing no bubble effect error, they still introduce a resonator effect as a result of the significantly increased compressibility, giving rise to density and mass flow measurement errors.
Studies show that suspended bubbles pose the greatest challenge to Coriolis flowmeters used in the field.
Even a small gas fraction dramatically reduces the speed of sound in a liquid, lowering the resonance frequency of the fluid mixture in the tube. If this frequency approaches the driving frequency of the oscillating tube, it causes a resonator effect (driven out of resonance) that cannot be neglected during measurement.
MULTI-FREQUENCY TECHNOLOGY (MFT)
To compensate the measurement errors induced by the resonator effect, MFT has been researched and developed based on the vibrational properties of the Coriolis sensor and advanced further with respect to the Two-Mode Compensation proposed in Figure 3.
When a Coriolis meter measures a liquid with suspended bubbles, the measured density error is defined as
![]() |
Figure 3 ... mode 1 mode 2 |
In the advanced sensor design (Promass Q), special consideration was given to ensure that the oscillation of the measuring tube is not only well balanced for the basic working mode, but also for a higher third mode of the measuring tube.
A good balance for tube oscillation is critical for the design of a Coriolis meter to ensure that the tube vibration is isolated from the external process connection.
Then, a reliable density measurement can also be realised with the third mode, which provides an independent density reading ρa3 from that of the first mode and therefore can give additional information about the resonance properties of the fluid.
The reason for relying on the third mode instead of the second mode of the tube lies in the fact that the second tube mode is anti-symmetric with respect to the driver, so that this mode cannot be excited by the existing driver.
In addition to mode shape, the third mode differs from the basic working mode by having a much higher resonance frequency, typically by a factor of 5-6.
It should be noted that the two tube modes can be driven simultaneously with the same driver.
The mechanical motions and the corresponding signals of the two modes are then superimposed.
With the modern electronics developed for this purpose, the combined signal can be simultaneously processed and two independent vibrational properties of the two modes can be obtained accordingly.
APPLICATION OF MFT
There is numerous entrained gas applications to which MFT can be applied, such as heavy oils that can hold bubbles because of high viscosity, dairy products that contain micro-bubbles due to product nature, etc.
![]() |
Figure 4 ... test setup |
Targeted for one interesting type of application, Promass Q with MFT was tested with outgassing from produced water in Porsgrunn, Norway.
The test setup is shown in Figure 4. A reference Coriolis meter was installed in the high-pressure section, where the production water saturated with nitrogen was single phase, which the reference Coriolis meter measured with an uncertainty of ±0.1 per cent.
The test Coriolis meter with MFT was installed in the low-pressure section, where outgassing was created to generate a gas-liquid two phase flow (Figure 5).
As can be seen there, a homogeneous micro-bubble flow regime was produced by the outgassing.
CONCLUSION
![]() |
Figure 5 ... outgassing |
The bubble and resonator effects are the primary sources of measurement errors in Coriolis mass flowmeters under entrained gas conditions. While process optimization methods such as gas eliminators or high turbulence can help suppress free bubbles, suspended bubbles remain a persistent challenge.
Multi Frequency Technology offers an innovative solution by utilizing multiple oscillation modes to compensate for resonator effects, significantly enhancing accuracy in density and mass flow measurements.
Additionally, MFT enables the measurement of speed of sound in entrained gas fluids, which, when combined with pressure readings, allows for Gas Volume Fraction (GVF) calculation in three-phase flows.
By integrating MFT, industries can achieve more reliable and precise flow measurements, even in the presence of entrained gas, thus unlocking new possibilities for process optimization and efficiency.