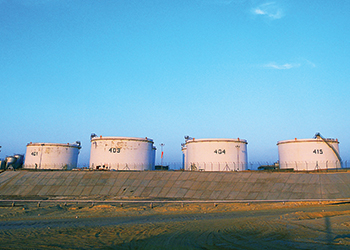
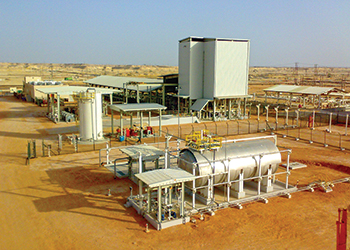
Replacing natural gas combustion with solar steam at enhanced oil recovery sites has the potential to save a lot of carbon emissions, even if these technologies don’t take us any closer to actually moving off fossil fuels
Cost savings will become more crucial if Omani oil projects are to remain competitive. The country needs to opt for solar steam generation in enhanced oil recovery (EOR) projects.
"We see down side risk to the sultanate’s oil production forecast as low oil prices weigh on comparatively costly EOR projects", warns a report by Business Monitor International.
Oman employs a number of technologies including miscible gas injection, thermal and chemical recovery to boost output. Thermal EOR is the most widely used, though polymer injection projects are seeing more attention.
Around 200,000 barrels per day (bpd) of Oman’s 950,000 bpd production is sourced from EOR.
"With oil prices remaining at a much weaker level, profitability of many of the projects is considerably reduced," points out the report.
Thermal EOR requires the burning of natural gas to generate the steam needed to power thermal recovery. This technique can add as much as $10 per barrel to the cost of oil extraction, making it significantly less cost competitive at a lower price.
Replacing natural gas combustion with solar steam at enhanced oil recovery sites has the potential to save a lot of carbon emissions, even if these technologies don’t take us any closer to actually moving off fossil fuels as the primary source for power generation and transportation. Around 24 per cent of Oman’s domestic gas consumption is also used by the oil sector, straining the availability of gas for other areas of the economy. According to Mark Gregory, chief economist at Ernst & Young, using solar energy for steam production will free valuable gas resources needed to power new industries and diversify the economy.
"If Oman were to localise the supply chain for solar steam generators, solar EOR could contribute more than $12 billion to Omani GDP over the next decade," he adds.
The gas not burned for EOR can be used for higher-value applications, such as LNG export and power generation. Additionally, gas can be redirected to the Omani private sector, where dozens of industrial projects have been cancelled or stalled in the past decade due to gas shortages.
Adam Lesser, analyst for Gigaom Research, says, people may think of the Middle East as overflowing with cheap fossil fuels, that’s only partially true.
"Energy use is growing very quickly across the Middle East and it’s expensive for the sovereign oil producers to burn natural gas to enhance oil recovery when it could be exported".
According to him, there is renewed interest in solar photovoltaic in the region as the countries would rather not use their precious fossil fuels to produce power domestically when it could be exported at a premium.
The phase 2 of the Marmul polymer injection project reportedly cost around $1 billion to complete.
"In an optimistic scenario, where the project averages 60,000 bpd of production over ten years, capital costs alone would add $5/bbl to the commercial breakeven," says the report.
Petroleum Development Oman (PDO), which produces more than 70 per cent of the country’s and Occidental Petroleum, which operates the 122,000 bpd Mukhaizna field, are looking for cost saving measures.
"In the short-term this is most likely to come from renegotiating oilfield service contracts and improving operating efficiencies", points out the report.
However, over the longer-term, lower oil prices could play an important role in improving the prospects of solar steam generation to replace gas use in thermal EOR projects.
According to GlassPoint, leading Oman’s first solar EOR project at PDO’s Amal West field, 60 per cent of the operating cost of thermal EOR projects is related to the purchase of gas.
Apart from the second phase of the Marmul, a new polymer injection is being tested on the Nimr field to sustain the 90,000bpd production level.
Also the Harweel thermal EOR project has increased output to 50,000 bpd as of May 2015, while optimisation of thermal recovery processes on the Al Amal field will support future production.
At the same time, a ramp-up of steam flooding operations at the Mukhaizna field will maintain plateau production.