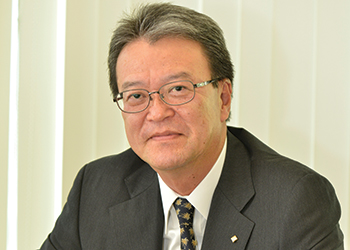
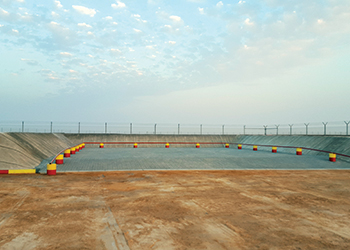
The pathfinding project, executed in November 2016, was successful and Saudi Aramco Haradh Gas Plant officials were very happy with the end result and has recommended the use of CC HydroTM in other projects in the future
Saudi Aramco’s Haradh Gas Plant has pioneered the use of Concrete Canvas in the construction of a pyrophoric treatment area, the works for which were carried out by Saudi-based Freih Bin Owaidha Al Qahtani Sons Co Ltd (FOQSCO).
This was the first application of this material as liner for pyrophoric treatment area in the world, says AbdulRahman O Lashkar, Environmental & Health Coordinator, Haradh Gas Plant.
Reinforced concrete slabs were considered but CC HydroTM (CCH8TM) was chosen because it reduced time and cost and has an expected life time of 50 years.
In total, 800 sq m of CCH8TM was installed within 24 hours (over a four-day period) by five people. CC Hydro was laid transverse using a spreader beam and crane and subsequently cut. Once laid the CC Hydro layers were jointed using wedge welding and hot air gun equipment.
Inspection was done by using spark tester and tensiometer. CC Hydro was anchor trenched and backfilled with marl. Hydration was carried out using a hose attached to a tanker over a course of three days because of dry weather conditions.
The project, executed in November 2016, was successful, Saudi Aramco Haradh Gas Plant officials were very happy with the end result and has recommended the use of CC HydroTM in other projects in the future. They stated they would recommend CC HydroTM to anyone who has similar requirements, says Lashkar.
After evaluation by Saudi Aramco CC HydroTM was approved by its CSD and EPD departments for such applications. An appreciation certificate was also handed over to the contractor FOQSCO in recognition of its efficient work.
'The major factors behind the success of the installation were the dedication and commitment of Haradh Gas Plant team, their great leadership at all levels and cooperation of the work contractor,' he says.
Since pioneering the application of Concrete Canvas by Haradh Gas Plant, it has been used in other various applications by Saudi Aramco as well in light of its fast application, ease of use, cost effectiveness and the fact that it is environment-friendly.
This includes remediation of a water channel in Yanbu Refinery, Saudi Aramco, slope protection of a major area in drill site Saudi Aramco Dhahran and creation of ponds for the wildlife in the Shaybah Widlife Sanctuary under Saudi Aramco. All these projects were time critical and involved access limitations, conditions ideally suited for application for Concrete Canvas.
HARADH GAS PLANT
Saudi Aramco’s Haradh Gas Plant is one of the major gas plants of Saudi Arabia. Located near Haradh village, 300 km southwest of Dhahran, the plant treats gas to produce natural gas and hydrocarbon condensate.
The plant which was officially inaugurated in 2004 was originally scheduled for 37 months but was completed in 31 months, six months ahead of schedule and 27 per cent under budget, exceeding all company quality standards and recorded an amazing 49 million construction man-hours without a lost workday incident. This safety performance was the best in Saudi Aramco’s 71-year-history and a record for the Gulf region1.
The priorities for the Haradh Project were safety, quality, schedule, and cost. With this guidance, the project team was always alert to schedule optimisation opportunities consistent with safety and quality objectives, and this goal was constantly considered in all decisions. This is what ensured that the project was completed well beforehand.
PYROPHORIC TREATMENT AREA
Keeping these guidelines alive in every aspect of its operation since its early days of operation till now even after more than a decade, Haradh Gas Plant has continued to achieve greater heights by evaluating and incorporating cutting-edge technologies. The use of Concrete Canvas for the construction of the Pyrophoric Treatment Area at Haradh Gas Plant is one such example. Pyrophoric Treatment Areas are used to treat materials that when exposed to air can cause them to evolve heat and fire. Due to the potential fire hazard, they need to be treated in a location where they can be contained and this area must be lined with a noncombustible and impermeable lining material (as per per Saudi Aramco Engineering Standard-A-210 Management of Pyrophoric Wastes).
THE CHALLENGES
Pyrophoric Treatment Areas used to be an option that was not 100 per cent reliable, therefore the common practice was not to use this option. Instead, Saudi Aramco facilities used to have temporary storage areas to store these dangerous pyrophoric materials until they are transported to specialised approved waste management companies.
![]() |
Pyrophoric Treatment Area |
Engineers did not pursue treatment areas as they had no reliable material to be used as a liner for them.
The only material that could partially satisfy the requirements was conventional concrete however it could not withstand the heavy weight of the containers and it would start cracking in a short period of time.
The second challenge was the inherent permeability properties of conventional concrete thus allowing for leaching of the hazardous material to the soil and ground water.
This potential cocontamination and pollution of the ground water is not by any means tolerated in Haradh Area where all major dairy farms of Saudi Arabia are located.
A third challenge was the high cost involved in the construction of pyrophoric treatment areas using conventional concrete in addition to the long execution period.
THE SOLUTION
To overcome these challenges, the Haradh Gas Plant environmental team went out and explored various materials in order to construct a reliable Pyrophoric Treatment Area. After a rigorous search and comparing different lining materials they found that the Concrete Canvas material has the properties to meet all their needs that is Concrete Canvas was noncombustible due to its Euro Class B and MSHA ASTP-5011 fire resistance certifications. Concrete Canvas was also impermeable due to its composition which consists of not only a PVC layer at the bottom but also the fibre-reinforced matrix with the concrete mix as well as its chemical resistance.
CONCRETE CANVAS
Concrete Canvas (CC) is a flexible, concrete impregnated fabric that hardens when hydrated to form a thin, durable, water proof and fire resistant concrete layer. CC allows concrete construction without the need for plant or mixing equipment which makes it ideal for use in plants and remote locations.
CC consists of a 3-dimensional fibre matrix containing a specially formulated dry concrete mix. A PVC backing on one surface of the material ensures the material is water proof. The material can be hydrated either by spraying or by being fully immersed in water. Once set, the fibres reinforce the concrete, preventing crack propagation and providing a safe plastic failure mode.
CC provides a quick, cost-effective method of laying concrete that is revolutionising the construction industry. Compared to traditional concrete solutions, CC is faster, easier and, more cost effective to install and has the additional benefit of reducing the environmental impact of concreting works by up to 95 per cent.
Reference
1 Qureshi, M. S. (2004). Haradh Gas Plant projects. Paper presented at PMI® Global Congress 2004—North America, Anaheim, CA. Newtown Square, PA: Project Management Institute.