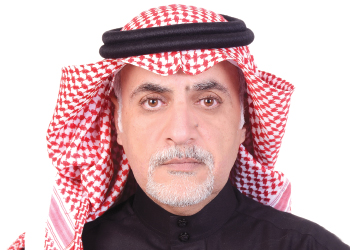
Vega Grieshaber KG is working with process and operation engineers to help improve the safety and reliability of several gas phase reactors, Vega Product Manager, Alexis Alexander tells OGN
In many polyolefin plants, the gas phase reactor is a critical application. Depending on the process, either ethylene or propylene enters a reactor through the bottom. Next, feedstock mixes with a catalyst to form a powdery polymer. This powder forms a bed that becomes less dense the closer it is to the top of the vessel.
Converted gas that reacts with the powder leaves the reactor quickly, and the unconverted gas travels to the top of the vessel until it reaches the disengaging zone. Here, it separates from the powder, leaves the reactor, and is recycled back into the process.
To achieve maximum efficiency, operators want to run the process at the ideal level – not too low, which will decrease the amount of throughput and lead to chunk formation; and not too high, so as to avoid the fines from being carried over through the unreacted gas.
Carry over poses a major threat to the exchangers and other applications, eventually leading to a shutdown and shortening the production cycle.
DPTS—THE TRADITIONAL APPROACH
Differential pressure transmitters (DPTs) are most commonly used to measure and control the reactor bed level. The mass of the fluidised product bed exerts a hydrostatic pressure, which is measured to infer level. But when the product is denser than the original calibrated value, the level measurement will appear higher than it is and vice versa when less dense.
Compared to the measurement errors from the changing density, the greater issue for operations is the amount of maintenance DPTs require.
Small polymer chunks can strike and damage transmitter seals leading to maintenance-related errors. But more commonly, buildup can occur where the sensor is installed, leading to intermittent clean-outs, leaving operators without any measurements for control.
Because of the multiple possible errors, operators eventually lose faith in their measurement and begin to operate at a lower than optimal level.
USING RADIOMETRIC
Radiometric technology is a reliable and accurate technology used in critical applications where standard measurements fail. A radioactive isotope emits gamma radiations from a source holder, and the radiation attenuates as it passes through the vessel and the material inside.
Using the amount of gamma radiation reaching the measurement area, radiometric sensors from Vega called the Protrac 30 series can calculate a number of measurements, including point level, density, and continuous level. Both the source holder and the sensor are mounted externally, leaving nothing to interfere with the process within the vessel.
A common mistake among radiation solution providers would be to size and measure the level using one continuous detector. A single radiometric detector cannot accurately detect level for the same reason differential pressure cannot accurately detect continuous level-varying densities.
The fines near the top block very little radiation while the fluidised bed at the bottom blocks a significant portion. This large gradient delivers a poor measurement resolution.
Vega, a German manufacturer for level and pressure instruments, is known for its specialty in radiation based measurements.
Using multiple detectors, like Vega’s Fibertrac 31 or Solitrac 31, to segment the measurement throughout the vessel can give operators a continuous level measurement as well as monitor the fines. Each sensor simultaneously acts as an individual level measurement for its designated section of the vessel while providing a portion of the total level for the entire vessel.
The total level, thanks to Protrac multigauge communication, will provide a computed 4-20 mA signal for controlling the leading edge of the fluidised bed.
At the same time, the segmented detectors can individually indicate any fines floating above. That’s because each level sensor is simultaneously acting as individual densitometers.
The level sensors can provide a density output for the fines while also providing a level reading of the fluidised bed. This solution gives operators the control and the resolution needed to optimise the process inside the gas phase reactor.
Providing an accurate continuous level measurement with carryover detection to operators can give them the confidence needed to run the gas phase reactor at its full potential.