
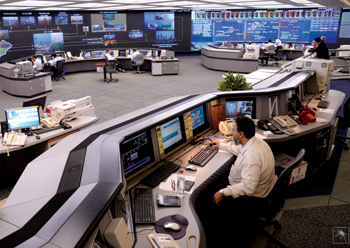
Encompassing innovations from electronic work packages to big data analytics and cloud platforms in operations will be critical to leveraging data in the pursuit of operational excellence and securing profitability now and in the future
Asset-heavy industries are facing mounting pressure from tightening operating and capital expense budgets, as plant managers strive to improve safety and productivity while training and retaining experienced operators. These challenges are exacerbated by the Covid-19 pandemic and prompt a pressing need to optimise the allocation and maintenance of assets to maximise returns.
The potential savings in time, money, effort and, ultimately, lives offered by the digitalisation of the chemical, petrochemical, oil and gas industries make a compelling argument to adopt cutting-edge technology into asset performance management (APM) strategies to achieve operational excellence, said a Reuters Events report produced in association with Downstream USA 2021, a digital conference that will be held from October 12-15, in Houston, US
Digital technology such as machine learning (ML), artificial intelligence (AI), big data, and the Industrial Internet of Things (IIoT) offer an array of tools to realise the optimisation of asset performance including predictive maintenance that drives safer, more reliable operations.
Intensive manufacturing and industrial businesses are turning to digital APM strategies as they seek not only to optimise physical assets, but also organisation-wide resources in a bid to increase reliability, minimise costs, and reduce operational risks.
Pressure to minimise workplace risks and improve safety intensified in August 2020 when more than 2,700 tonnes of ammonium nitrate (AN) stored at Port Beirut in Lebanon exploded in one of the largest non-nuclear detonations ever recorded. More than 200 people lost their lives.
Port Beirut was the latest in a history of major incidences, which began with AN blasts at the Oppau plant, Germany, in 1921, through to the explosions on the Piper Alpha off-shore oil platform in the North Sea in 1988. Notably, the release of toxins from the Seveso plant, Italy, in 1976, led to the Seveso Directive on technological disaster risk reduction that underpins many safety initiatives.
In 2018, Deloitte Insights conducted a survey on company investment in capabilities driven by Industry 4.0 to enable digital transformation (DX). Oil and gas leaders rated big data derived from APM programs as the most likely to provide the greatest business value.
However, the survey also found that although there was strong interest in DX, some organisations were still trying to strike a balance between improving their current operations and the innovations offered by Industry 4.0. And even though 94 per cent of respondents understood the importance of DX, the strategic possibilities were not necessarily being fully explored as fewer (68 per cent) saw DX as a path to profitability.
Deloitte extrapolated these findings to conclude that APM could deliver more than just improved maintenance. Connecting systems across an entire organisation would reveal insights to optimise operations and safety, yielding better financial results. As the IIoT is pivotal to equipment reliability, APM strategies that connect multiple data points will play a major role in driving these improvements.
Allied asset-heavy industries are successfully applying DX to operations and employing data analytics to minimise downtimes and drive down maintenance costs. The US Nuclear Energy Institute (NEI) launched an initiative in 2016 to strengthen the nuclear power industry’s commitment to safety and reliability while assuring future viability through efficiency improvements.
Nuclear operators embarked on DX journeys in which technological and operational changes that could enhance safety and efficiency were identified. APM programs integrating predictive analytics that drive condition- and value-based maintenance strategies were implemented and the widespread adoption of innovative tools that could reduce costs encouraged.
However, nuclear companies soon realised that digital opportunities reside not only in enhancing asset performance through predictive maintenance and asset strategy optimisation, but also in operations optimisation. In particular, on-site work execution involving complex processes had become increasingly cumbersome.
The Electric Power Research Institute (EPRI) proposed that the digitalisation of work would enable these processes to be carried out electronically in the field, thereby improving efficiency without compromising safety.
In 2020, EPRI published data that showed electronic work packages (eWP) are now a primary innovation tool for integrating work activities with basic plant work processes, eliminating several costly activities associated with paper-based procedures. Mobile work management platforms are now accepted by the industry, with more than half the US nuclear fleet deploying an eWP solution.
Implementing holistic APM strategies that streamline digitalisation across an entire organisation from on-site daily work processes to physical assets and knowledge management, will be pivotal to the successful and complete digital transformation of any business. Encompassing innovations from eWPs to big data analytics and cloud platforms in operations will be critical to leveraging data in the pursuit of operational excellence and securing profitability now and in the future.
FUNDAMENTAL PILLARS
Deloitte outlined the common challenges facing most asset-intensive organisations, including more stringent regulations, especially with regard to safety, as well as manual uncoordinated work processes and a lack of knowledge management systems. These challenges could be addressed by broadening the scope of APM beyond maintenance to include the key business areas of the physical and mechanical, operational, as well as the environment, health, and safety (EHS).
EHS was particularly identified as needing a shift from compliance to prevention and APM was cited as a potential tool to minimise risk and improve safety. This would, in turn, lower insurance costs while strengthening the reliability of assets and, therefore, the reliability of operations.
Implementing APM offers the opportunity to accelerate digitalisation of any plant, which potentially generates more trusted data that enables swifter and sounder decision-making. It also offers a broadened view of optimisation, bringing together the people, processes, and technological aspects of operations to provide an effective mechanism for optimising asset management.
• People, who drive and manage the solution, are responsible for creating and sharing knowledge on APM within the plant and across industries and making informed and timely decisions that ultimately affects risks, costs, and performance.
But this can never be achieved without a culture that supports, promotes, and ultimately delivers a safe and reliable performance. This culture is founded in organisational alignment of and commitment to achieving safe and reliable operations, as well as always striving for improvement. Such a culture is underpinned by consistent messaging and communications from top management throughout the organisation so that reliability and safety excellence are seen as the norm.
There are a number of challenges to overcome including historic work practices that may involve taking unnecessary risks. For example, there may be pressure to complete tasks as quickly as possible to minimise losses but which result in taking potentially hazardous short cuts. Cumbersome processes that make safely controlling work difficult to achieve will not deliver the required level of reliability. In addition, third-party organisations, such as external contractors working on the plant, might not be familiar with or fully committed to on-site requirements.
A key aspect to achieving an innovative, engaged, and empowered working environment is making sure people feel listened to and respected. Decision-making must be delegated to the right organisational levels, thus empowering the workforce to drive performance in the right direction. Recognition and positive constructive feedback are critical to ensuring everyone understands how their performance contributes to business successes.
• Processes: Effective APM processes achieve better reliability, safety, and, ultimately, profitability. They are a vital part of asset management and define the way in which different scenarios are approached and managed, facilitating compliance with defined expectations. This drives consistency across people and teams to ensure that activities are completed safely.
A clear and well-defined work process should provide the steps required to complete tasks in a safe and effective manner by preventing unsafe actions that result in accidents and incidents. Continuous improvement ensures that current people, processes, and technology are in line with the requirements and demands of today and, to some extent, the future. Training and knowledge sharing sit alongside continuous improvement.
Digital tools provide an efficient mechanism for applying the right processes, standards, and asset strategies to quickly assemble all necessary information for the safe control of work. Wearable technologies can help the user to visualise different aspects related to a given job, such as technical data and drawings, whilst being hands-free and contributing to safety and execution efficiency.
• Technology complements the APM paradigm by making strategies more data-driven and risk-based. It enables comprehensive decision-making processes because it brings together a wealth of data that humans may not be able to access under normal circumstances. It is critical to ensuring APM strategies are effective, especially now the market is moving towards more connectedness and almost instantaneous feedback.
Technology augments the value of the other two pillars. It connects the right people to the right data at the right time, providing additional intelligence and oversight to make informed decisions. And it ensures asset and process knowledge continuity when subject-matter experts retire from or leave the company.
APM strategies are optimised by having access to as much relevant data as possible. Therefore, technologies related to data ingestion such as the IIoT, integration using cloud platforms, processing including ML and AI, and visualisation using digital twins, will lead and drive DX for APM. Overall, safety is one of the most important risks to consider. There is a direct connection between reactive maintenance and safety incidents. When reactive maintenance is performed, maintenance workers tend to hurry to prevent further damage. This leads to unnecessary risks, human error, and increased maintenance costs.
FUTURE STRATEGY FOR APM
Digital transformation is necessary if asset-heavy industry is to remain competitive and secure a viable future. Safety of the workforce and neighbouring communities is paramount not only to lower costs associated with major incidences, but to maintain engaged employees who will be the main drivers behind the processes and technology deployed to achieve operational excellence.
A holistic APM program offers greater connectivity across an entire organisation and optimum reliability, efficiency, and profitability. Sound change management from leaders that involve staff at all levels will be critical to that program’s success, especially as the technologies that power APM will continue to advance and must be embraced and understood to achieve optimal performance.