
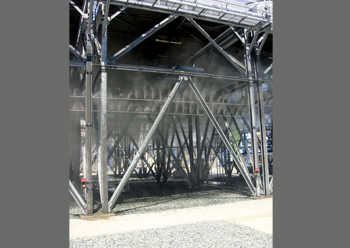
The Coolingmist and LNG Screen Tech systems work to boost ACHE capacity on hot summer days, positively impacting the production process and in turn helping increase plant throughput as a whole, Marc Ellmer, Managing Director, Elbrons, tells OGN
Avast majority of all air cooled heat exchangers (ACHEs) in operation in plants are underperforming. As a result, the product flow during hot summer days has to be reduced to achieve the required product temperature or pressure in the column thus leading to a loss of revenue for the plant owners.
Elbrons, a market leader in the air cooler and engineering industry, offers two new innovative techniques as a solution to this problem — the Coolingmist and LNG Screen Tech.
'The Coolingmist is a high-pressure fogging system (chilling, peak cooling, adiabatic cooling) that is used to influence ambient climatic conditions. It has explicitly been designed for the energy, petrochemical, and oil and gas industry to address the requirement for increasing cooling/condensing capacity,' Marc Ellmer, Managing Director, Elbrons, tells Abdulaziz Khattak of OGN.
The system achieves adiabatic cooling by evaporating billions of micro-fine droplets in the inlet air of an ACHE. The evaporative effect results in a drop in inlet temperature, thereby increasing efficiency substantially. This also directly positively impacts the production process.
The Coolingmist system can be tailored to every individual situation and environment. It guarantees, at least, 95 per cent evaporation of the water (evaporative cooling), thus resulting in a system that has a very high performance and with no damage to the static or mechanical equipment. Minimum water is consumed for a maximum cooling effect.
During hot summer days especially, a strong inverse relationship exists between the dry bulb temperature and relative humidity.
When the ambient temperatures reach a high level, the coincident relative humidity gets invariably lower. The Coolingmist makes use of this typical weather phenomenon and, therefore, cools down the air by as much as 12 deg C in hot and dry climates.
The system offers numerous clear advantages to the end user such as an immediate measurable positive cooling effect; maximum evaporation capacity; adjustable cooling to the desired level (a multistage system); no negative effect on airflow; adaptability to any existing air cooler or air condenser unit; and no increase in existing noise level of air coolers.
The Coolingmist has a fast installation time and requires minimum space. With low capital expenditure, it has barely any operational and maintenance costs and offers rapid payback. There is no need for structural modification or drilling of the support structure.
Only top quality materials such as SS316 are used in the system’s manufacturing.
In order to illustrate the potential of a high efficiency fogging system, Elbrons used the thermal engineering software of HTRI to simulate ACHE performance at different degrees of cooling. The design case consists of design conditions that are very common for a propane condenser installed within industrial environments. The results of the thermal calculations are used to indicate potential improvement and provide independent recommendations within the performance of the ACHE.
• LNG Screen Tech: The challenges for large air-cooler banks from wind are many. For ex¬ample, a common problem is the adverse effects of air recirculation where hot air from the air cooler is sucked back into its inlet.
This is due to a difference in pressure between the inlet and outlet sides of the air cooler. The impact of hot air recircu¬lation on ACHE performance can be disastrous.
Elbrons has introduced the LNG Screen Tech for these operational challenges.
'This product was specially developed for LNG, GTL and petrochemical air coolers. Strong side winds can also cause vibrations and fatigue such as belt failures, bearing failures, blade failures, etc,' says Ellmer.
The specially designed LNG Screen Tech fire retardant screen with unique mash ensures a constant airflow instead of wind fluctuations under the fan or bundle. It also reduces wind velocities entering the ACHE inlet. These aspects limit production loss by preventing hot air recirculation (HAR), typically observed on large air-cooler trains.
Additionally, the LNG Screen Tech ensures constant maximum plant throughput over long periods at different wind strength and direction as it creates an 'over pressure' at the fan inlet and stabilises the wind velocities entering the ACHE. This enables plant owners to reduce or limit hot air recirculation, which in turn increases plant throughput as a whole.
The LNG Screen Tech is made from PVC coated polyester material and offers flame retardant and rot-proof properties. It’s anti-static and anti-bacterial, in additino to being lightweight with a UV stabilised screen. The system has a temperature ranging from -45 deg C to +70 deg C.
The screens of the LNG Screen Tech are, as a standard, tested up to 160 kmph wind, but high wind specifications of up to 196 km/h can also be met, if required
The system requires no hot work permit during installation as there is no need for welding or drilling. It’s maintenance-free and has tailor-made components. It can also be installed during operation
To illustrate the possible gains in capacity of the Lng Screen Tech, Elbrons BV has conducted various thermal calculations using HTRI’s thermal engineering software.
Elbrons is well-known for its deep expertise in helping over 200 energy, petrochemical, and oil and gas customers globally. The company leads the way in ground-breaking and innovative technologies for air-cooled heat exchanger capacity enhancement, and holds multiple worldwide patents in this regard, particularly for the use of the specially designed Coolingmist and LNG Screen Tech.