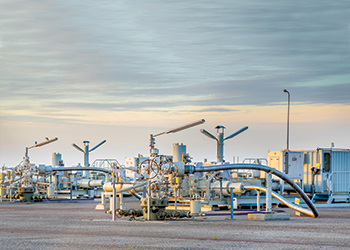
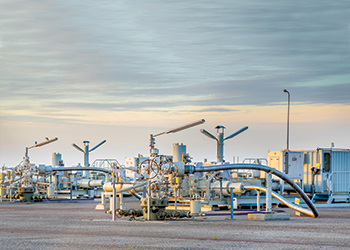
Investing in innovative equipment, operators can significantly lower their carbon emissions,
reduce energy consumption and prevent gas leakages
Compressors have been identified as an emission source that has the potential to produce emissions into the atmosphere during oil and gas production, processing, transmission and storage.
By increasing the efficiency of compressors, operators can directly reduce energy-related emissions and save money, improve operations, decrease emissions and increase competitiveness, while fighting global warming a the same time.
Compressors are mechanical devices that increase the pressure of natural gas and allow the natural gas to be transported from the production site, through the supply chain, and to the consumer.
The oil and natural gas exploration and production industry globally is highly dynamic and growing rapidly. Consequently, the number of wells in service and the likelihood for greater air emissions from oil and natural gas sources is also growing.
In the US, for example, it is estimated that there are around 504,000 gas producing wells and an estimated 536,000 oil wells.
Meanwhile, globally the increase is said to be substantial in the future as oil and natural gas production is projected to steadily increase over the next two decades.
![]() |
Innovative compressors can significantly prevent gas leakages |
Specifically, natural gas development is expected to increase by 44 per cent by 2040; and crude oil and natural gas liquids are projected to increase by approximately 25 per cent.
The projected growth is primarily led by the increased development of shale gas, tight gas, and coalbed methane resources utilising new production technology and techniques such as horizontal drilling and hydraulic fracturing.
Based on this increased development and the fact that half of these new oil wells co-produce natural gas, the potential exists for increased emissions from production through distribution of natural gas from these operations.
During energy production, large amounts of CO2 are produced as waste byproducts. The inefficient use of typical mechanical equipment, like reciprocating compressors can add to this problem by producing additional unnecessary CO2 emissions.
Vented emissions from compressors occur from seals (wet seal compressors) or packing surrounding the mechanical compression components (reciprocating compressors) of the compressor.
These emissions typically increase over time as the compressor components begin to degrade and leak emissions from various compressor components can also occur.
This overview summarises the vented VOC and methane emissions from compressors and looks at the available mitigation techniques (practices and equipment) to reduce vented emissions from compressors.
Included in the mitigation techniques discussion is the understanding of the efficacy and cost of these technologies and the prevalence of use of the technologies in the industry.
In the oil and natural gas sector, the most prevalent types of compressors used are reciprocating and centrifugal compressors.
• Reciprocating compressor: Simply stated a reciprocating compressor is defined as a piece of equipment that increases the pressure of a process gas by positive displacement, employing linear movement of the driveshaft.
Compressors are used in all aspects of natural gas development. In the production segment, compressors are used at the wellhead to compress gas for fluids removal and pressure equalisation with gathering equipment systems.
However, the primary use of compressors is in the natural gas processing, transmission and storage (particularly underground storage) segments of the industry.
In a reciprocating compressor, natural gas enters the suction manifold, and then flows into a compression cylinder where it is compressed by a piston driven in a reciprocating motion by the crankshaft powered by an internal combustion engine.
A reciprocating compressor rod packing is defined to mean a series of flexible rings in machined metal cups that fit around the reciprocating compressor piston rod to create a seal limiting the amount of compressed natural gas that escapes to the atmosphere.
Over the operating life of the compressor, the rings become worn and the packing system will begin to wear resulting in higher leak rates.
Emissions from packing systems originate from mainly four components; the nose gasket, between the packing cups, around the rings, and between the rings and the shaft. Typically, gases leaked from the packing system are vented.
• Centrifugal compressor: This kind can be defined as any machine for raising the pressure of a natural gas by drawing in low pressure natural gas and discharging significantly higher pressure natural gas by means of mechanical rotating vanes or impellers.
Centrifugal compressors use a rotating disk or impeller to increase the velocity of the gas where it is directed to a divergent duct section that converts the velocity energy to pressure energy.
These compressors are primarily used for continuous, stationary transport of natural gas and are widely used in the processing and transmission industry segments.
Centrifugal compressors are equipped with either a wet or dry seal configuration. Wet seals use oil around the rotating shaft to prevent natural gas from escaping where the compressor shaft exits the compressor casing.
The oil is circulated at high pressure to form a barrier against compressed natural gas leakage. The circulated oil entrains and absorbs some compressed natural gas that may be released to the atmosphere during the seal oil recirculation process (degassing or off-gassing).
Alternatively, dry seal compressors use the opposing force created by hydrodynamic grooves and springs to provide a seal. The opposing forces create a thin gap of high-pressure gas between the rings through which little gas can leak.
The rings do not wear or need lubrication because they are not in contact with each other. The combination of two or more of the dry seals.
Gas emissions from wet seal centrifugal compressors have been found to be higher than dry seals compressors primarily due to the off-gassing of the entrained gas from the oil. This gas is not suitable for sale and is either released to the atmosphere, flared, or routed back to a process.
In addition to lower gas leakage (and therefore lower emissions), dry seals have been found to have lower operation and maintenance costs than wet seal compressors because they are a mechanically simpler design, require less power to operate, are more reliable and require less maintenance.
Hydrogen is a key element in the green energy transition. It is also here that compressors will play an important part to allow wide use of hydrogen for mobility and trailer filling.
Transport and storage of hydrogen will be a central issue of the future hydrogen economy. Independent from the type of production, transport and storage, there is a need for efficient compression solutions along the entire hydrogen value chain.
By using innovative products and services in compressors, operators can significantly lower their carbon emissions, reduce energy consumption and prevent gas leakages.