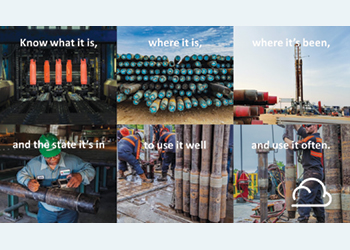
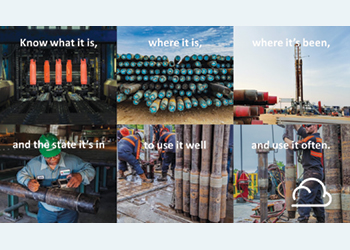
By leveraging a combination of propriety hardware and software, NOV can help asset owners identify, locate, evaluate, and manage globally dispersed drill string components, says Raffoul Raffoul, Senior Vice-President of Sales NOV Wellbore Technologies, Middle East
In today’s environment, every company in the oil and gas industry is looking for new ways to increase efficiency and accurately manage/lower its spend. When looking at ways to helping customers achieve these goals, proper lifecycle management of drill pipes was identified as highly beneficial in providing confidence, clarity, and cost savings.
Information provided as part of a customer analysis revealed that the year-to-date non-productive time (NPT) incident rate for drill pipe failure has increased 100 per cent from the previous typical rates. At this rate, the cost will be more than $25 million.
In addition, an ageing inventory provides an increased NPT risk since 75 per cent of the expansive fleet are six years or older. To add to the severity, the current 4 million ft of pipe includes 24 different types of grades and connections. This is a vast array of drill pipe that all requires tracking and tracing, which is typically done manually through spreadsheets.
![]() |
A worn out serial number on a drill pipe |
By not being able to properly identify drill string components and their state of readiness, it can lead to improper use and unnecessary inspection that results in avoidable NPT and increased inventory and maintenance spend.
It was determined that a complete lifecycle management option would be valuable as it eliminates the guess work around how to best use and maintain tools such as drill pipe.
By integrating several established technologies from our NOV Wellbore Technologies segment, we developed a complete solution that allows asset owners to easily tag, track, trace, and tally their drill pipe.
By leveraging a combination of propriety hardware and software enabled by radiofrequency identification (RFID), NOV can now help asset owners identify, locate, evaluate, and manage globally dispersed drill string components to gain much-needed confidence, clarity, and cost savings.
Owners can easily track RFID-tagged assets and capture their history — from manufacture to retirement — using configurable, cloud-based web and mobile applications that make individual asset information available immediately when most needed.
A complete view of an asset’s state of readiness is available by utilising supplemental asset records with downhole usage by well section and inspection and maintenance summaries.
![]() |
The M/D Totco AutoTally real-time pipe tally system provides usage data to |
By leveraging downhole usage data, asset owners can now switch to usage-based inspections. This allows them to rotate pipe based off actual environmental exposure, resulting in significant cost reductions, extending asset life, and ensuring expected performance of assets (Figure 1).
Leveraging a complete lifecycle management solution to reduce NPT attributed to drill pipe and lowering inventory spend is a multi-step process undertaken by NOV as a comprehensive solution tailored to the customer’s requirements.
The process begins with the customer investing in premium drill pipe, such as NOV’s Grant Prideco Delta rotary-shouldered drill pipe connection, which has wider field tolerances and reduced repair frequency.
The Delta connection is easier to run, more robust, and more forgiving to improve total cost of ownership of drill pipe. The connection has a 66 per cent reduced repair frequency and 50 per cent faster makeup compared to the XT connection.
Once a drill pipe is selected, the customer then needs to care for that investment with premium service. In conjunction with a complete package of drill pipe service and repair offerings, Tuboscope TruData inspection and reporting software provides customers critical inspection data by serial number in an easy-to-read format.
Detailed repair and maintenance history across the fleet along with in-depth asset categorisation and reporting enables customers to maximise their investment by immediately capturing and consolidating trusted asset information to make informed decisions. This allows customers to confidently distinguish assets that are ready for use from those that are unsuitable for operations, ensuring that assets perform as intended when and where they are needed.
This eliminates the increased risk of NPT that comes with assets being sent to the field that have lapsed inspections or otherwise quarantined. It also allows for the customer to easily know what they have and where, so they can maintain accurate inventories across locations and identify the exact location of specific assets when required.
Previously, an operator would report damaged pipe returns to the yard without being be able to identify the rig that was causing the handling damage since specific assets that went to each location were not tracked.
The challenge that many face is that they are not able to collect all this valuable information through serial numbers that cannot be read accurately. While stamped serial numbers are the standard, they are often worn out and difficult to read. These illegible serial numbers lead to misidentification, which result in inaccurate records.
With our Tuboscope TracID RFID tags, serial numbers appear upon scanning. While common in many industries – and even elsewhere in oil and gas – RFID tags are rare for drill string components due to the need for them to survive extreme downhole conditions characterised by high temperature, pressure, and vibration.
However, our field-proven TracID tags are built to last downhole and deliver 99.5 per cent tag readability. Enhanced by using TracID tags and complementary handheld readers, the Max Track asset-tracking software provides the ability to identify, locate, evaluate, and manage dispersed assets by serial number.
Max Track asset-tracking software provides authorised users with information needed to determine suitability and readiness by serial number, including, but not limited to asset specification, last-known location and status, and in most importantly in recent history those ‘events’ captured by other proprietary NOV software previously mentioned. Max Track enables customers to eliminate guesswork and confidently manage their assets.
Lastly, the M/D Totco AutoTally real-time pipe tally system provides usage data to improve pipe management for both owners and operators, and improves safety and efficiency by removing the need to mark and measure each joint at the wellsite.
With an RFID antenna installed under the rotary table, each tagged asset is recorded as it enters and exits the well, automatically updating usage and tally history by serial number.
Operational information is available at the rig site through a touch-screen human machine interface in the driller’s cabin, and tally and usage history appear directly in Max Track. You can easily set thresholds in Max Track and receive visual threshold notifications on a rig-site display to evaluate assets before using them downhole and identify assets to shuffle into use after each trip. This optimises rig inventory management to ensure minimal NPT.
Drill pipe lifecycle management enables customers to know their assets, simplify workflows, and reduce unwanted spend with clear, detailed asset information centralised in Max Track.