
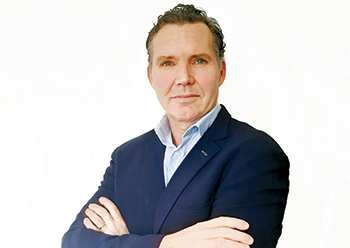
The latest generation of Faccin HAV series, a three-roll bending machine with variable geometry, offer energy savings of up to 50 per cent compared to a normal hydraulic or mechanical bending machine, says Javier Lanfranchi, Faccin Group’s Senior Sales Area Manager
Pressure vessel manufacturers are constantly faced with challenges and changes in their production, driven either by cost reduction demand due to new players entering this lucrative but competitive market, or new government or environmental rules and regulations.
For instance, everyone is talking about carbon dioxide (CO2) reduction since carbon emissions need to be reduced drastically in the next 10 years. In this regard, the standard ISO 50001 was created for organisations committed to addressing their impact, conserving resources and improving the bottom line through efficient energy management systems (EnMS) so as to help find and implement energy saving options in their production lines.
![]() |
Elliptical tanks from Faccin’s dished head production lines |
The Middle East is no exception, says Javier Lanfranchi, Faccin Group’s Senior Sales Area Manager.
'The Kingdom of Saudi Arabia, spearheaded by its national oil company Saudi Aramco, has taken the ambitious strategic decision to involve more domestic companies in the development of the country’s infrastructure, and as consequence, an important flow of investment in machinery and equipment is taking place.'
Aramco’s goal is to purchase 75 per cent of all its material needs locally by 2021, thus increasing the energy consumption of its industrial network and, therefore, making energy efficiency a must-have feature in all the new machinery to be acquired by Saudi enterprises.
Lanfranchi says modern efficient machines help achieve energy saving goals set by manufacturers and governments by using the latest technology available. Accordingly, steel plate bending machines are an integral part in the production line of pressure vessels fabrication.
'Imagine if a plate roller could save up to 50 per cent in energy costs. Can CO2 emissions be reduced by installing a state-of-the-art bending roll in the production line?' he asks.
'The answer is yes; with the latest generation of Faccin HAV series, a three-roll bending machine with variable geometry.'
Lanfranchi explains: 'If we look at the energy flow of metal forming machines, it is ultimately electrical energy that is used to activate the machine. The HAV series uses completely hydraulic drives so that energy is absorbed by the electric motors for the hydraulic unit. To reduce energy consumption, the motors must be used as efficiently as possible.'
Faccin has integrated several innovations in the new HAV series that enable the manufacturer to use significantly less operating energy.
On the one hand, every Faccin HAV bending machine has the Faccin AP package. This includes fully proportional hydraulic control of the rotation and the rolls movement.
In addition, it allows simultaneous movements of several axes, so that while the steel plate is being fed in, the rotation and the lowering of the top roll can be operated at the same time as the central or side support, which can be moved during the rotating movement. This means the rolling process can be carried out more efficiently and quickly, significantly reducing energy consumption.
The Faccin AP package also includes an automatic shutdown of the hydraulics after several minutes of idling thus minimising unnecessary power consumption.
Another innovation on the HAV machine is the two identical variable axial piston pumps system.
The hydraulics are based on two hydraulic pumps that supply the hydraulics with pressure in equal parts. This means the machine can be operated with just one pump when the power requirement is low. This is particularly helpful in flexible production processes, where the maximum load is not always required, in order to reduce energy consumption.
Another advantage of this is the high reliability of the machine. So even if there is a defect in one pump, the other pump continues to keep the machine working.
With these changes, which are standard in the HAV series, energy savings of up to 50 per cent are possible compared to a normal hydraulic or mechanical bending machine.
Lanfranchi says companies in the Middle East are aware of the importance of finding the right partner for their most-challenging energy-efficient rolling projects.
'When we looked at the market to find the right supplier for this investment, we found Faccin as the most suitable manufacturer,' said James Brazier, Operation Director, Serck Services Gulf.
'Their three-roll variable geometry HAV model with the advanced Faccin AP package for higher productivity, pre-bending precision with the shortest flat end and versatility to roll different thicknesses and diameters, was an exact match to our requirements for heat exchanger manufacturing.
'We want to offer our customers the best possible equipment and we do this by having the best possible manufacturing technology available.
The machines that Faccin currently have in the Middle East and the positive feedback we heard by other Faccin customers did the rest,' he said.
Part of the reliable and powerful Faccin Group, Faccin is a leading global metal forming machine producer that manufactures and commercialises three major brands: Faccin, Roundo and Boldrini.
It offers the widest range of plate rolls, angle rolls, dished head lines and special machines from small to large capacities, standard or tailored to customer needs, all with one feature in common: long-lasting guaranteed performances.