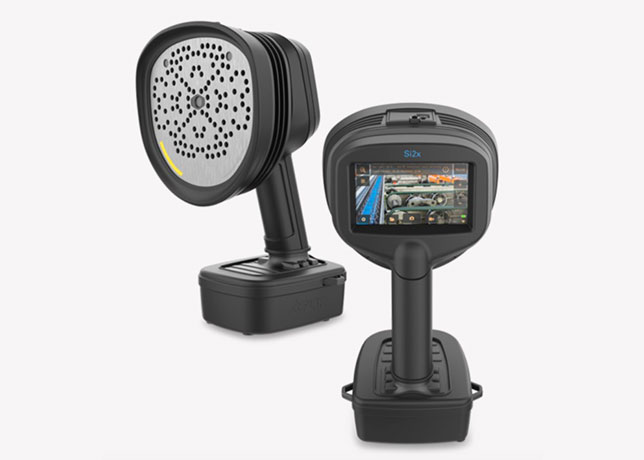
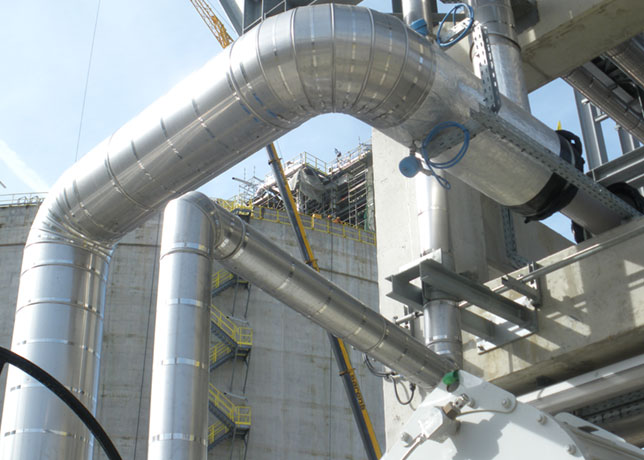
While identifying challenges early in LNG facility design enhances safety and longevity, cellular glass insulation effectively reduces fire risks, moisture, and noise while supporting storage tanks without compromising thermal performance
Demand for LNG is rising as the world shifts toward lower-carbon energy systems, prompting the planning and announcement of new terminals to meet this need.
Facility designers, engineers, and contractors encounter a range of challenges related to location, layout, and operational temperatures.
This article explores several common challenges in insulating LNG facilities and demonstrates how cellular glass insulation helps engineers and facility managers address these issues while enhancing safety, minimising maintenance and labour, and improving the workplace environment.
THERMAL PERFORMANCE
LNG facilities require insulation systems to address thermal performance at extreme temperatures. Equipment throughout these sites can operate at -162 deg C and this means reliable and long-lasting insulation is needed to keep pipes and storage tanks at temperature without warping.
When insulation is subject to extreme temperatures, there can be a rate of thermal expansion or contraction.
Organic-based insulations tend to have a larger coefficient of thermal expansion than insulation types that are non-organic.
Some organic materials – like plastic foams – can have coefficients that are five to ten times larger than those presented by metal materials.
This difference can lead to open joints and allow for unwanted heat gain – reducing the overall thermal efficiency of the system. The movement also may allow entry points for moisture or water vapour.
However, using FOAMGLAS® cellular glass insulation, which can function in temperatures ranging from -265 deg C to 430 deg C, provides a minimal coefficient of thermal contraction similar to that seen with carbon or stainless steel and concrete.
Unlike polyisocyanurate, use of cellular glass insulation in situations where extreme temperatures occur can help protect joint seals and keep moisture from entering an insulated system during temperature cycling.
MOISTURE PROTECTION
Despite the cold temperature of the pipes, LNG facilities may face a particular challenge from moisture and corrosion as many are located in locations with humid, or warm and humid climates.
![]() |
FOAMGLAS can reduce toxic smoke generation and help improve the safety of an LNG facility |
Pipes or vessels may function at temperatures reaching down to -162 deg C, but they can be located in areas where the ambient temperature remains 30 deg C or higher with high humidity.
As moisture seeks to move from hot conditions to cold ones, the combination of cold pipes or tanks and warm outside temperature drives moisture to insulation.
Adding permeable or absorptive insulation to a cold pipe can create a dew point where moisture can collect and potentially freeze within the insulation even if it does not reach the pipe.
According to information from ASHRAE, about 98 per cent of insulation failures are linked to moisture. The collection of ice within insulation also can add weight to the pipe and reduce the lifespan of equipment.
Cellular glass insulation is long-lasting, impermeable and can help protect LNG systems from invasion by moisture or water vapor.
COMPRESSIVE STRENGTH & EQUIPMENT SUPPORT
The need for comprehensive strength can be an overlooked piece when insulation is selected for an LNG facility.
However, it remains a necessary element in insulation choice – especially when working with tank bases, piping or vessels.
The failure of insulation materials from compression can hasten deterioration of the insulation system and result in mechanical system or equipment damage.
When insulation is used on pipe supports and hangers, providing a material with a high compression strength allows for supports to be used on the outside of an insulation system – which helps prevent thermal breaks in the system.
If an insulated pipe fails, it can alter how a load is distributed. When that occurs, the entire system may surpass its stress tolerance.
Damage, including increased leak or rupture risk, is particularly possible at sensitive areas such as nozzles, flanges and fittings following a system imbalance.
When insulation is used on storage tank bases - a compressible insulation could cause a drop in thermal insulation performance or unwanted settlement of the structure.
If not stopped, these situations could continue to degrade leading to ground heaving or even system failure from ruptures in the bottom of tanks as foundation temperatures exceed limits.
There also needs to be an awareness of how insulation functions with extreme temperatures. Long-term creep can occur when extreme temperatures are applied to insulation or the accessories used with insulation.
Compression creep may start when a solid material deforms or moves after a mechanical load is applied.
The compressive properties of FOAMGLAS® insulation are consistent over time and across a wide range of service temperatures. It has been tested against ASTM C165, EN 826, ASTM C552-17 and EN 14305.3
Cellular glass insulation is capable of supporting heavier loads than many other insulating materials.
FOAMGLAS® insulation tolerates a range of compression and has declared compressive strengths of 800 kPA to 2,400 kPA.
Its compressive strength and dimensional stability cut the need for additional treatment at pipe supports and allows it to be used under storage tanks.
Cellular glass insulation provides a stable base for heavy storage tanks and can be used with cryogenic tanks to limit heat gain and preserve system lifespan.
FIRE PROTECTION & SUPPRESSION
Because LNG is a mixture of low-molecular-weight hydrocarbons risk of fire on site is a consideration. As site locations shrink and move toward populated areas – there is increased interest in developing new ways to mitigate fire risks. Insulation systems can contribute to fire protection by providing heat absorption and thermal protection to reduce the rate of temperature rise towards the item being protected. When specifying insulation systems for passive fire protection of structural steel, equipment, piping and hydrocarbon storage tanks, engineers should consider relevant material properties, the process environment and the required level of fire protection.
Materials properties such as combustibility, absorbability, smoke development and possible loss of mass in case of a fire can help determine which products would be most suited for a set of design considerations and environmental conditions.
Selection of a non-combustible insulation and one that does not wick or absorb flammable liquid – like FOAMGLAS® - can reduce the opportunity for toxic smoke generation and help improve the safety of an LNG facility.
NOISE
LNG facilities can be loud - especially when liquification and regasification occur - and employees may need hearing protection to meet 85db regulations and facility location and zoning requirements.
But selecting the right types of insulation can help with noise mitigation as it remains easier to treat the problem at its source than remediate it.
A combination of cellular glass insulation and mineral wool can insulate cold and cryogenic pipes and meet class C and D acoustic compliance using less material than is needed in other systems.
The reduced amount of mass and cladding can help with ease of installation and handling, potentially lowering labour costs. Additionally, the thinner amount of material needed drops the amount of weight added to piping.
The application overfits a base layer of cellular glass insulation with mineral wool to provide additional acoustic performance.
Mineral wool insulation provides a fibrous layer to help sites meet ISO 15665 compliance.
Owens Corning® mineral wool insulation pipe insulation is water-repellant and non-combustible; however, it should be used with appropriate vapor barrier jacketing, mass-loaded vinyl and recommended accessories.
CONCLUSION
Although LNG facilities face numerous challenges to operations and safety, starting the design process with them identified can help protect the functioning and longevity of the site while protecting employee safety.
While several kinds of insulation can provide pieces to the puzzle that is LNG facility safety and design, cellular glass insulation completes the picture by addressing multiple challenges at one time.
The insulation can play more than one role by reducing fire risks, repelling moisture from insulated systems and reducing the amount of noise generated while providing support for storage tanks without compressing or losing thermal performance.