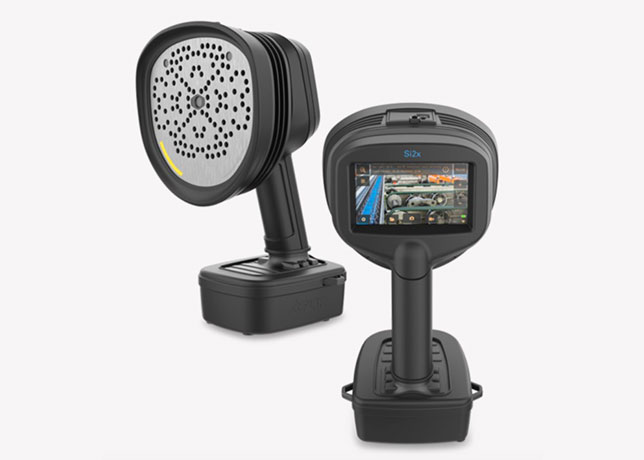
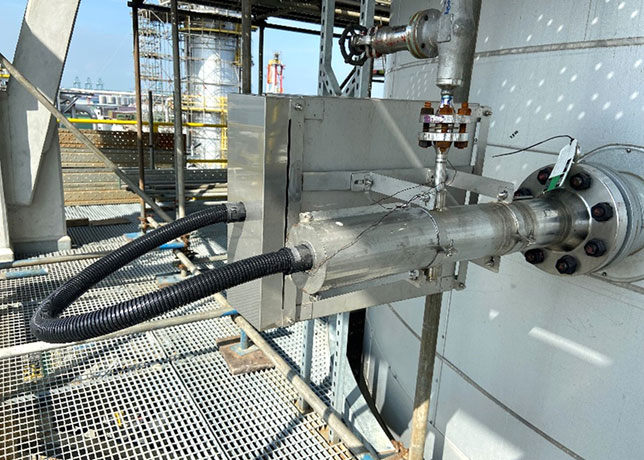
Endress+Hauser’s temperature solutions offer high-precision monitoring capabilities that help refineries optimise process efficiency, extend catalyst life, and manage operational challenges, Michele Pietroni tells OGN
Hydroprocessing is a fundamental operation in refineries, encompassing two major unit types: Hydrotreaters and hydrocrackers. These units process gas oils of varying boiling points to produce a range of refined products with diverse qualities and performances.
Hydrotreaters are the most common processing units in modern refineries, constituting nearly half of global crude distillation capacity.
The number of hydrotreaters worldwide is almost three times that of distillation columns, and the average annual growth rate (AAGR) for these units is projected at 2.6 per cent until 2027. Hydrocrackers, though less common, are expected to grow at a higher AAGR of 6 per cent in the same period.
Countries like China, the US, India, Russia, and Saudi Arabia account for 56 per cent of global hydrocracking capacity as of 2022.
In Asia, nations including China, India, South Korea, Thailand, and Japan contribute to 90 per cent of the region’s hydrocracking capacity, which is anticipated to grow at 8.8 per cent AAGR until 2027.
"These developments are driven by rising fuel demand and increasingly stringent regulations aimed at producing cleaner fuels, including those derived from non-fossil feedstocks," Michele Pietroni, Industry Manager – O&G and Chemical, Endress+Hauser, tells OGN energy magazine.
HYDROTREATING vs HYDROCRACKING: KEY DIFFERENCES
![]() |
ProfileSens TS901 – multipoint cable sensor |
Although both hydrotreating and hydrocracking involve the use of high-pressure hydrogen and catalysts to remove contaminants from oil fractions, there are significant distinctions between the two processes.
Hydrotreating primarily removes sulphur, nitrogen, and oxygen without breaking carbon-to-carbon bonds, while hydrocracking breaks these bonds to produce lighter products with varied energy content and properties.
Another key difference lies in the oil conversion rates, where hydrocracking achieves lower conversion of feedstock into products.
Reactor design and temperature mapping are essential in both processes to optimise efficiency, but the complexity of hydrocracking demands a more intricate configuration due to the exothermic reactions involved in breaking carbon bonds and to control the heat release distribution from the reactor’s design phase to its operation.
HYDROCRACKING: SPECIFICATIONS & CHALLENGES
![]() |
Sensors entering in the reactor and running on supporting beams |
Hydrocrackers operate at higher pressures, use more catalysts, and have more complex reactor sections compared to hydrotreaters.
Controlling the heat distribution across the catalyst beds is critical, and precise temperature measurement is key to maintaining reactor performance.
High-density temperature measurement points within the reactor, such as those provided by iTHERM MultiSens TMS02 (capable of measuring between 2 to 16 points), are essential for accurate monitoring.
Because hydrocrackers have a lower conversion rate than desired, products are often recycled through the same or additional reactors to achieve conversion rates of up to 95 per cent.
When processing heavier feedstocks containing olefins, aromatics, and sulphur, the temperature across the catalyst bed can rise by 70-90 deg C, making multi-bed reactor designs necessary to distribute heat and manage cooling.
In reactors with fixed catalyst bed reactor, achieving conversion rates of 65-70 per cent requires precise thermal mapping, especially considering the thermal stresses that can occur during operations.
The iTHERM ProfileSens TS901, with its multipoint measurement capability, offers a suitable solution for monitoring temperatures in these challenging environments, ensuring both accuracy and minimal interference with fluid streams across the bed with the right density of measurement points.
CATALYST LIFE: INFLUENCING FACTORS & TEMPERATURE MONITORING
![]() |
Sensors routing along internals |
The catalyst plays a vital role in hydroprocessing, driving reactions with high efficiency and quality.
The lifecycle of catalysts, which can last anywhere from 12 to 60 months, is heavily influenced by thermal and mechanical stress.
Maintaining an optimal temperature distribution within the reactor can help extend catalyst life, which has a direct impact on the economics of hydrocrackers.
At the start of a reactor’s cycle, temperatures across the catalyst bed are typically between 330 deg C and 350 deg C, with uniform radial temperature distribution and predictable axial gradients.
However, as the catalyst deactivates over time, temperature variations increase, forcing refiners to adjust feeding rates and inlet temperatures to maintain conversion rates.
Monitoring these changes with high-precision thermocouples like those from the iTHERM MultiSens family helps ensure that thermal stress is minimised through perfect instrument integration (thanks to the high level of customisation and engineering), prolonging catalyst life and optimising reactor performance.
MANAGING CATALYST DEACTIVATION
Catalyst deactivation poses several operational challenges, including the need to increase inlet temperatures and feeding rates to maintain product quality.
Accurate temperature monitoring is essential for managing deactivation rates and ensuring that reactor components are not exposed to temperatures exceeding the maximum allowable structural temperatures, which could damage the reactor’s internals.
Temperature sensors, such as iTHERM MultiSens TMS02, play a key role in monitoring critical reactor zones to prevent damage and plan timely maintenance shutdowns.
Additionally, excessive gas production from side reactions during deactivation can strain downstream gas-processing utilities, requiring operators to reduce feed rates or conversion levels.
Accurate temperature monitoring helps balance the trade-off between gas production, cooling hydrogen consumption and the quality of middle distillates. In extreme cases, shutting down the reactor to replace the catalyst may be more economical than continuing to operate at reduced efficiency.
The diagnostic chamber feature of the iTHERM TMS02 allows operators to monitor hydrogen injection effectiveness, providing real-time data on cooling efficiency in the catalyst layers.
It also helps detect early signs of process issues, such as micro-cracks in reactor components caused by sensor vibrations or corrosion from catalyst overheating.
PRESSURE MANAGEMENT & STRUCTURAL INTEGRITY
As the catalyst bed becomes more fouled over time, pressure drops across the reactor increase, especially in the first catalyst bed, which is highly sensitive to fouling.
If pressure drops become too large, components like quench deck support beams can suffer thermal deformation, potentially affecting reactor performance and integrity of internals.
High-precision temperature sensors installed in critical reactor zones, such as those in the iTHERM MultiSens family, can help monitor and manage these issues, ensuring structural integrity and preventing costly shutdowns.
FEEDSTOCK QUALITY & POISONING DETECTION
Sudden changes in feedstock quality, such as the introduction of residue that poisons the catalyst, can cause rapid fouling and sintering.
Early detection of these issues is possible through high-density temperature measurement points, enabling operators to take swift corrective action.
By identifying poisoned layers early, operators can remove contaminated catalyst layers and extend the life of the entire catalyst bed, minimising downtime and costs.
In summary, accurate temperature measurement and monitoring are crucial for the effective operation of hydrocrackers and hydrotreaters.
Endress+Hauser’s iTHERM MultiSens and ProfileSens temperature solutions offer robust, high-precision monitoring capabilities that help refineries optimise process efficiency, extend catalyst life, and manage operational challenges such as catalyst deactivation and feedstock variations.