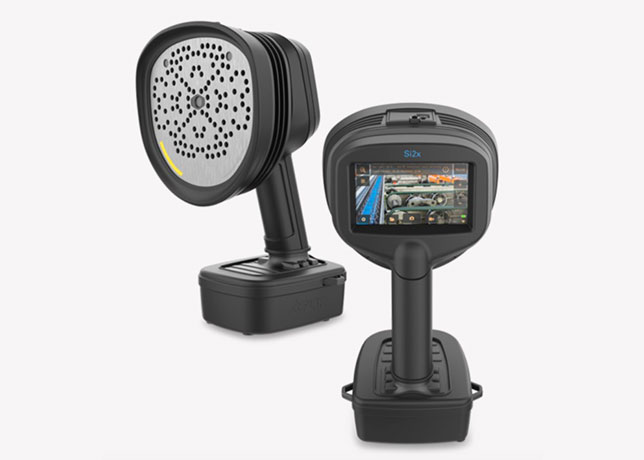
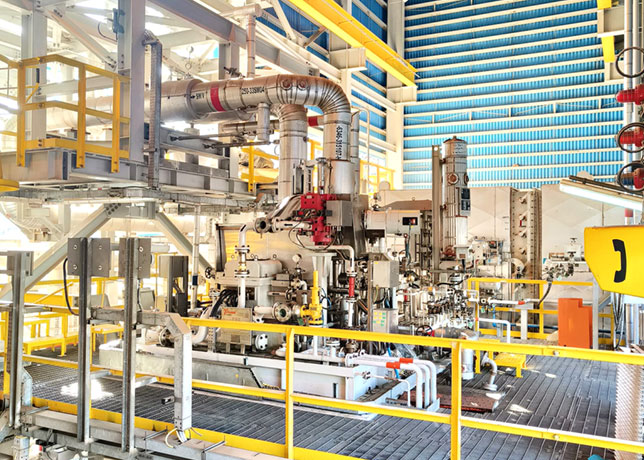
The oil and gas industry's challenges are accelerating the adoption of energy-efficient technologies, with steam turbines playing a key role in optimising steam balance and utilisation for enhanced sustainability and reduced emissions
Steam turbines play a crucial role in the oil and gas industry, particularly within petroleum refineries.
These turbines can be classified as backpressure or condensing types, with configurations that include extraction capabilities, depending on the specific design of the plant cycle. In refineries, steam turbines are versatile, serving as mechanical drivers for pumps and compressors, as well as generating power when coupled with alternators.
Additionally, combined cycle systems that incorporate both steam and gas turbines can be tailored for optimal performance, whether for electrical load matching or thermal load matching.
This adaptability allows refineries to enhance their efficiency and meet varying operational demands.
In this context, Triveni Turbines Limited (TTL) is making significant strides in the API segment of the industry.
Recognising the growing need for energy and sustainable technologies amidst a volatile geopolitical landscape, TTL is partnering with leading EPC firms and original equipment manufacturers (OEMs) to deliver high-efficiency steam turbine solutions.
TTL continues to invest in research and development, with recent successes including high-speed, high-power-density models that enhance the compactness of turbine-generator packages.
The company has installed numerous high-speed turbines, operating at speeds of up to 12,000 rpm, which maintain high reliability and efficiency in various installations.
Additional R&D initiatives focus on developing high-efficiency low-pressure (LP) modules tailored to new requirements, improving high-pressure (HP) blading, and introducing innovative sealing technologies, all aimed at advancing the application of steam turbines.
![]() |
A 3.6 MW STG ready for dispatch to a client in India |
TTL boasts a significant installed base of API steam turbines under 100 MW across petroleum refineries globally, with numerous installations already commissioned and a robust pipeline of projects planned for commissioning in the coming years.
REFERENCE CASES FOR PETROLEUM REFINING INDUSTRY
1. TTL supplied a project in Kuwait with four each of 1.5 MW and 2.7 MW back pressure steam turbine generators (STG) for drive applications.
• Project description: The contract, for a national oil company and a leading petroleum refining company in Kuwait, included design, supply, and commission an API 612 steam turbine for use in fan drive applications and as per shell design engineering practices (DEP) plus AMEC FW project variations. Each steam turbines power four combustion air blowers and flue gas fans respectively for the world’s largest reformer package.
• Challenge: These special purpose steam turbines were designed, manufactured and tested as per the project specifications, which includes design for outdoor installation, ensuring a minimum design metal temperature suitable for -30 deg C, and meeting the classification for electrical hazard area Zone 1, IIC, T3.
• Solution: The supplied steam turbines have a design life of 30 years and 6 years of continuous operation. The supply scope also encompassed gear units, lube oil systems, unit control panels, and gland steam condensers. The project was commissioned successfully to meet the specifications.
2. A project in India is driven by TTL’s 3.6-MW back pressure STG for drive applications.
• Project description: In a contract from a national oil company and a major petroleum refining company in India, TTL designed, supplied, and commissioned an API 612 steam turbine for use in compressor drive applications.
• Challenge: The steam turbines were designed to meet the project specifications, featuring instrumentation appropriate for electrical hazard areas and high-humidity environments. The steam turbines, clutch, coupling and driven equipment were mounted on a common base frame that complies with applicable standards.
• Solution: The steam turbines were successfully mounted on a common base frame in compliance with API RP 686 standards. They were supplied to the customer with advanced governing and control systems (including the Woodward FT 5009 TMR Governor and MOOG Hydraulic actuator) to drive an induction generator/motor and compressor. Additionally, they feature instrumentation suitable for Zone 1, IIC, T3, and high-humidity environments.
3. TTL supplied a 3.85-MW extraction condensing STG for drive applications in Australia.
• Project description: TTL was awarded a contract by a major chemical and fertiliser company in Australia to design, supply, and commission an API 612 steam turbine for use in boiler feed water (BFW) pump drive applications.
• Challenge: The steam turbines were designed to meet project specifications, accommodating necessary variations in extraction flow. Additionally, they will integrate advanced materials designed to withstand seawater as a cooling medium, ensuring adherence to all applicable standards.
• Solution: The steam turbines, mounted on a steel structure, were engineered to withstand nozzle loads up to 5.5 times those specified by NEMA SM23. Seawater, with a fouling factor of 0.000172 m²K/W, is used as the cooling medium, necessitating the use of titanium for both the condenser tubes and tube sheets. The steam turbines feature an adjustable extraction flow ranging from 0 TPH to 9 TPH to meet the plant's process requirements, all while ensuring full compliance with Australian standards.
4. TTL supplied a 33-MW straight back pressure STG for power generation applications in the UAE.
• Project description: TTL secured a major contract from a national oil company and a leading petroleum refining company in the UAE to design, supply, and commission an API 612 steam turbine for a power generation application.
• Challenge: The steam turbines were designed to meet the project specifications, which involve designing the turbine to operate at high ambient temperatures of 54 deg C and with an inlet pressure of 38.5 bar, inlet temperature of 398 deg C, exhaust pressure of 6.5 bar. The turbines were also equipped with instrumentation suitable for high hazardous area classification. Amidst strong competition from European turbine manufacturers, TTL provided the necessary support to the customer in meeting the desired technical requirements and emerged as the preferred vendor for this critical project (non-stop equipment package without standby).
• Solution: TTL partnered with a reputable Spanish EPC company from the front-end engineering design (FEED) phase through to the EPC bidding stage. The project's design parameters would be met by engineering the turbines to operate under extreme ambient conditions of 54 deg C, utilising a closed air circuit air-cooled (CACA) generator, incorporating lube oil cooling, ensuring compliance with high hazardous area classification, and implementing triple modular redundant (TMR) governor technology.
CONCLUSION
The global oil and gas industry's current challenges have catalysed a crucial shift towards the adoption of energy-efficient technologies, bringing substantial benefits to petroleum refineries, chemical plants, and petrochemical facilities by significantly lowering their carbon footprint and operational costs.
Achieving global energy efficiency and net-zero emissions will require a concerted effort from policymakers, energy-intensive industries, energy agencies, EPC contractors, process licensors, and OEMs, working in unison to enhance the global energy infrastructure and guide nations toward a more sustainable future.
In this context, steam turbines play a crucial role in achieving these goals, as optimising steam balance and maximising steam utilisation have become critical design considerations.
By Abdulaziz Khattak