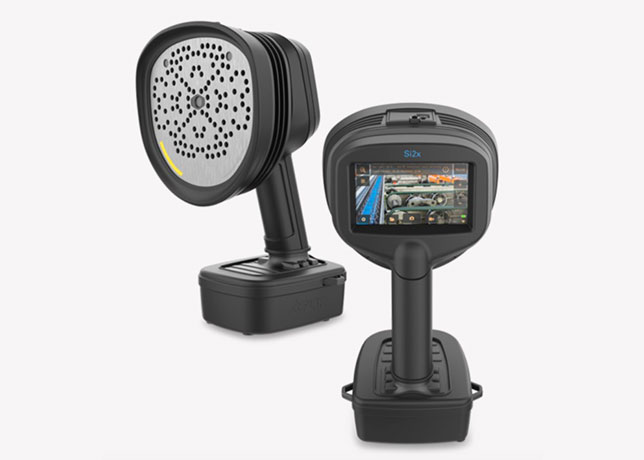
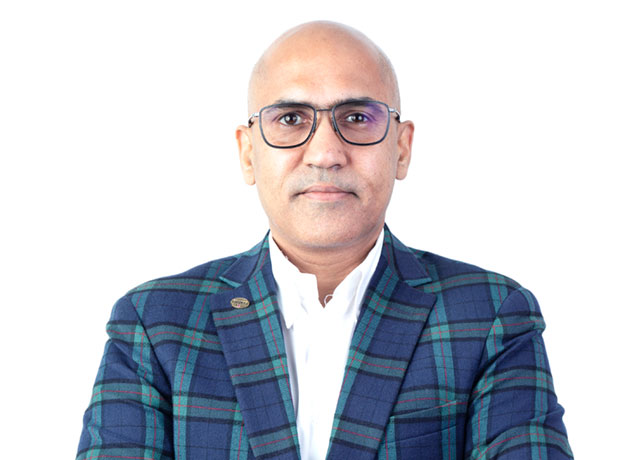
Innovative recycling solutions are essential for effectively addressing plastic waste challenges and enhancing the quality of pyrolysis oil for sustainable ethylene production, Deepak Sharma tells OGN
In an era where sustainability is at the forefront of global discourse, addressing plastic waste has become crucial for the health of our planet.
Plastics provide benefits to nearly every aspect of life, but the resulting high demand has led to increased production, generating a significant amount of plastic waste.
As the global economy and population expand, plastics demand is expected to grow from 350 million tonnes in 2020 to 950 million tonnes in 2050.
With only approximately 10-12 per cent of that plastic being recycled, millions of tonnes of plastic are incinerated, disposed of in landfills or end up collecting in oceans and other waterways leading far-reaching consequences.
Plastic waste has become an alarming global problem, with its impact on the environment and human health steadily increasing.
Banning single-use plastics might not eliminate plastic waste challenges completely, but strengthening waste management practices can return plastic waste to a circular economy.
'As public opinion has moved toward a greater emphasis on sustainability concerns, the response to plastics has turned towards increasing the level of circularity,' Deepak Sharma, Senior Marketing Manager, Nalco Water, an Ecolab company, tells OGN energy magazine
ACHIEVING CIRCULARITY
Mechanical recycling traditionally involves grinding, melting, extruding, and cutting plastics into pellets without altering their chemical structure. This method primarily works with three grades of plastic: PET, HDPE, and polypropylene.
![]() |
Table 1 |
However, repeated recycling degrades the polymer quality, and sorting incompatible plastics is labour-intensive.
To broaden the range of recyclable materials, chemical recycling, which alters the chemical structure of plastics, is being explored as a promising alternative.
There are two main methods for chemical recycling: Depolymerisation (also known as re-monomerisation or monomer recycling), where the polymer is broken down into its monomer building blocks; plastics-to-feedstock, which uses heat in an oxygen-free or low-oxygen environment to break down plastics into material commonly called pyrolysis.
• Pyrolysis oils (pyoils) as an ethylene feedstock: As chemical manufacturers have started looking towards pyoils and similar feedstocks produced from recycled plastics, there has been considerable interest in the impact these feeds would have on production and processing within the ethylene plant
• Characterising pyoils: Because these pyoils are still new to the ethylene industry and not much is known about their properties, the Nalco Water Research, Development, and Engineering (RD&E) group began analysing pyoils from various chemical recyclers and developed a battery of tests, using both ASTM methods and in-house proprietary tests.
Over 200 pyoil samples have been tested in our lab with established ASTM pyoil test methods (Table 1).
PYOIL FEEDSTOCK CHALLENGES
• Product stability: Pyoils can be highly olefinic in nature, breaking down to form films or gums. This is often, but not always, due to oxidation.
![]() |
Table 2 |
Film formation can cause plugging of equipment, fouling heat exchangers and build-up of solids in storage equipment. Fouling in the convection section of a pyrolysis furnace is a particular concern.
Using a proprietary oxidative stability test, researchers found that treating pyoil with an antioxidant can increase its stability and reduce/eliminate film formation.
Table 2 shows the dose-response of pyoil stability using antioxidant, and Figure 1 shows an example of film formation of untreated versus treated pyoil.
• Flow properties: Many of the pyoil samples exhibit undesirable cold flow properties. This can lead to difficult pumpability and require expensive capital for heated storage and transportation facilities.
The use of a pour point depressant (PPD) can reduce cost on heated facilities. Table 3 shows the dose-response of pyoil using Nalco pour point chemistry.
• Heavy components and variability: Pyrolysis processes producing pyoil generate heavy components ranging from a coke, tar like heavy oil to wax which can cause issues during further processing. In some conditions, higher-value, lighter pyoil may be downgraded as 'cutter stock' for heavy material.
![]() |
Plastic waste has become an alarming global problem |
In those cases, lab testing has shown that the use of a pour point chemistry can allow manufacturers to use less cutter stock, thus producing more higher value pyoil. Analysis of pyoil samples have shown that they tend to vary widely not only from producer to producer, but even batch to batch.
As chemical recyclers expand in scale from pilot to commercial operation, an increasing volume of waste feedstock is required.
Sorting out known contaminant source s is often done manually, making its both labour-intensive, subject to human error. Variable contaminant levels can cause process reliability issues.
Presence of reactive components and their varying concentration can impact fouling risk, along with varying amounts of saturates that can impact ethylene yield across the furnaces.
In benchmarking testing, researchers found that pyoils derived from catalytic processes had significantly higher concentrations of aromatics than thermal processes. The variability tends to impact in three principal areas: Film formation (oxidative and non-oxidative); corrosivity; and feedstock contaminants.
![]() |
Figure 1 ... Film formation in untreated (left) versus treated (right) samples |
A chemical recycler sent two different sets of pyoil samples: one from March 2021, and the other from November 2022. Benchmarking (Figure 2) shows that film formation and fouling propensity were observed for samples contain a high concentration of N, O-containing compounds such as caprolactam, imidazolines, etc.
Additionally, it was observed that when the film was filtered out, it re-formed in the samples. Testing showed that dispersants were effective at keeping the film solubilised in the pyoil and was even able to disperse deposits already formed.
• Contaminants: Feedstock contaminants are a significant concern to ethylene manufacturers, dealing with contaminants in pyrolysate feedstocks and multiple technologies have been introduced or repurposed to deal with contaminants.
Known potential contaminants in pyoil and their potential impact in the ethylene plant include:
1. Oxygenates can produce organic acids in the ethylene furnace increasing corrosive potential, or peroxides and carbonyls that increase fouling severity and downgrade crude C4 value. The most common source of oxygenates is PET.
2. Chlorides damage cracking furnaces and form HCl. The most common source of chlorides is PVC.
![]() |
Figure 2 |
3. Nitrogen can form ammonia in the furnace, and any N-O bonds present can form NOx being sourced from nylons, caprolactam, imidazolines, and other compounds.
4. Phosphorous & Si can be a catalyst poison.
To reduce the potential negative impacts of contaminants in the ethylene production process, manufacturers are diluting pyrolysis oil with other liquid feed. Several approaches are being proposed in the marketplace, including adsorbents, hydro processing and use of extraction solvents.
Nalco went in with proprietary extraction techniques utilising various chemistries to successfully remove 70 per cent of chlorides.
CONCLUSION
Advanced recycling is an emerging technology that can complement traditional recycling to help promote plastics circularity. There are, however, significant challenges to manufacturers seeking to use pyrolysis oil as feedstocks in their processes.
Solvent stability, flow properties, heavy material, variability, and contaminants are among the challenges faced with the pyoils themselves, as well as additional challenges like to be discovered as the impacts of cracking this material on ethylene unit operations are documented.
Through extensive research of a variety of pyoils, Nalco Water research has shown that various chemical additives can address these challenges, providing pyoil that is more stable, less prone to fouling, and lower in contaminants.