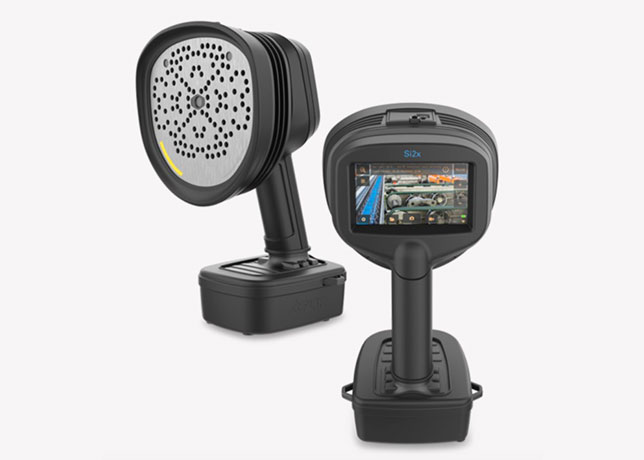
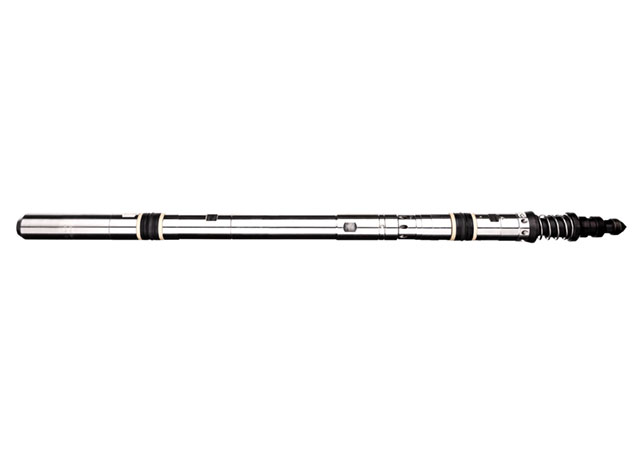
The Adaptive Gas Lift System (AGLS), developed by Interwell and Emerson, adapts to changing production conditions, maximising production while minimising lifting costs, with innovative, retrievable technology
In the ever-evolving landscape of oil production, efficiency is paramount. The Adaptive Gas Lift System (AGLS) is here to transform the way gas lift operations are approached, leveraging cutting-edge technology to enhance production while addressing the challenges of traditional systems.
Introducing the world’s first electric gas lift system qualified to international standards, Interwell and Emerson through the AGLS combines proven methodologies with advanced digital solutions.
This innovative system is designed to adapt to fluctuating reservoir conditions, ensuring optimal performance and cost-effectiveness throughout the life of a well.
The AGLS is a retrievable digital gas lift system that primarily utilises field-proven technology.
AGLS is the world’s first electric gas lift system qualified to internationally recognised standards.
It is based on industry-leading Interwell and Emerson gas-lift technology and Emerson’s Roxar Integrated Downhole Network and sensor technology.
THE CHALLENGE
![]() |
The AGLS utilises field-proven technology |
Conventional gas lift systems are designed to optimise the initial production phase when tubing pressure is high.
However, as production conditions change over time, adjustments to the orifice size and injection depth are required to maintain efficiency.
Closing each injection pressure operated (IPO) valve requires a drop in casing pressure, which can limit the injection depth and potentially reduce additional production.
Manipulating casing pressure and dealing with IPO temperature uncertainties often leads to multi-pointing, resulting in ineffective gas lift and loss of production.
Well interventions are expensive and can be particularly challenging if the well has flow assurance issues.
These issues can complicate valve retrieval, leading to additional downtime and increased operating expenses (opex).
SOLUTION
The AGLS offers the ability to adjust port size and change the injection depth to deliver optimal injection rates as well conditions change.
This adaptability addresses future uncertainties in modeled reservoir conditions. Deeper injection is possible as the valves can be closed without reduction of casing pressure.
Continuous online optimisation throughout the life of the field maximises production and reduces project payback time.
Furthermore, AGLS reduces the instability associated with conventional gas-lift systems by optimising the injection rate and port size.
AGLS is compatible with e-field and i-field technologies, offering the potential for autonomous production optimisation.
SYSTEM SPECIFICATIONS
• Designed and qualified to API 19G1 (V1), 19G2 (V0) and AWES 3362-36.
• Set and retrieved using conventional wireline methods.
• Run on a single TEC line, up to 32 nodes on an Emerson Electric network.
• The Side Pocket Mandrels accept both electric and conventional gas lift valves (1.5 inches).
• 4.5-inch and 5.5-inch mandrels in 9-5/8-inch casing (other sizes can be made available upon request).
• Temperature range: 4-150 deg C.
• Valve working pressure: 10,000 psi, 15,000 psi absolute.
• Adjustable variable choke allows fractional port size variation from 10/64 inches to 32/64 inches.