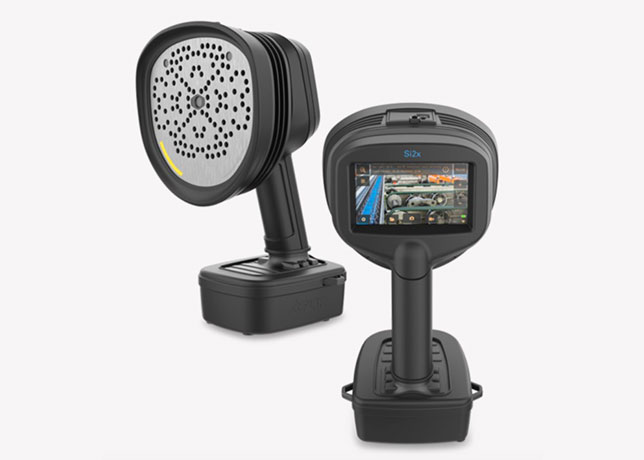
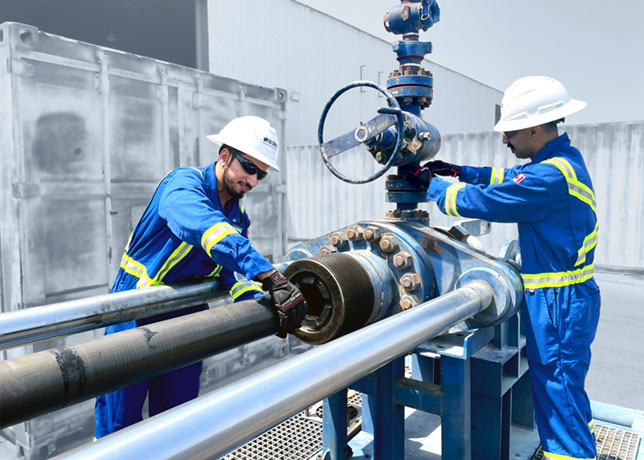
A suite of technologies tailored for the region brings forward automated solutions for the wellsite and clean tunnel perforating systems that can significantly reduce opex, Patrick McKeever and John Creighton tell OGN
Oil and gas remain a critical part of the global energy mix, with the Middle East region home to some of the world’s top energy producers.
According to the International Energy Agency (IEA), energy investment in the Middle East is expected to reach approximately $175 billion in 2024, with traditional energy supplies dominating the region’s exploration and production (E&P) activities.
As Middle East operators pursue more complex, deeper reservoirs to access untapped energy resources in exploited fields, downhole perforating and completions technologies will be vital in securing the region’s energy future and meeting global demand.
A suite of new and existing technologies tailored for the Saudi land market and Middle East operations brings forward automated solutions for the wellsite and clean tunnel perforating systems that can significantly reduce opex in an era of capital discipline.
Three innovative technologies in particular are helping oilfield companies overcome complex well challenges to optimise completions.
REDUCING RIG TIME & CLEANUP COSTS
Perforating technologies have a major impact on efficient production operations. Technologies such as GEODynamics’ Connex® can help oilfield companies in the Middle East tackle tighter, more complex conventional sandstone formations and make wells more productive for greater return on investment.
It’s able to remove the perforation skin to restore a perforation tunnel to near virgin porosity and permeability.
This technological approach works by clearing out the compaction zone in a perforating zone.
A patented charge liner material is deposited along the tunnel, cleaning exothermically when introduced to heat and pressure.
This cleaning action creates significant pressure within and around the tunnel, breaking up and expelling the crushed zone compacted debris back into the well bore.
In sufficiently competent rock, fractures are also formed at the tunnel tip. Improved perforation cleanup delivers clear, open tunnels independent of rock type, promoting optimal flow paths between the reservoir and wellbore.
![]() |
ACTIVELatch's remote capabilities promote greater site safety and reduced downtime |
Using a proprietary flow laboratory, GEODynamics characterises shaped charges to meet an operator’s specific requirements based on formation properties.
This engineered solution provides a solid understanding of the well performance expectations to help derisk projects.
Connex technology is currently used onshore in Oman and Saudi Arabia where new drilling techniques are targeting deeper reservoirs up to 25,000 ft, compared to the 2,000–3,000-ft depth of previously pursued reservoirs.
However, the more complex the well operation, the more time consuming it is to clean up perforation tunnels.
Eliminating the need to use the well stimulation tools that conventional perforating tools require effectively reduces rig time – saving as much as up to 48 hours in the EMEA region – and cleanup costs.
STREAMLINING WIRELINE OPERATIONS
Saudi oil and gas operations are especially challenging, as companies must currently rig down and remove isolation equipment to accommodate wireline operations, increasing non-productive time (NPT) and costs in between stages.
Wellhead isolation enables operators to run wireline tools, perforating guns, plugs and other downhole operations without removing isolation equipment when switching between frac and wireline operations.
With a large bore tool such as Oil States’ StageFrac™, operators can save three hours per stage of rig up/rig down time of their equipment, which equates to a full 24 hours of time-savings over eight stages. Fewer equipment moves also decreases safety risks for wellsite personnel.
In addition to substantial time savings, operators can enjoy greater adaptability to different styles of completions.
This provides increased operational flexibility across various types of wells.
The technology’s simplicity also allows hydraulic setting tools to remain in place throughout wireline operations as well as frac operations, streamlining the entire process.
This can produce significant operational efficiencies, allowing operators to complete more stages while minimising NPT and increasing safety on site.
The Oil States Active Seat Gate Valve is often paired with StageFrac for Saudi operations, which provides a patented sealing mechanism that is technologically advanced compared to traditional gate valves due to its ability to exclude debris from the valve cavity while reducing the amount of grease required or lost during valve operations.
This reduces valve grease contamination and can cut costly valve repairs significantly while extending valve life.
Over a six-month period of standard operation, it’s estimated that less than one pound of grease is lost per valve which not only eliminates typical greasing requirements during operations but also reduces maintenance downtime and prevents unwanted grease downhole that could inhibit oil production.
REMOTE WELLSITE MONITORING & CONTROL
Automation marks the next major evolution at the wellsite, freeing up personnel to work on higher-value tasks while also improving safety factors.
![]() |
Rig time can be reduced by up to 48 hours with Connex |
Wireless capabilities also eliminate the need for cumbersome cables or hydraulics, which helps reduce points of failure to streamline operations and reduce NPT.
Most important, automating wellsite operations can significantly reduce exposure to hazards that result in injuries or an industrial accident.
Remote operation proves even more valuable in difficult or remote environments where wellsite access may be limited.
ACTIVEHub™ is an automated digital platform that helps operators improve stage completion efficiency through remote monitoring, removing personnel from the red zone.
This advanced communication and control system employs ACTIVELatch™ technology, the industry’s first battery-operated wireline latch enabling oilfield companies to remotely make and break wireline connections.
The ability to capture real-time information and control the latching process up to 75 ft away is an innovative way to automate wellsites in remote Middle East operations.
Additionally, downtime can be reduced by saving 20 to 25 minutes per swap from frac to wireline as compared to conventional methods of making wireline connections.
For complex, remote land operations in the Middle East, automation delivers significant benefits to enable safety and remote operation, efficient and continuous monitoring, and intelligent data collection and predictive maintenance.
LOCAL CAPABILITY, GLOBAL ENERGY SECURITY
Oil and gas production remains a vital contributor to global energy security, even as the energy mix diversifies. The dynamics of today’s production efforts require new solutions to help ensure the full oil and gas potential of the Middle East is realised.
Minimising NPT and rig time while increasing safety and operational efficiency are paramount for the region as the industry evolves. Cost-effectively tapping into the region’s unconventional reservoirs in addition to conventional oil and gas resources ensures continuity of production goals.
* Patrick McKeever is the Business Development Manager for Oil States Energy Services. Over his 20-year career with the company, he’s focused on optimising wellsite operations.
John Creighton is the Director of International Business Development and New Technologies for GEODynamics. Creighton’s oil and gas industry experience spans more than 20 years, concentrated on Middle East production.