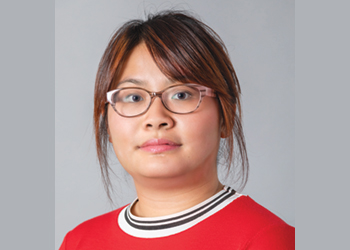

Saras expects to achieve savings from this initiative, which is part of an important digitisation project, says Alessandro Zucca, Digital Platform Manager, Operations and Assets, Saras
Saras, the owner of the most complex refinery in the Mediterranean, with 300,000 barrels per day capacity, was evaluating ways to drive greater drive reliability in its capital- and asset-intensive refinery operations as part of its digitalisation programme.
It selected AspenTech's Aspen Mtell based on a competitive pilot project selection process which initially focused on critical refinery equipment, such as large compressors and pumps.
Aspen Mtell mines historical and real-time operational and maintenance data to discover the precise failure signatures that precede asset degradation and breakdowns, predict future failures and prescribe detailed actions to mitigate or solve problems.
"The initial project, conducted in just a couple of weeks, included building Aspen Mtell agents to identify the failures for a subset of equipment. The data for these agents included condition data and process data," says an AspenTech spokesman.
The initial project focused on four pieces of equipment:
• The feed pump that pumps liquid charge from other plants towards the exchange train.
• The wash oil pump, which recycles wash oil coming from the separator to toward the mixer.
• The makeup H2 compressor, which streams makeup H2 from the hydrogen supply toward the main exchange train.
• The recycle compressor, which recycles H2 coming from the exchange train.
The desired outcomes of the pilot project included:
• An accurate solution that detects precise patterns of normal behaviour, failures and anomalies.
• A solution that indicates early warning, with significant lead time from point of detection to actual failure.
• The ability to capture a failure signature and use it to detect failures in unseen data on the same assets and/ or similar assets.
The data used for the Aspen Mtell agents consisted of 52 million sensor values, including condition data and process data. The team reviewed 163 quality issues (such as bad values and missing values) and cross-referenced the work order history of the four assets, including 340 prior work orders. The maintenance history spanned 17 problem classification codes.
The project achieved all objectives, and the Aspen Mtell agents were able to predict failures with significant lead time: high valve temperature, 36 days; oil seal replacement, 45 days; pump seal replacement, 33 days; and gas seal replacement, 24 days. For a reciprocating compressor, the agent showed high accuracy (91 per cent) with a lead time of 30 days.
The agents also accurately identified the specific failure mode without false positives. These capabilities are expected to reduce unplanned shutdowns by up to 10 days, increase revenue by 1 to 3 per cent, reduce refinery maintenance costs and cut operating expenses by 1 to 5 per cent.
Aspen Mtell executed the pilot project within weeks, impressing Saras with its speed of deployment, accurate early detection of asset failures, avoidance of false alarms and ability to scale the solution system-wide.
Saras now plans to use its sister engineering company, industrial automation specialist Sartec, to roll out Aspen Mtell refinery-wide.
"Improving reliability positively impacts a wide range of issues, from reducing current maintenance costs to planning for abnormal process conditions, avoiding emergency or unplanned shutdowns and successfully managing unpredictable feed and demands. Saras expects to achieve savings from this initiative, which is part of an important digitisation project," says Alessandro Zucca, Digital Platform Manager, Operations and Assets, Saras.