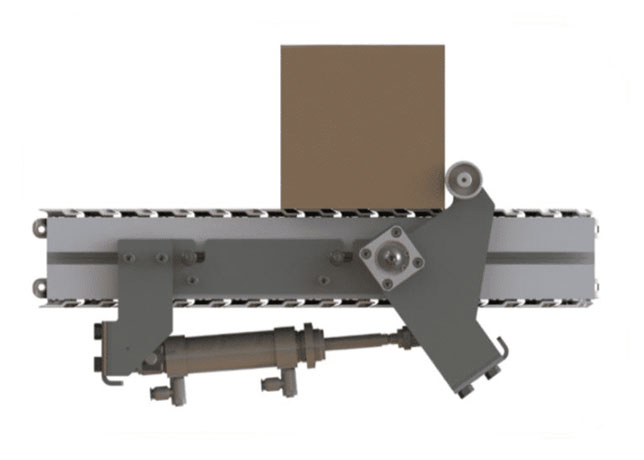
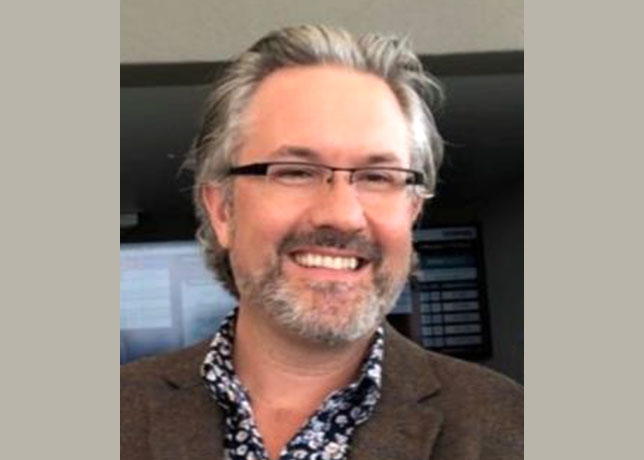
As industrial producers experience the use of high-fidelity process models in water, a new world of optimisation opportunities open up – from daily actions through to production planning and even evaluation of capital projects, Neil Davidson from Ecolab tells OGN
Nalco Water, an Ecolab company, has been serving industrial producers for nearly a century. At the heart of that service is deep domain expertise in how water impacts industrial production plant.
"From our beginnings, we have pioneered innovative technologies in water chemistry and automation to help industry achieve greater environmental compliance, reliability, and efficiency," Neil Davidson, Business Development Lead, Climate Intelligence & Partner Solutions, Ecolab, tells OGN energy magazine.
In the past 30 years Nalco Water has deployed its industry-leading 3DTrasar technology – 40,000 installed water monitoring systems producing 90 billion data points annually.
More recently we have brought digital solutions to industry to quantify individual plant equipment performance that may have previously been overlooked, under-estimated or not fully understood.
With such insights, together with our industrial producer customers we are empowered to take informed, quantified actions to address performance gaps in reliability and efficiency at the individual plant equipment level based on our perspective through water.
![]() |
Figure 1 |
However, to take the performance of industrial water to the next level for producers to achieve their ambitious sustainability goals, a novel approach is required.
An approach that takes a holistic view of water and production so that decisions on sustainability outcomes are informed based on production needs. Productivity must improve along with sustainability.
Water’s role is complicated and its relationship to production processes is often not understood sufficiently to allow optimisation.
What we have seen repeatedly is that the interrelationship between water and production is invariably multifaceted and very dynamic with numerous variables capable of working in conjunction or opposition with each other.
The net outcome of these usually needs to be understood in the context of highly integrated operations where the risk of overall sub-optimal performance is high, especially as deficiencies in one part of the circuit can significantly impact the operation downstream, often with multiplier effects.
![]() |
Figure 2 |
Given this complexity, only a truly holistic view of production can highlight what is dictating economic and environmental performance at any given time.
Ultimately, this necessitates having a production-centric view of water and a water-centric view of production.
Once such a framework is in place, the value it can provide to restore or even exceed design/best practice conditions can be remarkable.
This is especially the case if it is targeted at delivering sustainable production with the objective of producing ‘more for less' energy/emissions, water, and waste.
Here we need to highlight that industrial operations cannot adequately meet their sustainability goals without understanding the essential role of water, particularly as an energy transfer medium.
In refinery operations for example, 35 per cent to over 70 per cent of the total energy is transferred in this way and yet historically this perspective has not been used to inform holistic and integrated optimisation.
We see this energy nexus repeatedly in heavy industry, and the emerging low-carbon energy technologies are no less water and energy intensive.
As we explored the light industry sectors, what we found was that not only did water continue to serve as the predominant energy carrier, but product quality became of increasing importance to productivity.
This is particularly relevant in those products that contain water by formulation such a beer, but also in industries where cooling duty and quality has a significant impact on productivity – such as in microprocessor chip manufacturing.
We see sustainability goals (Figure 1) applied equally numerous and ambitious across the industrial sector, with water at the heart of many decisions.
Having established the "vital roles of water" across the Industrial sector, we focused on a developing a "universal truth" of the relationship between water and its impact on production to achieve sustainable productivity.
This understanding would lead to the development of high-fidelity process models as it would allow us to apply our domain knowledge to the model concept. The universal truth can be illustrated with the tetrahedron in Figure 2.
These interrelationships apply regardless of the nature of the production – at the same time of conserving water and energy and minimising risks (water related scaling, corrosion, fouling, microbial, deposition, product quality, contamination…), the producer must at all times ensure these resources are optimised for maximum productivity – more for less – and optimised dynamically for the reasons mentioned above.
Industrial producer’s profitability is predicated on their productivity, and to remain competitive must be able to produce their products at all levels of demand, in the most optimal, agile, and conservative way.
In many cases, effective use of water is the largest differentiator for competitiveness.
Having established the modelling concepts, we engaged our digital twin partner, Siemens, to build the model, incorporating our domain expertise, and applied this model to already well optimised, world scale refineries and petrochemical plants.
Due to our long history of serving these energy-intensive industries, we were able to secure two pilot sites to achieve proof of concept.
Following the period of building and validating the models in cooling water and steam, the results were surprising – not only could we find opportunities for energy efficiency and reliability improvements through water, but we also found considerable water optimisation savings with commensurately high energy savings.
Most importantly, and critical to producers need of more for less, we found productivity improvements (more product) that could be achieved at no additional energy requirements (that is, reduced energy intensity).
We were also surprised to see how cooling water performance changes over a brief period, for example just a few hours during a morning, and how such changes are productivity impactful.
Our early results confirmed that the vital role of water in energy transfers can be optimised to help industrial producers achieve water and energy savings that will directly impact their sustainability goals, such as 2030 emissions reduction targets.
For a typical world scale refinery or petrochemical plant, setting aside feedstock costs, the total cost of operation is predominantly comprised from people and power.
The energy bill (fuel, electricity) to run a refinery and petrochemical plant can exceed $100 million annually. Of this, 35-75 per cent of this energy cost passes through water at some point.
Small inefficiencies can create multimillion dollar consequences.
During the development of our digital twin, we have found energy savings of over $5 million annually, water savings of over 1million tonnes per year, carbon intensity improvements of over 5 per cent and productivity improvements from $5-10 million annually.
As our industrial producers experience the use of high-fidelity process models in water, a new world of optimisation opportunities open up – from daily actions through to production planning and even evaluation of capital projects.
There is excitement building about the savings that are achievable now, require little or no capex, and can help industrial producers on their journey to greater productivity at a time when they need it most.