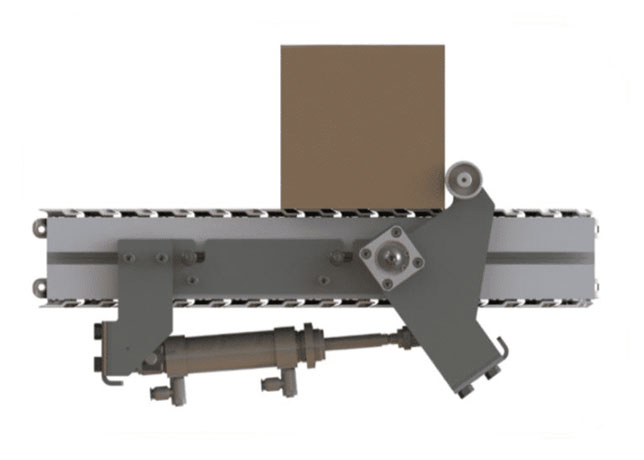
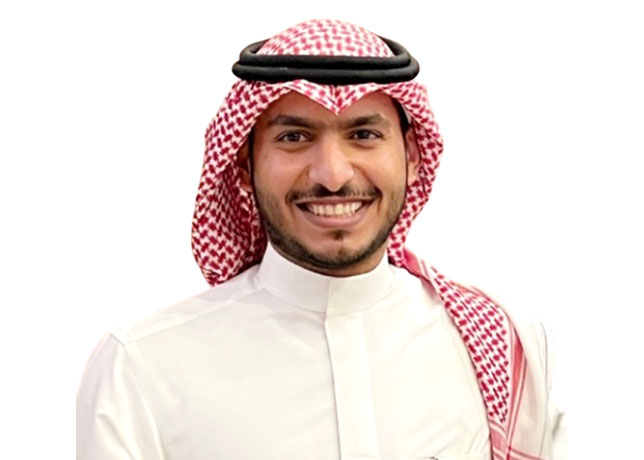
Salt settlement can impact the efficiency of centrifuge equipment. However, a viable solution to prevent this issue is nitrogen puffing, write Turki Alghamdi, Khaled Aljuhany and Pietro Scoppetta from Saudi Aramco in their research
Monoethylene Glycol (MEG) is widely used as a dehydration agent in the natural gas industry. In the MEG regeneration process, centrifuge equipment is commonly used to separate salts from the MEG solution.
However, salts settlement can cause significant issues with the efficiency of the centrifuge equipment.
The MEG regeneration process involves several steps aimed at obtaining lean MEG form the rich MEG stream.
Rich MEG is typically received in the MEG regeneration unit from the plant slug catchers and inlet separators. This liquid feed generally contains some dissolved hydrocarbons, CO2, salts and solids.
Filtration removes solid particles and floating impurities from the MEG solution. Degassing and thermal processes leave a stream with concentrated salts.
The separation of the salts from the MEG solution is usually referred to as reclamation. The slurry stream produced in the reclamation is typically fed to a centrifuge to produce a salt cake.
"Centrifugation is the most efficient method for separating salts and impurities from the MEG solution during the regeneration process and is included to enhance the level of recovery of glycol," a research study by Turki Alghamdi, Planning and Performance Management Analyst, Saudi Aramco, Khaled Aljuhany, Project Engineer, Saudi Aramco, and Pietro Scoppetta shows.
CENTRIFUGATION
During centrifugation, centrifugal force is applied to the slurry that has been obtained by processing of the contaminated MEG solution, causing heavier particles to separate and settle at the bottom of the equipment.
The purified MEG is then recovered along with the regenerated MEG, leaving the separated impurities to be removed later.
However, salts settlement can cause fouling in the centrifuge equipment, reducing its efficiency and leading to unplanned downtime and production losses.
Centrifuges may have different design features. Nevertheless, it is possible to identify a general working principle based on batch operation that comprises the main steps of filling, centrifugation and scraping/discharge.
At the end of a cycle, it is typical of the machine operating procedure to leave a residual heel of salts cake on the basket in order to protect the filtering cloth. This is deliberately done to avoid the scraper to touch (and damage) the filtering cloth.
After several cycles (10 to 15) this residual film affects the filterability efficiency. In other words, the centrate (the liquid that is supposed to be separated) starts to encounter increasing difficulty to pass through the residual heel and cross the basket.
This heel layer then needs to be removed. Inefficient removal of the heel can eventually lead to halt of the operation to allow for operators to intervene and manually clean the basket.
In the most severe scenarios, it can even cause equipment failures with associated downtime.
Periodical removal of the heel is, therefore, important to maintain proper operation of the centrifuge.
A common way to aid the cleaning of the heel is through water washing. This can be automated as part of a Cleaning in Place (CIP) procedure.
However, water cleaning may not be effective enough. Hence, an alternative (or additional) pneumatic cleaning system can be considered that typically uses nitrogen supply available in the plant.
SOLUTION: NITROGEN PUFFING FEATURE
One solution to prevent salts settlement in the centrifuge equipment is to use a nitrogen puffing feature.
Nitrogen puffing is a process in which nitrogen gas is used to prevent salts from settling in the bowl or walls of the centrifuge equipment.
During the process, nitrogen is introduced into the chamber by means of puffing through designed nozzles into the walls of the centrifuge, causing the salts to displace from the walls.
In addition to this system that blows nitrogen from outside of the basket, it may be possible to include also nozzles suitably located on the scraper blade supports in order to blow nitrogen from the basket interior.
The nitrogen blowing process can be automated and integrated in the control steps of the centrifuge.
The details of the solution may slightly differ depending on the centrifuge manufacturer, but the system is not an uncommon feature and the vendors should be able to assist on its most appropriate definition.
The use of nitrogen puffing in centrifuge equipment has several advantages:
• Improved separation efficiency: Nitrogen puffing can improve the separation efficiency of the centrifuge equipment by preventing salts settlement, leading to a higher quality MEG solution.
• Reduced maintenance costs: The use of nitrogen puffing can reduce maintenance costs by minimising fouling in the equipment, reducing the need for cleaning and replacement. The system is generally relatively inexpensive to include and its cost is expected to be easily offset by Opex improvements.
• Increased equipment life: Nitrogen puffing can increase the life of the centrifuge equipment by reducing the fouling and wear on the equipment.
• Increased production capacity: By preventing salts settlement, nitrogen puffing can increase the production capacity of the MEG regeneration process.
CONCLUSION
Salt buildup in centrifuge equipment can cause several problems in the MEG regeneration process, including reduced separation efficiency, equipment failure, and increased maintenance costs.
The use of nitrogen puffing in centrifuge equipment can effectively prevent salt buildup, improve separation efficiency, and reduce maintenance costs.
Nitrogen puffing systems can be retrofitted to existing centrifuge equipment, making it a cost-effective solution for improving the performance of MEG regeneration processes.
It is important for companies in the oil and gas industry to consider implementing nitrogen puffing systems in their MEG regeneration processes to improve efficiency and reduce costs.