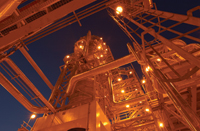
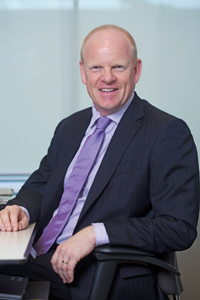
WITH global energy demand expected to double by 2050, Shell sees itself as a major contributor to meeting it, placing top priority on partnerships and innovation to find the way forward.
“By partnerships, I mean mutually beneficial partnerships, which bring out the best of the complementary strengths of partners,” says Gerald Schotman, Shell executive vice president and chief technology officer, innovation, research and development in an interview with OGN.
Shell is committed to research and development (R&D). R&D is expected to drive innovation and come up with solutions for the energy challenges, he says. Here the role of geoscience is critical. It will fill the world with energy.
In this context the need for operational excellence is paramount. Technology and operational excellence are the key to unlocking a sustainable future for global energy, he says.
Among innovative technologies that are helping Shell tap resources in frontier areas, three technologies come to mind – one is seismic imaging onshore, wireless systems which can connect small very accurate sensors with each other and fibre optics and acoustic sensing, says Schotman.
Then there is the offshore flying nodes technology (developed by the UK-based GO Science Ltd, which is focused on mobile sensor grid technologies that offer economies of scale in survey automation. GO Science developed self-propelled “flying” nodes that can position themselves at predetermined locations and is currently testing primary in-flight landing and corrective secondary positioning).
Shell is interested in reducing the cost and improving the robustness of ocean-bottom receiver arrays, and this technology is cheaper and will cut deployment time in half compared to current systems. Referring to underbalanced drilling, he says well engineers pump thick fluid into well shafts to counteract pressure from oil and gas in the surrounding reservoir. But the high pressure created can cause damage to the rock formation or reduce the oil and gas flow. “To overcome this we are applying an innovative solution – underbalanced drilling.”
Schotman says underbalanced drilling, particularly for tight gas, is very advantageous. “Shell is the leading company in the world in underbalanced drilling; it is our standard way of drilling. We have been using it everywhere globally,” he says.
In conventional, or “overbalanced”, drilling fluid is pumped into the well shaft at pressure higher than in the reservoir. This keeps the oil and gas in the reservoir during drilling, but the high pressure can damage the rock around the wellbore.
Underbalanced drilling – a type of managed pressure drilling – uses lighter fluids or gases so pressure is lower than in the reservoir so that fluids can enter the well shaft. This prevents damage to the reservoir rock and allows oil and gas to flow freely, increasing production, he explains.
Shell uses underbalanced drilling to improve the flow of oil and gas at some of its operations, and to help gather more accurate data on underground reservoirs.
In underbalanced drilling the circulating drilling fluid lifts the drilled cuttings and gas to the surface. Shell analyses this mixture and, along with other data such as seismic surveys, learn more about the flow characteristics and geology of the reservoir. Shell is able to identify the most promising production areas and so drill fewer wells to find oil.
“We also use the data to identify areas where water may enter the reservoir and, for example, use expandable seals, called swellable elastomers, to keep any water out. We use underbalanced drilling at some stage in all our tight gas reservoirs, applying the technique as much as all other oil majors and national oil companies combined,” he explains.
On tight gas, he says it is not new, although it is always in the news. What is new is making tight gas drilling economical.
It is an area where there is long way to go for the industry. Many geoscience technologies are involved in it including acoustic sensing and fibre optics, which help assess the cost and environmental consequences. In Saudi Arabia’s Empty Quarter, the quest for tight gas in ongoing “where we have to wait for the results”, he says.
Tight gas is natural gas held in rock pores up to 20,000 times narrower than a human hair. Often the gas will not flow freely into a well, or it flows at a much slower rate than in normal gas reservoirs. The amount of gas that would be recovered from each well would be low but the overall volume of available gas in the reservoir can be much higher than conventional gas reservoirs. Technology is needed to produce it economically.
Shell has decades of production experience with tight gas – in the North Sea, mainland Europe, the US and Canada.
Over time it has found ways to safely develop the fields and produce the gas with greater efficiency, lowering costs and limiting the environmental impact. At its operations at Pinedale in Wyoming, the US, for example, Shell is now able to drill wells over twice as fast and at 30 per cent less cost than when it started.
Engineers must drill many more wells than in a conventional field to access volumes large enough to make a project worthwhile. Shell uses seismic sensors and advanced software to map out underground fields and pinpoint the best locations to drill. It uses steerable drills to extend many wells horizontally into the rock, often up to 2.5 km away, from one location on the surface. This also helps to increase efficiency and lower the environmental impact of Shell’s operations.
![]() |
Shell continues to invest in and develop |
“We crack open the rock at selected intervals within the well by pumping fluids (mainly water) into the well bore, a technique known as hydraulic fracturing.
This releases the gas and helps it to flow.
“At all our tight gas operations we use hydraulic fracturing to break open rock and release the gas. This is a safe and proven technique according to the US Environmental Protection Agency, which is now carrying out a new study into hydraulic fracturing and its potential impact.”
Shell is also doing a lot in enhance oil recovery (EOR), especially in Oman. EOR currently accounts for 4 per cent of global oil production. This could rise to 20 per cent by 2030.
Shell is using EOR to boost production at 11 projects across the world, at locations including Oman – through its joint venture with Petroleum Development Oman – the US, Russia and the Netherlands.
Explaining the concept, Schotman says, natural pressure in a reservoir will usually push oil out of from a newly drilled well. When the pressure drops, engineers inject water or gas produced with the oil back into the reservoir. This in turn helps to push out more oil – a technique known as improved oil recovery. Engineers may also encourage the flow using pumps, for example.
But oil producers typically only manage to recover around a third of a reservoir’s oil: the rest is left in the ground.
Injecting steam, chemicals or gas into a reservoir – a process called enhanced oil recovery (EOR) – eases the flow of oil and boosts recovery by an average of 10 per cent. In total it could help to unlock 300 billion more barrels of oil, equal to 10 years’ production at today’s levels.
Shell first used steam injection in the 1930s, in California, US. Since then it has installed numerous steam injection projects, and have trialled and set up commercial projects for the injection of CO2, and using chemicals.
“Each reservoir requires a tailor-made approach to enhanced oil recovery,” says Schotman. “Our extensive experience helps us to apply the best techniques to improve oil production and recovery at an acceptable cost.”
One benefit of this approach is that much of the infrastructure needed to produce and transport the oil, such as pipelines and roads, is already in place. And there are no exploration costs involved because the oil’s location is known.
Shell continues to invest in and develop new ways to flush out more oil. This includes improving existing EOR techniques and developing new ones, as well as enhancing technologies which support the process.
For example, Shell has developed Smart Fields technology, an advanced system that allows it to manage real-time information from sensors in the fields. These feed, for example, continuous temperature and pressure readings into a central database to create an up-to-the-minute model of the field. Engineers can make rapid adjustments to extract oil more effectively according to conditions, or react immediately to any sign of problems.
Some EOR techniques are energy-intensive, but Shell is finding ways to reduce the amount of energy it uses. At Qarn Alam and Amal in Oman, for example, 80 per cent of the steam needed for its projects comes from waste heat from local power stations.
Another technique is injecting steam, which heats the oil in a reservoir, thinning it and making it easier to produce. It also pushes the oil to wells where it can be better drawn to the surface.
![]() |
Pearl GTL will add almost 8 per cent to |
Shell is working on several full-scale steam EOR projects with Petroleum Development Oman. For example, at Qarn Alam oil is drained through the reservoir’s rock fractures. But the natural process is slow because the oil is very thick.
Injecting steam into the fractures is to raise recovery over the life of the field from 3-5 per cent to 20-35 per cent.
The next approach uses chemicals. In this, chemicals are mixed with water before injecting it into an oilfield to drive the oil out of the rock. The mixture is tailored to the properties of the rock, the oil and the water it contains.
Chemicals can be polymers or surfactants. Polymers are long-chained molecules that thicken the water. At Marmul in Oman, for example, saline water is produced along with the oil. The water is unsuitable for any other purpose and can be re-injected it to help push out more oil. The water is too thin to push out the dense oil so Shell removes impurities like sand, add a chemical polymer to thicken it and re-inject the mixture. This process began in February 2010 with the aim to increase production by 8,000 bpd and to raise the amount of oil recoverable from the field from 15 per cent to more than 25 per cent.
Injecting gases that can dissolve in oil – known as miscible gas – into a reservoir is the next technique. It creates a mixture that flows more easily through the reservoir to production wells.
Shell was one of the pioneers in injecting naturally produced CO2 to boost oil recovery from the Permian Basin in Texas, the US, in the 1970s. There it built one of the world’s largest CO2 EOR projects. Now it is looking at ways of using man-made CO2 from power plants for gas EOR.
“We also plan to use contaminated natural gas produced with oil in a project at Harweel in Oman. Here a gas rich in hydrogen sulphide will be re-injected into the reservoir to force out more oil. Using this approach we hope to recover up to 50 per cent of the oil, compared to 10 per cent using conventional production methods,” he says.
On the productive uses of sulphur, a by-product of gas production, Schotman says one of the most promising uses for sulphur comes from a Shell-patented technology that adds a mix of elemental sulphur and sulphate to fertilisers.
Shell Thiogro technology makes sulphur – a vital nutrient for many crops – more readily available to plants throughout the growing season. The benefits of more effective sulphur use in fertiliser could be significant: tests on crops by Shell and the Sulphur Institute in the US showed it can increase yields by 14 per cent on average in sulphur deficient soils.
Sulphur is also widely used in the construction industry. For example, adding sulphur pellets to asphalt helps make road surfaces more durable and resistant to extreme high and low temperatures. Shell Thiopave – also patented by Shell – mainly consists of sulphur and replaces up to 30 per cent of the bitumen used in making a road. It can be made at lower temperatures than conventional asphalt, offering an environmental benefit.
The Qatari Public Works Authority and Shell have been testing sulphur asphalt since July 2010 on a 150-metre strip of the Umm Bab highway, which sees heavy traffic by trucks, in the first trial on a public road in Qatar.
Shell and Qatar’s Khalid Cement have signed an agreement to develop uses for another product, sulphur concrete.
Manufacturing Shell Thiocrete requires no water and produces less CO2 than making traditional Portland-cement concrete. It reaches maximum strength within hours compared with weeks for cement concrete, he says.
Schotman says in adverse environments like the Arctic, Shell combines existing with new technologies, and Shell-developed technologies with those developed by others to create specific technical solutions to the challenges.
The strategy involves building on Shell’s Arctic and sub-Arctic operational experience gained from projects in Alaska, Sakhalin and the North Caspian Sea; applying Shell’s extensive and pioneering deep-water and well technology and experience gained from projects such as Ormen Lange off Norway; and working with industry partners to achieve shared standards and solutions, especially in the areas of safety and environmental protection.
The Arctic poses physical challenges including remoteness, ice, extreme temperatures and long periods of darkness in the winter. Advanced technology is needed to meet these challenges. It is also vital in protecting the region’s biodiversity, by reducing the operational footprint of discharges, air emissions and marine sound.
“Although oil spills in the offshore arctic are extremely rare we have well-developed plans in place to respond. We use a range of approaches and the first step is the use of multiple barriers. A multi-layered well control system is used to ensure that if any one system or device fails it should not lead to an uncontrolled oil spill,” he says.
On floating LNG (FLNG) projects, he says they are suitable for smaller reserves between as 2 tcf and 3 tcf. The biggest advantage is that FLNG avoids building a pipeline. So it is environment-friendly besides being cost efficient. The world has a lot of FLNG opportunities.
“We will set them up where it makes sense to avoid an onshore LNG plant and thereby save building a pipeline,” he says.
Shell now moving ahead with the world’s first FLNG plant, Prelude FLNG, off Australia’s north-west coast.
There are also plans to use the FLNG technology and expertise elsewhere. After an extensive and rigorous process to evaluate different possible concepts, the Woodside-led Sunrise Joint Venture has chosen Shell FLNG technology as the preferred option to develop the Greater Sunrise gas fields in the Timor Sea.
Recently Inpex announced that Shell also has been selected as a partner in Inpex’s Abadi gas field project off the coast of Indonesia, where the first phase of development will include the construction of an FLNG facility.
On gas to liquids (GTL) projects, he says GTL is not new to Shell. “We believe we can do more of these projects at many places in the world that are suitable for it. If not in the Middle East, we will continue to look globally for such opportunities,” he says.
Pearl GTL will add almost 8 per cent to Shell’s production worldwide – making it the company’s main engine for growth for 2012.
The proprietary Shell Middle Distillate Synthesis (SMDS) process is at the heart of the two-train Pearl GTL plant.
Developed over more than three decades, the process has been proven on a commercial scale at the 14,700-bpd Bintulu GTL plant in Malaysia, which began operation in 1993.
Shell has over 3,500 patents at all stages of the GTL process. The Bintulu experience helped improve the chemical catalysts integral to the SMDS process. These improvements will reduce unit capital expenditure, allow faster processing and should enable Shell to produce greater volumes of fuel and other products at Pearl.
Building on its extensive experience marketing GTL products from Bintulu, Shell will export Pearl’s high value, differentiated premium products, including GTL gasoil, kerosene, naphtha, normal paraffin and base oils for lubricants, to markets around the globe. And finally, Shell has found a way to use tiny motion sensors – like those used in modern everyday gadgets – to create sharper pictures of underground rock formations. They could help to find new oil and gas fields more cost effectively.
Geophysicists map underground rock structures by sending seismic waves – essentially sound – through the ground.
Sensors record the seismic waves and computers process the recordings to create images of the rock layers. But these seismic images may not be sharp enough to pick up important details. As a result, multi-million dollar exploration wells sometimes end up as dry holes.
The accuracy of seismic imaging could soon improve thanks to a motion sensor, similar to those found in electronic devices like the handheld controllers in a Wii game console. The sensor, developed by computer giant HP and Shell, is 1,000 times more sensitive than those in the Wii. In conventional seismic surveys hundreds of kilometres of cable are needed to carry the information back to a recording unit. But the new sensors are small enough to fit into a radio transmitter, and they need little power. So they can send information wirelessly – in a similar way to the Wii remote. Eliminating the cables reduces the cost of seismic surveys.
The sensors could potentially be mass-produced, further bringing down costs. This would make it possible to deploy them in far larger numbers than conventional seismic sensors.
If tests under way are successful, thousands of the wireless seismic sensors could be planted like seeds over an exploration area of up to 1,000 sq km. They would pick up millions of billions of readings– far more than conventional seismic sensors. And this would give Shell a clearer picture of its drilling targets, he adds.