
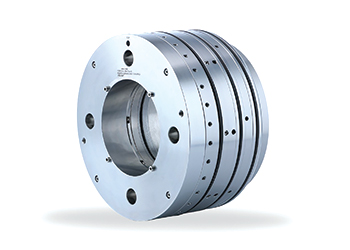
EagleBurgmann CobaDGS is the first dry gas seal that can seal compressors with zero process gas emissions (for example, methane) even under high working pressures. It is possible to seal pressures up to 160 bar.
The CobaDGS is a viable and sustainable option for upgrading existing compressors or can be installed in new compressors. It is also possible to substitute normal double arranged dry gas seals and provide the same function at a higher safety level, thanks to CobaSeal’s robust emergency behaviour.
For this project, EagleBurgmann developed a specially modified dry gas seal for a propylene compressor to help reduce the initial investment cost and to deliver a sealing solution characterized by maximum robustness.
The compressor is part of a plant for the production of propylene oxide, a plastic used for home furnishings, paints and coatings, household and industrial bottles, and more products used in many areas of everyday life.
A huge challenge for EagleBurgmann engineers was to fit a dry gas seal into the seal cavity previously designed for the oil-lubricated seal. In many cases this means the compressor housing and shaft has to be reworked in order to add additional supply or vent connections or to enlarge the installation space, which typically increases the project costs.
In the respective case, the compressor housing only had two connections. This technical prerequisite excluded a solution with a common tandem dry gas seal with intermediate labyrinth, which needs five connections; or a tandem seal with out intermediate labyrinth, which needs four connections, or a double seal which requires at least three connections.
The idea to use a CobaDGS from EagleBurgmann turned out to be perfect. This new product development is a coaxial dry gas seal that is based on the CobaSeal technology. It was adapted to this particular application so that it required only two connections without having to modify the housing. EagleBurgmann was the only supplier to offer such a solution, which helped the operator to significantly simplify the project and reduce investment costs.
The ultimate test: The CobaDGS completely seals the compressor shaft and does not cause any process gas emissions. It must be supplied with nitrogen, which only leaks in small quantities into the process medium. The designers naturally also considered emergencies, such as interruption or failure of the nitrogen supply. And that is exactly what happened shortly after successful installation and commissioning of the compressor. A valve of the nitrogen supply line was closed accidentally without the operator noticing anything at all. The compressor continued to operate. The situation was finally detected after eight days. When the technicians opened the valve, the compressor continued to operate as if nothing had happened.
The CobaDGS operated the entire time without the nitrogen supply. The technicians detected only minor leakage of process gas into the vent line. Common double dry gas seals, by contrast, would have failed due to the reverse pressure situation. Labyrinths or carbon rings, at least, would have lost their sealing function and the carbon rings most likely would have overheated due to the lack of cooling. It is not surprising the operator was very impressed by this robust emergency behaviour of the CobaDGS.
The case demonstrates that the coaxial design provides greater safety and more robustness than the common design of double dry gas seals in case the nitrogen supply fails. On top of that, the CobaDGS is a solution which prevents process as emissions from entering the environment.
The features of the CobaDGS include:
• Gas-lubricated.
• Bi-directional.
• Ready-to-fit cartridge unit.
• Available as single and tandem seal arrangement.
• Co-axial primary seal.
• Separation seals as CobaSeal, carbon rings or labyrinths optional.
Its advantages include:
• No methane and process gas emissions.
• Supplied with clean nitrogen (no dew point and dirt problems).
• Robust.
• Offers higher safety than a double seal.
• Upgrade possibility of existing single, double and tandem seals.
• No modification of the compressor necessary.
• Efficient alternative to hermetically sealed systems.
• For compressors with gas and steam turbines as well as with electric drive.
The benefits of using a CobaDGS for the plant operator include considerable cost savings, emission reduction, and longer MTBM.