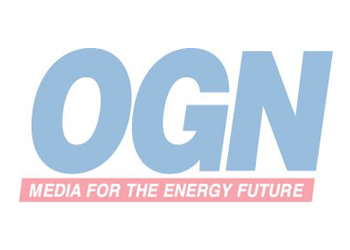
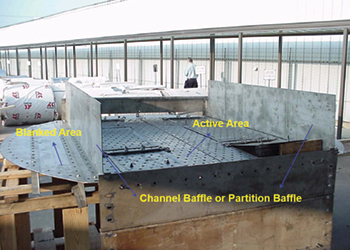
As refineries strive to meet changing market requirements with minimal capital expenditure (capex) by upgrading existing separation units, working together with a processing technology specialist can deliver advanced performance and the flexibility to support new applications while also reducing waste.
One UAE-based refinery turned to Sulzer Chemtech to convert one of its vacuum distillation units (VDUs) into an atmospheric naphtha-kerosene separation column. The result is a highly effective unit designed to help enhance the refinery’s competitiveness.
To support its growth and changing requirements while optimising capex, the refinery wanted to modify an existing VDU, used to separate vacuum gas oil (VGO) and lube base oils, into an atmospheric distillation unit (ADU).
THE OBJECTIVE & CHALLENGES
In order to optimise the existing equipment’s service life and the overall capex, the refinery was keen to maintain most of the structure, that is, the shell and support for column internals.
As no technical drawings or blueprints were available, Sulzer Chemtech’s field service team visited the site to take measurements in the column and prepare as-built drawings to use as a basis for the entire conversion project.
With a diameter of over 5 m, the unit consisted of 21 two-pass bubble cap trays, an over flash chimney tray located above the flash zone and four sieve trays in the stripping section, including another chimney tray. The existing column diameter was way too oversized to handle new requirement.
A TRAY TO SUIT THE PURPOSE
The solution provided by Sulzer Chemtech minimised the number of perforations, in the form of valves, to further reduce the open area and prevent weeping while reducing pressure drop.
The flow path length supports optimum vapour-liquid contacting and the channeled active areas improve jet flood at lower vapour rates. Furthermore, the updated design accommodates the existing downcomer width, eliminating the need for further modifications.
In effect, channel baffle trays restrict the contact activity into a limited space while preventing vapor and liquid spreading across the entire cross-sectional area of large towers.
This setup also supports the proper loading of the weir. Specifically, the channel baffles decrease the available weir length to prevent liquid stagnation and decrease the active area to prevent weeping.
In this case, as the existing trays were of two-pass, Sulzer Chemtech’s specialists designed the new channel baffle trays with a similar arrangement. This avoided modifications to the tray support rings and weld attachments.
FAST TURNAROUND & ADVANCED CAPABILITIES
Sulzer Chemtech’s fabrication centre was able to complete the manufacture and delivery of the new trays in less than six months.
The fabrication of these key components was fast-tracked, so that Sulzer Chemtech’s field service specialists could install the equipment during the refinery’s next scheduled shutdown, eliminating the need for any downtime specific to the project.
The solution provided, consisting of 19 trays, could process revised feed rate and deliver end products that meet the stringent specifications of the American Society for Testing and Materials’ (ASTM) D86 standards.
In particular, the un-stabilised naphtha and kerosene produced featured a sulphur content of 0.0005%M and 0.008%M, respectively.