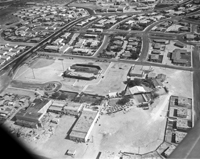
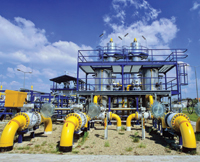
VALVES, the heart of oil, gas and petrochemical plants and production facilities are valuable assets. Well heads, X-mass trees, platforms valves, wing valves, upper master valves, lower master valves, ZVs, MOVs, PCVs, HCVs, launcher and receiver valves for scrapers are so critical in production that no company can afford to have any problems with them.
Saudi Arabia-based Oil & Gas Services Gate Company (OGSG) says replacing valves should always be the last option as replacing them will cause a big loss in production because of shutdown; replacing them will mean spending on high-priced new valves; and replacing them will lead to delay in operation due to a long lead time for manufacturers to supply valves.
![]() |
Ibrahim ... new initiative |
Haddad Ibrahim, operations manager, OGSG says he has a solution for all the above-mentioned problems with OGSG’s latest high-tech equipment, injectable materials and top-quality fittings.
OGSG, constantly, introduces and transfers new state-of-the-art technologies from the US and Western Europe to Saudi Arabia to familiarise his Saudi Arabian crew, technicians and engineers with the latest technology.
The company has introduced an online leak sealing service, which ensures smooth and safe operation and an extended life of valves, thereby leading to reduction of maintenance costs.
According to Ibrahim, this new service injects a flush cleaner fluid specially designed for valves, cleans all deposits on valves ball, gate and plug valves and removes all scale and corrosion inside the valves. It also applies a specially formulated lubricant to open and close valves easily, which helps field operators to con trol their production process.
Ibrahim adds that an integrity test for the serviced valve is performed to see if there’s any leakage of oil or gas. The last step is injecting a special super sealant into valve seals and seats to stop any leakage inside to make sure downstream is zero pressure.
Additionally, special stem packing materials are developed by the Val-Tex Company in the US, to stop valve stem passing or external leaking of crude oil or sour gas to the atmosphere, preventing any harm to the personnel or the environment.
This technology can be applied to various types of production valves such as ball, gate, plug, ZVs, MOVs, PCVs, valves of any brand, any size and any manufacturer. These can be used for even onshore, offshore and subsea valves seized, jammed, passing, leaking, stuck open, stuck closed valves and hard operation valves, says Ibrahim.
Applying this new technology eliminates the need to change defective valves with new and very costly valves which can have a long lead time to deliver and thus lead to loss of production.
“Our new technology will save 60 per cent maintenance costs to production facilities and extend service life of their facilities’ wells, x-mass trees, valves and equipment,” says Ibrahim. “Never replace your valve unless you have no other option,” he adds.