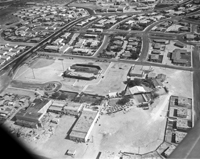
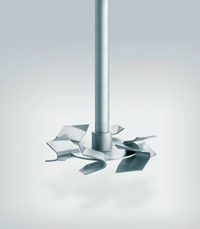
THE Ekato Group, with its headquarters in Schopfheim, Germany, is the global market leader in mixing and blending technology. Being mainly active in the market of bulk chemicals and polymers, Ekato’s activities range down into the fields of pharmaceuticals, biotechnology, paints and coatings, flue gas desulphurisation for power stations, hydrometallurgy, and even cosmetics and food.
Building the world’s largest agitators: The market more and more demands ‘world-scale’ systems. As a producer in the process industry, Ekato has the competitive advantage through ‘economies of scale’, helping companies to reduce and control production costs. At the same time, investment costs as well as maintenance costs have to be reduced.
Building the world’s largest agitators, Ekato bundles know-how in the fields of mechanical agitator design as well as mechanical seals. For this purpose, knowledge of hydraulic loads on components and state-of-the-art methods of finite element and modal analysis, including fluid structure coupling, lead to cost-optimised, operationally safe designs. All parts of the agitator are manufactured and assembled exclusively in Ekato’s factories in Germany.
Ekato bridges the ‘gap’ between mixing and process technology: What is unusual about a supplier of large process equipment is that Ekato has its own research and development (R&D) department, which is not only handling the mechanical development, but also – and as a focus – the process development. As a provider of reliable mixing equipment, one has to understand how the agitator influences the process performance, that is, how product quality and process capacity or throughput can be increased.
For this purpose Ekato opened a new R&D centre in January 2013, comprising a large pilot plant with a 100 sq m test pit, several laboratories and more than 20 experts working in the fields of petrochemical processes, polymerisation, crystallisation, fermentation, mining, and others.
Here, the Ekato experts are continuously looking for the optimum, customised mixing setup, as the world of process technology becomes more and more diverse.
![]() |
Ekato draft tube circulator streamlines |
This is very often done with the help of specific trials, where customers may join and, consequently, have a “deeper look” into their own process. For this purpose, either model fluids are used – to directly visualise the mixing performance – or the original process is run in the laboratory, with the “real chemistry”.
Here, analytic tools specified by the customer are used to control the process result.
Exclusively for a company working in mixing technology, Ekato has its own CFD (Computational Fluid Design) department, with experts working on flow simulations for customer projects as well as for the further development of Ekato’s portfolio of impellers and mixing systems. Combining CFD and corresponding experiments delivers a powerful tool not only to find a suitable mixing setup for the corresponding process, but also to investigate the influence of flow-related and process-relevant parameters.
Most important, and on top of the investigations described above, a reliable scale-up leads to the optimum solution for the process.
Example: Mixing solutions for bulk chemicals: When producing bulk petrochemicals, gas-liquid dispersion is one of the central mixing tasks inside large reactors.
Together with this, quick blending of these large reactors plus reliable removal of the heat of reaction are crucial. In order to provide all this in a most efficient way, the Ekato Phasejet impeller was developed. Because of the special design, i.e. blade geometry, it provides most efficient gassing and blending – together with a very low power drop. So the same performance is reached with significantly lower power input, if compared with a conventional gas-liquid disperser like the Rushton turbine.
A setup of multi-stage Phasejet impellers e.g. do their work in the world’s largest gassing reactors to produce PTA (Purified Terephthalic Acid).
Example: Mixing solutions for polymers: Polymerisation reactions are chemically and physically complex. Again, several mixing tasks have to be solved simultaneously. Depending on the process or the polymer specification most different components in various phases have to be handled. What is more, high viscosities and flow anomalies must be considered.
For a polymer reactor, the process result in terms of mixing mainly is defined by dispersion, homogenisation and suspension tasks. At the same time, providing a substantial ability to remove heat is inevitable. Productivity and product quality of the entire process are therefore directly dependent on the mixing system inside the reactor.
Correspondingly, the current trend in industrial practice is going away from standardised solutions towards individual solutions. In the polymerisation process all functional components and their interaction with the impellers are being taken into consideration. One no longer talks about the agitator alone but about the complete mixing system. As a result, production and investment costs can be lowered and the productivity of the reactor can be increased.
BPA (Bisphenol A) is a very common monomer to produce Polycarbonates and Epoxy resins. To crystallise and purify BPA large DTB (Draft Tube Baffled) crystallisers are used. Inside these crystallisers, large impellers are running to provide a loop flow together with most efficient suspending of the crystals. The more energy efficient the pumping is done, the easier can the crystal size be controlled, which is elementary for product quality. This is done with the help of the Ekato draft tube circulator plus tailor-made guide vanes, which smoothly provide this kind of pumping.
A very comparable setup can be found in butyl rubber reactors, which due to a very fast polyreaction have to work at very low temperatures. Here, the heat exchanger is placed in the “ring room” of a draft tube reactor, where the reaction mixture is efficiently cooled.
All this helps to manufacture customised, well-suited agitators – ideally together with the corresponding process solution. As a consequence, economically important factors for the customer – as there is: reliability of the equipment; product quality; and production capacity or throughput are improved.
In this manner, process innovation increases economic efficiency, even in mature technologies.