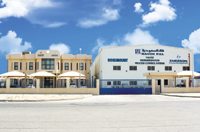
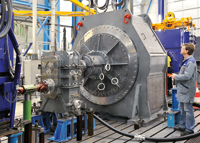
THE power distribution gear unit by Voith Turbo BHS Getriebe is the modern answer to increased demand for high power density gear units capable of transmitting high power at high rotational speeds. By combining the load distribution principle of epicyclic gears with the simplified design of a parallel shaft gear, operating efficiencies of 99 per cent are possible.
At first glance, the construction of the BHS power distribution gear is very similar to that of a standard epicyclic gear: Three planet gears are arrayed around a central sun pinion.
However, each planet gear is actually a compound design which meshes with two sun pinion shafts: one input shaft and one output shaft. This design enables the power distribution gear to act as a two-stage parallel shaft gear, but without high speed bearings and with a coaxial input and output shaft arrangement. Since power is distributed over three two-stage planet gears without need for a ring gear, the overall gearbox size is quite compact. In addition, the three planet gears are supported by six bearings instead of four (as in parallel shaft gear units), which means bearing diameters and journal velocities are reduced compared to a parallel shaft unit of the same power and speed transmission, while load capacity is increased.
Due to this load distribution feature, which segments the load into several smaller components, the BHS power distribution gear unit is the ideal solution for high power, high speed applications. Gas turbine driven compressors provide a classic example. Comparative calculations show the superiority of the power distribution gear unit as opposed to parallel shaft gear units. For a typical gas turbine to compressor application with speeds of 5,000/12,500 rpm, the maximum transmitted power of the parallel shaft gear unit is limited to 26 Megawatts (MW), because speeds cannot be increased at the bearings or the toothing. Within this range, efficiency is only 98.1 per cent for the parallel shaft gear unit, compared to 98.8 per cent for a power distribution gear unit. The power distribution gear in this example is able to transmit up to 65 MW of power without losing any efficiency.
The load distribution principle allows optimisation of rotating components while staying well within accepted limits, reducing centrifugal forces and material stresses compared to parallel shaft gears. This also has a positive effect on the service life and the operating safety of the components in the turbo gear unit.
Another feature of the power distribution gear unit is the integrated BHS TwinTors double diaphragm coupling, which ensures an ideal power transmission connection between driver and driven machine. Both the high and low speed sides of the gear unit include such a coupling.
The integration of these couplings into the gear unit turns the BHS power distribution gear into an axially compact unit, popular among customers for its space saving advantages. Axial, radial, and angular offsets in the train are reliably compensated by the patented double diaphragm coupling. This design permits optimum load distribution within the gear unit, enabling BHS to deliver a rotor dynamically optimised system consisting of both gear unit and connecting couplings. Ease of maintenance also played a role. The split casing, for example, provides ready access for inspection and maintenance work. BHS delivers power distribution gear units with up to 170 MW power (3,600 to 3,000 rpm) or rotational speeds of up to 80,000 rpm. The power distribution gear unit is ideally suited for applications outside the range of technical feasibility of parallel shaft and epicyclic gear units.