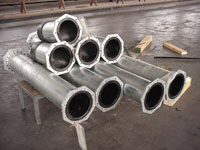
Alkhorayef meets HDPE pipeline lining target in one year at Riyadh facility alkhorayef Industries Co., the industrial arm of AI Alkhorayef Sons Group of Companies, which has been in business since 1957, has announced that its High Density Polyethylene (HDPE) lining facility in Riyadh's Second Industrial City has reached its target of lining more than one million metres of pipe and tubing in twelve months, according to marketing and sales manager of the company, M R Alhaj.
The company possesses the largest industrial line for the HDPE lining of pipes and tubing in the world. Spool pipes, up to 40 metres long and 24 inches in diameter, could be lined online. Special pieces and fittings can either be lined on the same line or plastic flame coated.
With state-of-the-art equipment, a fully equipped laboratory and dedicated R&D, production, QA and marketing staff, Alkhorayef Industries hopes to cover every foreseeable requirement of the oil, water, waste water and mining slurries pipe market, not only in Saudi Arabia but also throughout the Middle East.
''This region, in particular, presents a very corrosive environment for conventional pipes'' said Alhaj. ''Externally, the hostile soil and the saline, ever-rising water table places buried pipes in extremely harsh conditions.
''Inside the pipeline, abrasion, due to suspended particles in the flow stream, and corrosion caused mainly by the reduced pH value due to gases, chlorination and other factors, can have deleterious effects on the bare pipe wall,'' he explained.
''Our aim is to find better ways of increasing profitability of our customers' pipelines,'' he continued.
''Alkhorayef realised that the greatest cost of a pipeline project, whether offshore, buried or installed above ground, is usually not the cost of the pipe itself but the cost of other project activities such as preparation, diversion of existing services, excavation, shoring, safety precautions, bedding, supporting structure and foundations, pipeline installation, line pressure testing, back-fill and compaction, and site restoration. The longer the useful life of the installed pipeline, the greater the value to the pipeline owner and user.''
Established in the early nineties in Riyadh, this HDPE lining facility utilises the modern technology of HDPE lining and sleeving to protect steel pipes, and other metallic tubulars utilising a very economic and available material, HDPE.
Alhaj explains: ''The potential of utilising the patented technologies of Ultrapipe compressive-fit, annulus-free HDPE lining of pipes together with Mould-a-flange end forming the liner, ensures that not only is the pressurised pipeline leak free but also that its durability and economies are non-comparable with other options.
The principle is very simple. The steel pipe resists internal and external pressures, and the HDPE resists corrosion, erosion and scale build-up, while improving flow efficiency.
Conventional liners include expensive rubber, cement mortar which chips and cracks during transportation, handling, installation and/or erode and degrade over time, thin paints, sprayed or fused on, which would crack and separate, and brittle expensive fibreglass/RTR and polyurethane.
They are all also known to experience major problems at joints, whether welded, flanged or threaded. Pipe deformation, another major problem, is also experienced with non-metallic pipes, whether used above or below ground
Ultrapipe, can resist pressures up to 200 bar or much more, depending on the pipe rating, and can withstand temperatures of between 65 and 92 degrees centigrade, depending on the transported medium.
''A recently announced breakthrough in polymers technology will very soon provide us with a string of HDPE liners that could withstand temperatures as high as 120 degrees centigrade.'' Alhaj adds eagerly.
This revolutionary new pipe can be used in the oil industry as a downhole tubing for disposal, injection or production wells, or to transport anything from sea water, brine, fire fighting water, to crude oil, gases and chemicals. It can be also used by municipalities to transport water and sewage and by mining companies to transport mine slurries. Ultrapipe has been successfully used in the region since 1992 for various purposes.
Ultrapipe can also be lined in-situ. HDPE lining, which can be used to protect new pipelines or rehabilitate old ones, is possibly the most cost effective and successful field application for erosion and corrosion abatement available today. More than 30 projects have been successfully completed using Ultrapipe in Oman, Qatar, Saudi Arabia and Syria.
Experienced crews, HDPE liners and truck-mounted equipment can be mobilised within a short period of time anywhere in the region to complete the required work. Cutting edge compressive-fit technology is used to install engineered grade HDPE liner into pipes up to 24" in diameter, and mould the HDPE on the flanges.
HDPE lining allows the client to save a considerable amount of money on steel pipe weight. 3mm of pipe thickness, which would usually be incorporated in the design to account for corrosion, can be eliminated.
Alkhorayef's in-situ lining offers additional advantages over other lining and thin epoxy coating systems. These include: on site lining, no prior surface preparation, all types of welded pipes can be lined, no effect of contraction/expansion following temperature changes, no worries about spillage, environmental hazards, setting time or shelf life, and no need for personnel to enter inside the pipeline to complete welded joints or inspect surface preparation or coating.
''Think about this, we are not talking about microns of thin coat applied to the inside the pipe wall - the client will have three to 14 mm of HDPE pipeline inside his steel pipeline, under compressive fit.'' Alhaj concluded.