
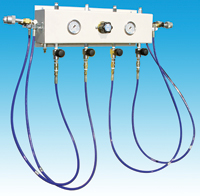
BAUER Kompressoren has manufactured and provided performance-proven, high pressure, breathing air solutions for over 60 years.
“From humble beginnings in the Bauer family home in Munich, Germany in 1946, to our current status as the industry leader, we remain poised to provide solutions for your requirements. We have earned our reputation as the world’s foremost innovator in design and manufacture of high pressure compressors, purification systems and components,” says a spokesperson.
The Bauer offshore series of compressor packages were designed to specifically meet and exceed offshore breathing air requirements. At the heart of every compressor package is one of the company’s performance-proven, air-cooled compressors.
Coupled to either a TEFC electric motor or a water-cooled diesel engine, Bauer is able to tailor the system to meet customer specific requirements. The NEMA-4 and or IP65 electrical enclosures all carry a UL certification as standard.
Additional features included within Bauer’s standard scope of supply, which are optional on other manufacturers’ equipment, include stainless steel fasteners and pneumatic fittings, base-frame and enclosure components fabricated of aluminium alloy; with integral forklift slots and lifting eyes. To further enhance this robust package against the effects of corrosion, Bauer applies a multiple layer base and topcoat of powder coating utilising its unique paint process.
![]() |
Last but not least, Bauer’s ME13-E3/D compressor is built to operate at 50 degrees C straight out of the shipping crate. “We can also tailor the package to operate at extreme temperatures up to 60 degrees C with only minor modifications. Equipped with H2S and CO monitoring, these packages can be used within any H2S safety application,” she says.
Typical offshore drilling rigs will have three of these compressors installed, with two of the units powered by electric motors being their primary source for high pressure breathing air. The third unit, powered by a water-cooled diesel engine is utilised as a “reserve” system in the rare instance that the rig loses electrical power. Each compressor is capable of discharging air at up to 6,000 psig.
However, a typical installation includes an air storage system comprising multiple storage cylinders rated at 5,000 psig, with each cylinder accommodating at least 472 cubic feet at pressure. These are all piped together providing large volumes of stored high pressure breathing air. The compressor is set to start and stop based on the pressure demand in the system – switching off at maximum pressure then restarting at typically 4,500 psig.
Installations of this nature are more often than not containerised solutions, as they consolidate all of the high pressure breathing air piping and ancillary gear in one location, making it easier for deck movement without fear of system contamination or hazards.
![]() |
The series 2 stationary nitrogen generation |
These installations are frequently utilised when trace elements of H2S are, or may be, present on the rig and operators are required to wear a self contained breathing apparatus (SCBA). However these packages are also used in support of fire-fighting operations wherein firefighters may be required to wear an SCBA.
The SCBA is typically rated for a maximum operating pressure of 4,500 psig and depending upon the volume of the cylinder will have a duration of 30 to 60-minutes depending upon what is specified by the operator.
The SCBA filling process is quite simple, she explains. The 5,000 psig stored air is decanted into the 4,500 psig SCBA via manually operated filling panel, as depicted in the picture (top right).
Air comes into the basic fill panel via high pressure piping with the incoming pressure indicated on the inlet pressure gauge. The operator regulates down to the maximum SCBA fill pressure via manually turning the regulator adjusting knob either counter or clockwise.
The regulated pressure is indicated on the regulated air outlet gauge, and then directed to the SCBA fill whips. During the fill process the SCBA cylinder is placed either on a work bench, inside a length of pipe or in some instances is filled directly on the back of the user.
For rig operators wishing to maximise operator safety, there have been significant advancements in recent history that remove the risk of fragmentation injuries from ruptured fill whips or SCBA cylinders during the fill process.
![]() |
Called a containment fill station (CFS), these devices are a repository for the SCBA cylinder during the fill process. The chamber where the cylinder is placed provides a barrier between the fill whip, cylinder and the operator during the fill process.
These fill stations are tested in accordance with the National Fire Protection Association (NFPA) standard number 1901 to contain the fragments of a ruptured cylinder during the fill process. Bauer offers a complete line of fill stations exceeding the current NFPA 1901 standard. A hands-free door interlock prohibits operation of the fill station with the door open, thus maximising operator safety.
The control panel operates in a similar way as the basic fill panel described above.
If the rig operator requires a CFS, it should be specified during the procurement phase that a NFPA approved version with original prototype test certificate must be provided. If not the operator may not receive a fully tested product and risks exposing the fill station operator to the hazards of fragments from a ruptured SCBA cylinder.
Thus far a high pressure breathing air system with separate compressor and storage components has been illustrated.
However, Bauer also has the capability to consolidate the entire high pressure breathing air solution into two containers.
This type of solution is engineered and manufactured to the customer’s specific requirements. System concept begins with a sit-down, in-depth analysis with one of our globally located application specialists to match client expectations.
The client required a compressor system with a sound attenuated enclosure, air storage cylinders, fill panel and SCBA storage consolidated into one containerised solution.
While for generations Bauer has been recognised as the world leader in high pressure breathing air, many do not realise that the breathing air market is just one segment that the firm operates in.
The wide and varied products manufactured by Bauer will fit any application requiring medium to high pressure air or gas compression.
Applications include instrument air, component testing, CNG fuelling stations, and most fittingly to the oil and gas industry nitrogen gas generation. Bauer offers a line of nitrogen generators up to 750 scfm and capable of pressures of up to 5,000 psig.
Bauer has a successful history of providing performance-proven nitrogen generators, installed on floating production storage and offloading vessels (FPSO) utilised for well stimulation, fire blanketing, flare gas purging, and for charging of surface and subsea blow out preventer accumulators.