
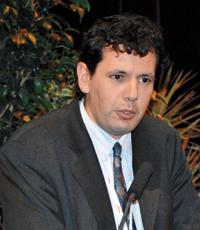
MATERIAL failure linked to sulphides is a major issue in upstream oil and gas as well as in refining and petrochemistry for over half a century and is a likely risk in future exploitation as the hydrocarbon resources tend to become more corrosive.
Economically optimised choices make it so that potentially sensitive C-Mn steels are used in a number of processing and transporting equipments. Steels have thus been enhanced into materials with improved properties, says Dr Patrick Toussaint, marketing and product support manager with Industeel, a subsidiary of ArcelorMittal specialised in advanced technology carbon, alloy and stainless steel plates.
Steel in contact with H2S-containing water can corrode and undergo ensuing hydrogen absorption into the steel. At the typical working temperatures of 200-degrees C and below, those hydrogen atoms can become trapped, causing embrittlement and ultimately cracking.
H2S leads to a number of problematic risks in steels, such as sulphide stress cracking (SSC), hydrogen induced cracking (HIC) and stress oriented hydrogen induced cracking (Sohic), he explains. Better H2S resistance is provided by a combination of improved chemistry, cleanliness, processing, homogeneity and microstructure, he says.
![]() |
Industeel supplies highly resistant |
Industeel developed its family of C-Mn CarElso normalised grades in order to satisfy the requirements for plates from six to 200 mm thick and beyond. A CLR index of maximum five per cent is commonly achieved thanks to the high level of quality of the steel. More than 20,000 tonnes of HIC resistant steel plates are delivered yearly by Industeel and the company is a recognised supplier for many major actors in the oil and gas business worldwide.
Steelmaking includes vacuum ladle refining after electric arc furnace melting of selected scraps, to enable the making of very clean high quality C-Mn steel with:
• Very low oxygen (O≤ 0.0015 per cent), to minimise total inclusions count;
• Very low sulphur (S≤ 0.001 per cent), whereby Ca treatment is unneeded and even detrimental to HIC resistance;
• Very low phosphorus (P≤ 0.008 per cent with an average level of 0.006 per cent usually obtained); toavoid crack-propagating intergranular segregation effects;
• Very well controlled chemical composition with optimised alloying to guarantee low while sufficient Ceq to achieve required mechanical characteristics. The typical Ceq range is 0.38 to 0.45 depending on thickness and delivery conditions, as thicker plates need higher Ceq whereas a “quenched and tempered”, or “normalised accelerated cooling and tempered” route allows for lower Ceq;
• Soft-reduction continuous casting or ingot casting under argon protection with optimised mould shape, to control solidification conditions and limit occurrence of segregation.
At the final stage of fabrication of equipments, a proper PWHT is strongly recommended. For C-Mn normalised grades produced by Industeel, typically according to the ASME SA516 standard, 610 deg C is necessary and sufficient to achieve proper stress relieving of the welds with ample reserve for other treatments, good mechanical properties, safely low hardness levels, and excellent H2S resistance.
Industeel today not only supplies highly resistant normalised H2S resistant steel plates under its CarElso brand, but has developed a complementary product line for demanding applications in pressure vessels and piping, meeting the needs for example of ASME SA533 type E class 2 and API 5L appendix H X65QS, in quenched and tempered condition, thereby more demanding strength and corrosion resistance.
Where pressure vessel weight or thickness limitation is important, a new high strength steel grade with 500MPa SMYS and resistance to H2S has been developed and already put in use for several offshore projects, branded as SuperElso 500HIC.
CarElso HIC Premium+, an optimised design meeting most existing standards for HIC resistant normalised steels is also available, from the mill as well as from selected distributors worldwide.