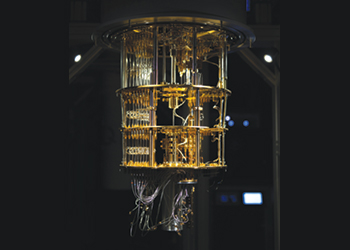
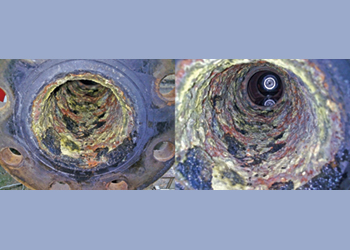
The company has helped O&G operators save hundreds of thousands of dollars in lost revenue by using its water chemistry-based process modeling software and innovative Cloud APIs to resolve issues related to corrosion and mineral scaling, Vineeth Ram, Chief Revenue Office, tells OGN
A primary challenge facing the oil and gas industry today is to produce more at lower cost with less emissions.
To operate as effectively, sustainably, and economically as possible, oil and gas companies must be able to predict when and where problems will occur as well as optimise the use of materials and resources to drive profit margins.
They must optimise process design to enhance operations efficiency, increase reliability and, improve sustainable water treatment by embracing the latest technology innovations to evolve their procedures.
Mitigating the risk of mineral scaling and corrosion—a major cause of equipment failure and lost production—is critical to improving asset efficiency and equipment reliability by enabling producers to extend asset life and increase well productivity, integrity, and yield.
INDUSTRY LEADING WATER CHEMISTRY PROCESS SIMULATION
![]() |
OLI Cloud APIs automate process design and operations analysis to accelerate |
For over 50 years OLI Systems has been leading the industry with water chemistry-based process modeling solutions with software and services to improve process design and accurately predict operational risk and enhance sustainability. These solutions help companies:
• Design water handling and disposal facilities.
• Simulate production and processing.
• Calculate the likelihood of corrosion or mineral scaling.
• Develop integrity operating windows to enhance asset reliability.
• Identify and eliminate toxic contaminants in produced water.
• Enhance the ability to effectively capture, store and transport CO2.
OLI has developed ionic modeling technology to identify the causes of corrosion due to contaminants and predict localised corrosion of corrosion resistant alloys (CRAs).
Recently, OLI expanded its monitoring and automation solutions with Cloud APIs and Cloud Apps to accelerate digital transformation and operations excellence.
OLI Systems has a rich history of working closely with global oil and gas companies to improve safety, productivity, reliability, and performance in upstream, midstream, and downstream operations.
OLI’s models are highly accurate and deliver attractive outcomes to clients as demonstrated by the following case studies.
OPTIMISING DOWNHOLE CHEMICAL TREATMENT TO REDUCE EQUIPMENT FAILURE
An OLI client in the oil and gas chemicals business used OLI’s software and expert consulting capabilities to mitigate corrosion and optimise drilling performance for its customers.
This client was unable to deliver effective downhole chemical treatments that would ensure superior integrity and performance in acid pumping and delivery systems because of the extremely corrosive environment in the oilfields.
Downhole equipment was at risk of catastrophic failure within just six months and in one case teams were twice forced to replace over one hundred segments of tubing in less than three months.
OLI helped the client predict the extent of the carbon dioxide corrosion damage as well as the possibility of oxygen-induced or freshwater-induced corrosion to pinpoint the exact causes and locations of the corrosion, and to aid the selection of ideal operating materials to prevent future corrosion issues.
The OLI Studio software was used to analyse the root of the issue in the affected tubing.
The introduction and mixing of oxygen-rich freshwater with produced fluids in the downhole equipment was modeled accurately and results indicated that general corrosion rates increased by 5–15 millimetre per year (mpy) in each of the scenarios.
They also found that maximum pit current density increased by 25–40 per cent on models when oxygen-rich freshwater was added.
Finally, the polarisation curve generated by the software determined a strong influence of oxygen-accelerated corrosion.
This client operationalised these vital insights to establish a trial to chemically control the oxygen concentration of introduced freshwater and dramatically increase the reliability of the downhole equipment across several drill sites.
Based on OLI’s insights, the client also implemented an electronic submersible pump to efficiently and reliably deliver the desired flow rate of fluids which led to remarkable results.
Only less than 10 segments of tubing were replaced due to corrosion. Meanwhile corrosion reduction occurred with a one hundred per cent greater exposure time leading to savings of hundreds of thousands of dollars across a small number of wells.
To quote a technology leader from this client: 'An investment in OLI Systems provided significant rates of return to our staff in productivity and confidence, and to our clients by optimising their operations. OLI Studio: Corrosion Analyzer was a vital tool in diagnosing the root cause of metal loss and identifying the best course of treatment.'
AUTOMATED PROCESS DESIGN WITH OLI CLOUD APIS
An oilfield services company used OLI Cloud APIs to automate process design and operations analysis to accelerate well monitoring and reduce risk of mineral scaling.
This client was challenged to perform complete water analyses on its wells due to limited workforce capacity and pressing time constraints.
The company had stopped using complete water analyses and instead performed scale modeling to keep its assets moving.
However, the water produced in its oilfield was about 30 per cent total dissolved solids, which, if left untreated, would solidify and shut off some wells within a year and others in as little as 30 days.
This client used the breakthrough OLI Cloud API capabilities to transform the process of well monitoring to automatically detect and predict scale formation with models that could be created instantly, saving the companies hundreds of person-hours.
The OLI solution met the client’s key requirements; utilise existing data ‘as is’, require no manual intervention, and generated output be readily accepted by their data interpretation software.
This client implemented OLI Cloud APIs to create a fully-automated system that enabled engineers to access software modeling applications with access to electrolyte calculations anywhere and anytime.
According to one technical specialist, the final system flow has streamlined complete water analyses, converting output data into well scale models 'magically'.
The solution started with the client’s lab database, which hosts twenty-six data points for every water analysis.
The specified data was extracted and pushed to the OLI Cloud API, where oilwell mineral scaling risks are generated instantly.
Previously, it took a trained engineer, at least, 3 minutes to produce a single scale model. This equates to 12 weeks a year.
The opportunity cost for an engineer was astronomical, particularly in a region with few local experts.
Today, the company is running complete water analyses and sharing automated chemistry insights in the cloud; the new system has resulted in a complete removal of manual scale modeling.
The ability to access the OLI Engine for well scale monitoring has removed geographic restrictions and created incredible efficiencies, delivering access to important insights using only a web browser.
This has empowered the operator to take on massive projects with production models that utilise large-scale data and output hundreds of complete water analyses, thus helping it identify the best locations to drill as well as predict the risk of scale as conditions change overtime.
This is especially important in areas where 50 per cent of scales are radioactive and incredibly expensive to remove.
A technical specialist of this client says: 'Even saving 50 per cent more time would not convince us to return to complete water analyses. We needed scale models that could take our output data and show up magically—which is exactly what OLI Cloud APIs allowed us to do.'