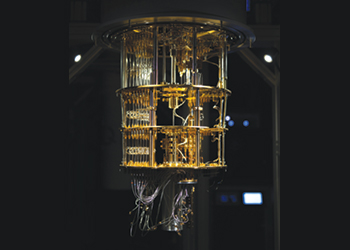
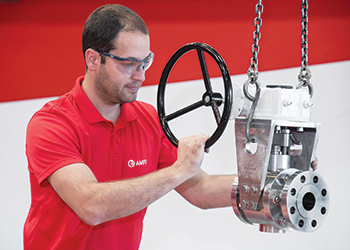
Considered the best in class in terms of severe use application, the valve evades the technical compromises that affect some of other products for these applications, Salah Elkadiki, CEO, AMPO Arabia tells OGN
The present day industry is experiencing an increasing demand for high-integrity and enhanced performance valves for specific critical applications and severe service condition.
AMPO POYAM Valves, a world leader in highly engineered valves and integrated smart solutions based in Idiazabal (Spain), took up the challenge, and following an accurate market research through its high-profile client network, identified common criticalities to its R&D team to design a product, which could offer a specific value proposition for such critical service applications demand.
After over a year, AMPO successfully completed the design and tested a product, which brings together the features of the best industry standard high performance valves into one product: AMPO POYAM Valves’ Hypercentric ball valve.
![]() |
Named Hypercentric ball valve from its unique, yet proven sealing concept, the product combines the strength and integrity of a metal-to-metal trunnion ball valve with the positive sealing performances of the triple offset butterfly valve — a widely known and used design in process flow applications.
One of the key tasks of AMPO’s R&D team was in fact to design a valve solution with known and familiar characteristic to the operators.
"The Hypercentric ball valve design can be considered the ‘best in class’ in terms of severe use application. It evades technical compromises that affect some of other products for these applications. In fact, the Hypercentric is a true 6D face-to-face dimension ball valve, which is produced in top entry forging design," Salah Elkadiki, CEO, AMPO Arabia tells OGN.
This extends by far the range of material selection with a direct consequence on the range of applications offered.
Thanks to the sealing performances granted by the triple offset seating configuration, the Hypercentric ball valve does not require a rising stem mechanism to disengage the ball from the seat.
Another added feature of the Hypercentric ball valve is that it can be operated by standard quarter-turn actuator with favourable torque characteristic, requiring high torque only near the fully closed position.
![]() |
AMPO headquarters in Idiazabal, Spain |
The torque seat characteristic allows the sealing required to be completely independent from the line pressure. Even in case of pressure drop, the sealing performances required is independently achieved.
Furthermore, thanks to the capacity to use conventional quarter-turn actuator and its trunnion mounted design, the Hypercentric ball valve can be installed in vertical or horizontal position, contributing to space saving in skids packages or in offshore installations, for example.
The full-bore design of the Hypercentric ball valve allows the use of pigs just like a conventional ball valve.
"One of the main points taken into consideration after the market research conducted was the repair and service characteristic of the products. "This aspect was highlighted by all operators who contributed to the survey," Elkadiki says.
Short turnaround or planned shutdowns and predictive maintenance operation require that critical equipment like valves can be serviced in the shortest time possible without the need of special tools; or, even worse, the need to move the valve to a nearby shop, which is not always possible especially when the products are installed in remote areas or simply too far from the nearest service shop.
![]() |
AMPO facilities in Idiazabal, Spain |
Elkadiki says: "The Hypercentric ball valve can be serviced in field. Standard maintenance routine previews the replacement of the sealing ring only. All other components such as stem packing or, in the worst case, the single seat, can also be easily replaced at site without any special tools."
He adds: "The only two non-standard components (sealing ring and seat) are fast-track produced items, which require minimum advance notice to be produced."
It can be said that such parts are considered as part of the standard commissioning and start-up recommended set of spares and, if not used, saved for any future need. The parts do not require special preservation conditions.
Thanks to its sealing design principle and to the wide range of material, the Hypercentric ball valve is a sound and cost-effective alternative to the existing range of products, and is suitable for highly contaminated media; high sulphur presence; molecular sieve, filtering; and black powder presence, just to name the most common ones.
The actual range of the Hypercentric ball valve cover sizes from 2 inches to 24 inches, in classes up to ANSI 1500, and the design codes meet the API 6D 24th Ed (design and quality requirements); ASME VIII-1 (pressure retaining parts); ASME B16.5 (flanges); NACE MR0175 / ISO 15156; Fire Safe API 6FA 4th ed; and IOGP JIP 33 – S-562 standards.
AMPO conducted the following tests on the Hypercentric Ball Valve:
• API 6D testing.
• HP Hydraulic and LP Gas Test.
• HP Gas Test.
• Annex H: Torque Functional Test.
• IOGP additional.
• Temperature Testing (HT test 800 deg F; LT test -20 deg F).
• PR1 cycling.
• PR2 cycling.
• PR2F test (API 6A Appendix F) Option: extended to 2,000 cycles (average cycles per year).
• Fire test API 6FA.
Elkadiki says the Hypercentric ball valve will be locally manufactured in the Kingom in the near future.
AMPO POYAM Valves, with its innovative attitude and technological capabilities, is committed since 1964 to the development of new fluid handling solutions, integrated smart solutions, technologies and systems for the most severe services and industries, covering applications in the oil and gas, petrochemicals, chemical, mining and power sectors.
With millions of valves installed in safe and reliable operation in the complete and global energy chain, the company develops custom solutions, working hand in hand with leading EPCs and end users, in order to offer optimum valve solutions and meet the most demanding requirements.
AMPO POYAM Valves is also committed to be wherever its customers are. With a wide sales network all around the globe, it also has state-of-the-art valve manufacturing and servicing facilities in its main headquarters in Spain, and also in India, Saudi Arabia, Kazakhstan and Nigeria.
Whereas AMPO India was established in 2010, AMPO Arabia in Dammam (KSA), AMPO Caspian in Aksai (Kazakhstan) and AMPO Nigeria in Oshogbo have been recently set up, meeting the growing industry localisation demand.
Consequently, AMPO is transferring global technology and knowhow to local markets, while is also able to positively impact in local delivery lead times and after-sales services to meet current and future projects demands of its customers.
"Hypercentric ball valve fits well in this localisation strategy, due to the design and product characteristics, which allow a considerable number of operations to be performed locally, increasing fast responsiveness and local capacity building," says Elkadiki.
Moreover, full maintenance and stock of key components are maintained by each branch, in order to provide customers with the excellent service standards for which AMPO is globally recognised.