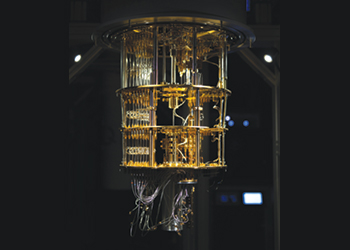
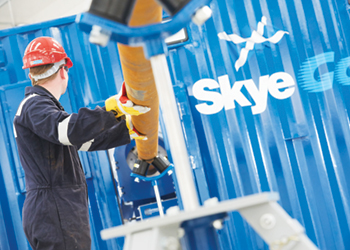
Duraband NC has shown consistently low friction against casing, causing around 50 per cent less damage than a tool joint with no hardbanding, Colin Duff, Global Director of Hardbanding Solutions, tells OGN
Hardbanding materials, applied by a welding process to the tool joints of the drill string, were primarily developed to provide protection from abrasive wear.
The drill string owners want their assets to achieve as many drilling hours as possible without being downgraded or scrapped for loss of wall thickness.
At the same time, preventing wear on casing caused by contact with the drill string is a priority for the operator, who traditionally owns the casing.
"Third party casing wear testing has evolved to give reassurance that both drill string and casing can be protected by the correct choice of hardbanding material," explains Colin Duff, Global Director of Hardbanding Solutions.
![]() |
Duff ... changing the way |
In decades past, when well profiles became more deviated resulting in more contact between the drill string and casing, there was a concern that a drill pipe tool joint might cause so much wear as to puncture the casing.
The first testing programme to investigate the potential damage to the casing was developed by a third-party laboratory in Texas, the USA, in the early 1990s. At that time the casing wear test was being referred to as ‘DEA 42’.
New hardbanding alloys such as Duraband NC® were created which would protect the tool joint from wear, whilst also having a low friction relationship when rotated against casing.
Previously, in more vertical wells, hardbanding was tungsten carbide dropped into a simple mild steel matrix.
While this application was effective at protecting tool joints from wear, it was extremely abrasive against casing, acting like a machining tool.
![]() |
Drill string rotates against casing |
In the initial test programme in which tool joints, new hardbanding materials and tungsten carbide overlay was tested, the results listed values such as ‘friction factor’ and ‘wear factor’.
To be approved as ‘casing-friendly’ hardbanding, the wear factor number had to be below a value of 2.0. A value above 2.0 was considered a failure.
The testing equipment was then sold to another laboratory. After some initial testing, the new engineers determined that the test results were inconsistent. This was due to the type of casing utilised in many of the tests.
The specification for the casing allowed for a wide range of material properties which added to the unreliability of comparable results.
In addition, the side load used in the test was not uniform or stable. So, several improvements were made to the equipment to improve repeatability of the results.
![]() |
Duraband NC applied on a pin tool joint |
Since these changes to the industry standard test, there is no longer a pass/fail result, but simply a set of values that are documented in the testing report. The friction factors and other results from one test cannot be compared to the other.
"I have been asked by oil and gas operators, concerned about wear on their casing, if there is any correlation between the old casing wear test and the current one. The answer is that there is simply no correlation between the test results. However, in various testing specifications with the improved equipment and procedure, Duraband NC has shown consistently low friction against casing, causing around 50 per cent less damage than a tool joint with no hardbanding. Tungsten carbide applications would destroy the casing sample before the conclusion of the test run,’ says Duff.
![]() |
Hardbanding being applied |
Other than casing wear test results, another consideration important to protecting casing is using a hardband material that is crack free.
If a hardband cracks, there is greater potential for it to ‘spall’ off in chunks downhole. Sharp pieces of very hard metal alloy can then get trapped between drill string and casing and cause significant damage.
This is one of the reasons Hardbanding Solutions’ priority with the development of Duraband NC was that it would be applied and reapplied 100 per cent crack free every time.
Finally, the type of mud used during drilling is influential on how much wear is seen on both the drill string (hardbanding) and the casing.
Oil-based or synthetic mud is known to reduce wear. As more organisations choose to switch to water-based mud due to the elevated cost of oil-based mud, they are noticing an increase in wear.
In the same casing wear test where other parameters are equal, we see a significant difference when the mud type is changed.
"Today, the only proven and effective guard against casing wear is to have proud, casing-friendly hardbanding such as Duraband NC applied to the tool joints and centre wear pads of the drill string," says Duff.
COMPARING TODAY’S CASING WEAR TEST RESULTS
There is more than one specification of test available with different parameters, and so it is important to look at the exact test conditions when comparing hardbanding products regarding casing wear.
There are several variables allowed by the test that must be considered when comparing results. These variables include:
• Type of mud (synthetic or water based) utilised for the test.
• Side load force (3,000lbs, 5,000lbs, or 7,000lbs),
• Type of casing used for the test (N80, T95, Q125).
Duraband NC is NS-1 approved for first application and reapplication over itself and various other materials.
It has been approved for use by almost all major global oil and gas production companies worldwide, including Saudi Aramco.
These operators recognise the importance of using casing friendly crack-free hardbanding to protect the drill string without causing damage to casing.