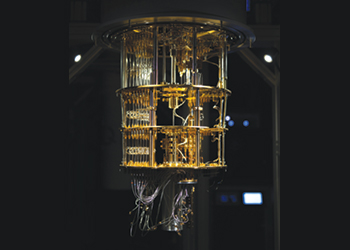
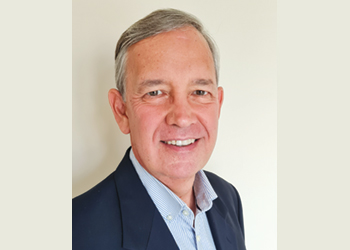
MSA Safety and its local partner for more than 30 years, Mohammed Hassan Sherbiny for Commerce (Sherbiny), supply gas detection systems to protect customers from dangerous gas leaks, including the highly toxic gas hydrogen sulphide (H2S).
Sherbiny, a leading provider of premium oil and gas equipment and solutions in Saudi Arabia now offers the General Monitors S5000 gas monitor from stock. This will help reduce delivery times, while also strengthening MSA’s technical support capacity and customer service.
![]() |
General Monitors S5000 with dual sensors and, below, the Observer-i UGLD |
As part of the country’s Vision 2030 initiative, Sherbiny established its Atheel manufacturing division, where in 2021 it began to assemble MSA gas detectors, including the S5000 with TruCal® H2S sensors.
'With the development of the state-of-the-art General Monitors S5000 gas monitor, it demonstrates MSA’s commitment to enhancing the level of safety for workers, who may be exposed to harmful toxic and combustible gases, including H2S. At the same time, the performance and self-diagnostics features of the smart sensor technology also help to lower the total cost of ownership for the user,' Ian Cameron, MSA Marketing Manager – Fixed Gas & Flame Detection for the Middle East, Africa, India, Russia and Caspian Region, tells OGN.
• The technology behind the new sensors: The S5000 gas monitor and its new advanced XCell® H2S sensor technology with TruCal, offers many benefits to the user, including:
• Enhanced levels of safety (gives a fault signal if gas cannot be detected).
• Multiple sensor status checks per day.
• Self-calibrations in the event of sensor drift due to changes in the environment.
• Extended manual gas calibrations from three months up to two years.
• Automatic monitoring on the sensor inlet for blockages.
• Improved levels of stability, measurement accuracy and overall performance.
• Longer sensor life, with new ionic non-consuming technology.
• Industry leading three-year sensor warranty for peace of mind.
• Dual sensor capability (lower capex and installation costs).
• Longer shelf life for the sensor (up to three years) reducing stocking costs.
• Remote sensor calibrations with the CalGard remote calibration adapter.
Today, the oil and gas industry best practice is to calibrate gas detectors that use electrochemical cells every 90 days.
Such calibrations are necessary to determine whether the traditional electrochemical sensors are functioning correctly and, therefore, are able to detect the target gas.
They also confirm the sensor’s inlet is not blocked and that gas can reach the electrochemical cell inside.
![]() |
'With traditional electrochemical H2S sensors, as well as the metal oxide semiconductor (MOS) H2S sensors, users only found out the sensor could not detect the gas leak when they manually applied test gas to the sensor,' says Cameron.
'This is the fundamental reason why frequent, labour-intensive, expensive servicing was required for these types of sensors. TruCal technology reduces this uncertainty as it performs a sensor self-check four times a day,' he adds.
TruCal technology is incorporated in MSA’s patented XCell H2S (and carbon dioxide) electrochemical sensors.
The pulse check within the sensor identifies if the sensor has drifted and corrects any changes in output sensitivity.
The pulse check uses MSA’s patented technology to calculate gas response by applying an electronic pulse to the sensor and analysing the response curve of the last manual gas calibration.
Through proprietary algorithms, MSA can quantify positive and negative drift that results in real-time accuracy adjustments (self-calibrations) during the pulse check.
![]() |
Senscient ELDS is an open path gas detector for H2S |
This technology is referred to as Adaptive Environmental Compensation (AEC) and occurs every six hours, which allows for manual gas calibrations to be extended up to two years.
The second part of Trucal is called Diffusion Supervision. 'In an industry-first, Diffusion Supervision monitors the sensor’s inlet for blockages, which would prevent gas from reaching the electrochemical cell inside,' says Cameron.
He explains: 'Should the inlet of traditional sensors become blocked, the sensor cannot identify this dangerous condition and, therefore, does not go into fault. This is one of the reasons why frequent manual gas calibrations are recommended.'
H2S sensors are one of the most expensive types of gas detectors to maintain and with some facilities having thousands of detectors, the cost of ownership is huge.
With the S5000 users can significantly reduce their annual maintenance budget. To estimate that users can use MSA Safety’s online cost of ownership calculator: https://webapps.msasafety.com/x5000-s5000-calculator-intl-usd/
ADDITIONAL LAYERS OF DETECTION
It is important to remember that no matter how good the H2S detector may be, it will not raise an alarm unless the gas reaches the sensor.
There could be various reasons for the gas cloud not to migrate to the sensor and the wind direction and its strength is usually the main factor.
To help increase the probability of detecting dangerous H2S gas leaks, which will further protect the people working in the hazardous areas, additional layers of detection are generally recommended.
An excellent solution here is an Open Path Gas Detector (OPGD) capable of detecting H2S gas leaks.
It offers coverage over a large area with the transmitter and receiver being capable of detecting H2S across a line-of-sight up to 60 m.
The Senscient Enhanced Laser Diode Spectroscopy (ELDS™) from MSA is a laser-based OPGD and designed to only detect one gas – H2S.
The H2S ELDS uses two lasers. This increases the reliability in detection and reduces the probability of false alarms, and provides the reassurance that when the ELDS sounds an alarm, it is detecting H2S and it’s not a false alarm.
Other benefits include:
• Factory-calibrated for life (no site calibrations).
• Auto self-test every 24 hours (lower cost of ownership).
• Both toxic and combustible gases can be measured in ppm metres (extra low concentration range enables earlier detection).
• Other ELDs units available for ammonia, hydrogen chloride, hydrogen fluoride, carbon dioxide, methane, ethylene and a sour gas option (H2S + CH4).
Another layer of detection that is often recommended for pressurised, high-risk applications, is the MSA Observer®-i Ultrasonic Gas Leak Detector (UGLD).
As a UGLD listens for the acoustic noise signature that a high-pressure gas leak produces and does not require the gas to reach the sensor, it can detect gas leaks at the speed of sound.
This gives additional valuable time to raise the alarm, monitor the gas detection system and take the correct course of action.
The MSA Observer-i is a third generation UGLD with a number of benefits over the earlier generations:
• Plug-and-play technology (no site visits for sound mapping surveys are required).
• Pre-trained to differentiate between gas leaks and sources of false alarms.
• Adapts to the environment and new noise levels (no follow up site visits required).
• Larger coverage area (fewer detectors required).
• More comprehensive auto self-test to ensure correct operation and lower cost of ownership.
'By designing a multilayered gas detection system, for any type of toxic or combustible gas, the people working in the hazardous area are further protected from life threatening gas leaks and the facilities, as well as the environment are also further protected,' Cameron concludes.