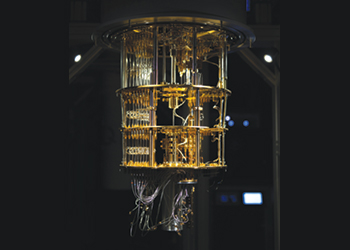
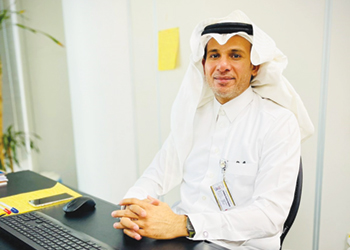
Realising the seriousness of worker safety, Total Safety Middle East is taking the business to a whole new level by introducing unique relevant technologies, localising core systems and manpower, and reinforcing leadership through the KSA office
As a global leader in safety, Total Safety has an uncompromising task when it comes to worker safety.
Through integrated safety solutions (SafeTek) and experienced specialised personnel (SSPs), the company is determined to protect mission critical equipment and valuable human lives.
In an exclusive interview with OGN energy magazine, Dr Hamad Almostaneer, who was recently appointed as General Manager, Total Safety Middle East, speaks about the importance of safety in the oil and gas industry, the challenges that still exist and how Total Safety is overcoming those challenges despite the rising demands in construction industry safety.
• What are some key safety hazards for workers in oil and gas?
There are quite a few key safety hazards, such as confined spaces, elevated work, and slips, trips, and falls, but the most critical one is confined space because this involves people going into very narrow places, which are not suitable for workers to stay in for a prolonged period.
But what makes them even hazardous is when there are hot activities like welding and chemical cleaning occurring in these spaces. Welding causes fumes, which put at risk workers if inhaled.
Total safety is a global leader in confined spaces through its SafeTek Smart Monitor™ technology, the Centralized Confined Space Monitoring (CCSM).
One of the most overlooked hazard is ‘slips, trips and falls’. These make up over 70 per cent of the industry’s accidents.
Total Safety will soon be introducing a new technology that rather than mitigating slips, trips and falls, which will prevent them from happening at all.
Additonially, toxic gases, such as hydrogen sulfide (H2S) and carbon monoxide (CO) still remain one of the leading hazards in the industry; inhaling of 10 ppm of H2S is the exposure limit of 8 hours per day and above which could kill a person.
Nitrogen oxides (NOx) is another group of very hazardous gases. Here too Total Safety is a leader when it comes to preventing and detecting these toxic gases in addition to lower explosive limit (LEL) of gases.
Our gas detection systems serve Saudi Aramco's Drilling and Workover (D&WO) Department and their top tier clients including Schlumberger, Halliburton, Nesr, Baker Hughes, Weatherford and many others.
Other significant hazards are explosions and fires. It’s a good thing that most companies, facilities and buildings have fire systems. But these systems may fail if they are not inspected periodically. We are fortunate that the Civil Defence in Saudi Arabia asks for the annual inspection certificate in which Total Safety recently became HCIS certified to provide such services.
• What are Total Safety’s recent campaigns with regard to workers’ safety?
![]() |
From left to right, Sara Alkhaldi (HR Manager), Muneer Abu Akbar (Sales Account |
Total Safety participates in key industry events. It was a participant at this year’s Global HSE conference in Muscat, Oman, in May; the Shutdowns, Turnarounds and Outages Technical Middle East Conference held in Dubai, UAE in May; the Project Execution Technology Conference (PETC) held by PMI-KSA chapter in collaboration Saudi Aramco PMT last December; and the iktva Forum and Exhibition, held in February this year at Dhahran Expo in Dammam.
These campaigns serve two purposes: To educate people and the industry about safety and how we can we help; and to promote our W3 brand.
• What are some instances where technology has played a major role in improving worker safety in the oil and gas industry?
It is Total Safety’s job to keep workers safe day in, day out, and there are daily instances where our technicians, engineers, supervisors and leaders are trying to improve people's safety.
But I have a few examples in particular to mention.
In a turnaround project in Jubail, where we have our SafeTek CCSM installed, the contractor was doing hot work in a reactor.
Our system engineer detected a fire on screen from underneath the bed where the workers were working, and immediately communicated it to the emergency response team, which rushed to the reactor and put off the fire before it caused any damage.
Usually these confined spaces are cleaned before the start of activities. However, reactors and columns can have chemicals remaining stuck to the walls that can be ignited by heat.
Our prompt response was greatly appreciated by the client and our team was rewarded.
In another instance at a major petrochemical plant in Jubail, catalyst was being loaded into a reactor.
The workers were not aware that the catalyst reacted with air, and that led to an increase in CO levels.
Our people behind the monitor at the CCSM spotted the CO buildup and raised an alarm. The emergency response team was called in immediately and everyone was evacuated.
Here too our team was appreciated by the company president and directors.
Today Total Safety has nearly a hundred sites across the region, including 62 active sites across Saudi Arabia alone. We have 26 active sites in Qatar and the UAE, and 3 in Bahrain.
We have 5 active In-Plant Service Center (IPSC) each in Vale (Oman), Sadara, Jubail, S-Chem, Jubail, SAMREF in Yanbu, Qatar Gas (QG), and GDS IPSC in SABIC-PK.
Amongst the many major companies, SABIC is a big believer in our technology. There is no SABIC plant turnaround (TAR) where Total Safety technology isn’t deployed.
Total Safety is also now in advanced talks with Aramco’s Riyadh refinery to install and utilise this technology.
We have people in other companies vouching for our technology to their management. And companies are consulting us to do turnarounds in a safe way.
Although Total Safety is focused on the upstream, we noticed that turnarounds and working with the petrochemical industry and the downstream is very important as well.
• What challenges do still exist with regard to worker safety in the industry?
The ‘restrictions’ posed by standards and procedures at legacy companies in the industry is an impediment in the adopting of new technology.
The younger companies on the other hand are more flexible to adopt technologies, which can improve their work and worker safety.
Another earlier situation, which is now changing, was the focus of safety only in oil, gas and petrochemicals in the Kingdom.
The government has now mandated that safety be introduced to non-oil sectors as well. These sectors will now have to adhere to safety standards and procedures, and have safety equipment.
So while, for example, the construction sector might not have to deal with toxic gases, it has other risks like working at heights.
Similarly, there are risks associated with the use of heavy equipment during road construction, corrosion of equipment in food plants, and even biological hazards in the pharmaceutical industry.
With Total Safety’s experience in multiple industries globally, we can transfer that knowhow to all sectors in the Kingdom.
• Share new developments at Total Safety?
We strongly believe in our Vision 2030, and thus understand that localising industry is important.
A recent development is our decision to register a manufacturing license.
Currently, we assemble our H2S gas detection systems in our Jubail factory using parts acquired from overseas and some locally. With a manufacturing licence, we will take it to a different level, and have the Saudi Made logo on our equipment.
Also, with regard to our CCSM systems, we get these from Europe. But with the system becoming a need in our industry, we decided to invest in 45 CCSM systems exclusively for Total Safety Middle East. We will be using our own systems now.
Furthermore, our manpower has also gone up, from 200 in 2020 to 246 employees.
Another proud announcement is the shifting of Total Safety’s regional headquarters to Saudi Arabia. So from our Al Khobar office, we will be leading all our branches in the UAE, Qatar, Oman, and Bahrain.
• What emerging technologies are you introducing into the Kingdom?
The first is our plan to soon introduce technology to prevent ‘slips, trips and falls’.
Another technology is an amazing ultrasound camera, which detects gas leaks by the specific sounds they emit.
Called Ultra Pro, it is made by Distran of Switzerland, and can detect gas from as far as 50 m just by pointing the camera towards a gas leak.
The camera shows the leak on the camera screen, and also identifies the location of the leak, the leak rate, and the type of gas.
It's state-of-the-art and even used by NASA to detect leaks in space shuttles.
We are also going to see newer versions of our time tested CCSM systems. In Version 4, more features will be added such as cameras not only monitoring workers working inside confined spaces but also checking if the worker is in fit condition and is not undergoing heat or work stress and fatigue.
This development is underway by our technology team in Europe and will soon see the light of day.
• How much have you achieved in the In-Kingdom Total Value Add (IKTVA) plan?
We have been part of IKTVA for almost four years now, and our score has always been above 80 per cent.
The formula for the high score includes three things: Our focus on Saudisation, planning and development, and our attempts to localised materials.
And with our intent to register as a local company, this will further increase our IKTVA score.
• What major projects are you executing in Saudi Arabia?
We execute numerous projects in Saudi Arabia, with sometimes more than 10 turnaround projects (TARs and T&Is) in a good year.
SABIC is our key partner. Other clients include S-Chem (Chevron Phillips), Sadara, Samref, Luberef, Tasnee, Alfarabi, Advanced Petrochemicals, Yansab, and Khafji Joint Operations (KJO).
With Saudi Aramco's D&WO we have a contract to provide our H2s perimeter packages for rigs.
We aren’t afraid of competition because neither do our competitors have the portfolio of technologies we have, nor our global strength.
• What is Total Safety’s strategy to develop the capabilities of Saudi engineers and technicians?
Total Safety currently has 260 employees, or heroes as we call them, because they are doing a fascinating job saving lives. Almost 80 are local (30 per cent Saudisation), and our goal is to reach 40 per cent by 2023-end.
To support the hiring and training of local workforce, we collaborate with different government programmes. Through these programmes, we have been able to hire more than 60 Saudis.
When I joined Total Safety Arabia, we had no engineers registered with the Saudi Council of Engineers (SEC). Now we have eight in addition to a good mix of technicians.
We also had no job description for safety engineers at the company. So we wrote that job description, got it approved from our corporate headquarters, and then hired Saudis as 'safety engineers'.
In the coming weeks, one of our Saudi engineers will be undergoing training in Europe for the CCSM system, including how to get the technology assembled and manufactured in Saudi Arabia.
We have a state-of-the-art training centre in Jubail, where new Saudis undergo a practical and virtual training for two to three months, followed by on-the-job training for another month or two.
• As an industry leader, what’s your take on the Kingdom’s energy transition plan?
Let me tell you about electric vehicle maker Lucid, which will be building its first factory outside the US in Saudi Arabia, in Riyadh.
We were approached by Lucid asking us if we could provide systems for its plant here.
They know about our systems, technologies, and services that we are providing to both Lucid and Tesla’s plants in the US. So considering our experience, we can transfer our Lucid US model to Lucid here in KSA.
We hope to be their partners and extend our global partnership and be able to provide services to Lucid in KSA as we are already partners in the US.
We will continue to follow the 2030 vision as we are proud of it, we believe in it, and we know that together we can achieve.