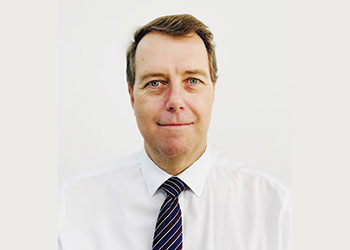
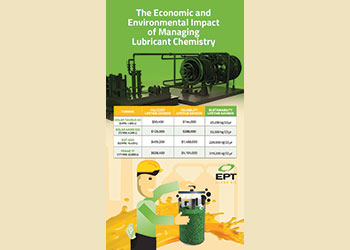
This simple approach of oil maintenance provides the users of critical industrial equipment with a blueprint to operate sustainably, and supports the global goal of net-zero by 2050, Matthew Hobbs, Manager, Technical Services, Research and Development, EPT Clean Oil, tells OGN
During the 1970s, burgeoning conservation efforts gave rise to the three Rs: Reduce, Reuse, and Recycle. This environmental mantra became pervasive and, in light of the present drive towards sustainability, is more important than ever today.
Indeed, sustainability is a 21st-century operational tenet that goes well beyond environmentalism; it needs to be a driving force at the centre of all of our operations.
In the energy sector, the current rates at which CO2 is being emitted are not sustainable.
Globally, it's estimated that 76 per cent of greenhouse gas emissions are energy-related, with power generation accounting for a third of that.
'For net-zero 2050 to be achievable, we will need to cut emissions everywhere we can including the way that we manage lubricants. This brings us to a new three Rs, the three Rs of oil management: Rethink, Remove, and Restore,' Matthew Hobbs, Manager, Technical Services, Research and Development, EPT Clean Oil, tells OGN.
RETHINK
![]() |
An end-user benefited from improved reliability and experienced zero |
We need to rethink business as usual, starting with rethinking assets. Typically, turbines are regarded as assets and the oils within them as consumables. But it's not just about the machine; oils are assets too and they need to be maintained sustainably.
Poor oil maintenance leads to lubricant waste, equipment failures and lost production, which are economically and environmentally costly.
Currently, 95 per cent of oil maintenance focuses on removing particles and water, which keeps the oil clean and dry. These important efforts, however, neglect the impact of chemical breakdown.
Oil oxidation produces acids and varnish, limiting typical oil lifespans to 2–5 years. Given that turbines have a 25-year lifespan, that means that most operators will need to change their oil, at least, five times.
Unfortunately, lubricant manufacturing is the most energy-intensive process in a crude oil refinery.
As a result, lube oils have a significant carbon footprint, with every litre produced resulting in 3.5 kg of CO2 emissions. This highlights an obvious opportunity for emissions reduction.
By improving oil maintenance to address chemical breakdown, oil lifetimes can be extended and reductions in overall emissions can be achieved.
To do this, we need to rethink oil maintenance. It’s not enough to remove dirt and water; if we want to treat our oils like assets, we need to remove oil breakdown products as they form.
This novel approach, lubricant chemistry management, will allow energy producers to operate much more sustainably.
Case study: Patented ion-exchange ICB™ filters were used to manage oil chemistry on a gas plant compressor driver from its first day of operations.
This plant has now been operating at baseload for 13 years. During this time, ICB effectively managed the oil's chemistry, removing breakdown products as they formed so that varnish could not accumulate or cause problems.
Indeed, this plant's MPC varnish potential has been maintained at near-zero levels. As a result, the end-user benefited from improved reliability and experienced zero oil-related failures.
Most importantly, the plant’s operators have never had to replace their carbon-intensive lubricant since they took the simple step of rethinking their oil maintenance by managing its chemistry. In fact, this oil will probably last longer than the compressor driver that it’s used in!
REMOVE
According to ASTM D4378, oils are condemned due to chemical breakdown, which leads to varnish and acid accumulation.
Since oil life extension allows for more sustainable operation, the removal of these breakdown products is an obvious maintenance goal which also enhances equipment reliability.
The best way to deal with a varnish problem is not to have to.
Case study: An operator experienced a turbine trip. Subsequent oil analysis confirmed that their oil’s MPC varnish potential was critical and that varnish caused their failure.
Hoping to avoid a recurrence, an SVR™ lubricant conditioning skid using patented ion-exchange ICB filters was installed.
This removed varnish, resulting in a dramatic 94 per cent MPC reduction.
The unit hasn’t tripped since. Moreover, this oil charge (which would have been condemned otherwise) was salvaged resulting in significant carbon savings.
RESTORE
![]() |
Patented ion-exchange ICB filters can help manage oil chemistry on a gas plant |
In a recent poll of gas turbine users, one in five reported that they lost production in the past year due to an oil-related problem; varnish was, by far, the most common.
This lost production is both economically and environmentally costly. For example, 24 hours of unplanned downtime will not only cost a Frame 7F operator about $160,000 in lost revenue but it will also negatively impact sustainability.
When a turbine trips, it needs to be started again. Since start-up emissions are greater than baseload emissions, there is a significant environmental cost to every avoidable failure.
By rethinking oil maintenance and removing varnish through lubricant chemistry management, you can restore your equipment’s reliability and efficiency, allowing for more sustainable operation.
Case study: After varnish plated out within cooler internals, a gas turbine started to run hot. As the bearing temperature rose, the unit’s high-temperature alarm went off.
To silence the alarm, engineers had a creative solution; they derated the turbine by 40 per cent. This impacted their bottom line, costing the operator $350,000 in lost generating revenue annually but it also had an environmental cost.
Gas turbines operate most efficiently at baseload (100 per cent). When the turbine was derated by 40 per cent, its efficiency dropped by 12 per cent. The turbine burned more fuel to produce less power which is, of course, unsustainable.
Following the installation of an SVR lubricant conditioning system, backed by patented ICB ion-exchange technology, the turbine oil’s varnish potential dropped by 97 per cent.
As a result, varnish was removed from the cooler and the bearing temperature came down to nominal.
This allowed the end-user to return to operating at full design capacity, and they saved the charge of oil that was in their reservoir while simultaneously improving their operation’s environmental impact.
CONCLUSION
The three Rs of oil maintenance provide the users of critical industrial equipment with a blueprint to operate sustainably.
By rethinking oil maintenance programmes and removing oil breakdown products through effective lubricant chemistry management, end-users can restore profitability, reliability and efficiency.
Because the energy sector is responsible for 76 per cent of CO2 emissions, these simple changes can have a big global impact — Rethink, Remove, and Restore.