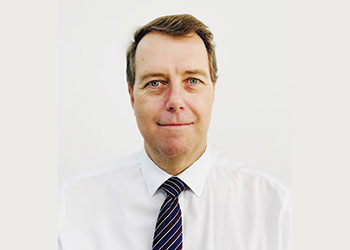
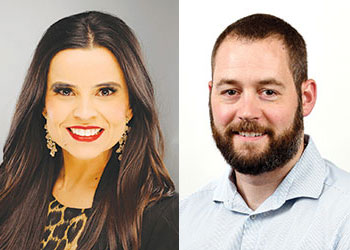
Continuous application of multi-functional chemistry containing the FeS dissolver eliminates the need for system shutdowns to clean tank level monitors and reduces the frequency for filter changing, Ana Ferrer and Brian Bennett, tell OGN
The formation and build-up of iron sulphide (FeS) and other inorganic scale can cause plugging, corrosion, flow restriction and emulsions, ultimately leading to production loss.
Finding efficient ways to handle this issue has been an inherent challenge for the oil and gas industry.
While chemical scale inhibitors have traditionally been used for remediation, they can be corrosive, which could potentially lead to a variety of additional problems, such as hydrogen sulphide generation.
ChampionX Corporation, a global leader in chemistry solutions and highly engineered equipment and technologies that help companies drill for and produce oil and gas safely and efficiently, developed a multi-functional portfolio of chemistries that act as cleaners, corrosion inhibitors, Fes dissolvers and scale inhibitors in one, combined solution.
With very low corrosivity, even in neat form, the novel remediation treatment has proven its effectiveness in the laboratory and across several field applications, including saltwater disposal (SWD) operations.
INNOVATIVE, VERSATILE CHEMISTRY
![]() |
Figure 1 .. facility diagram outlining pre-treatment issues |
Costly mechanical methods can be used to remove scale deposition from a system.
However, in some systems, restricted accessibility and pigging capability can hamper this approach.
Chemical remediation is, therefore, a lower-cost option and incurs less downtime and risk to personnel.
A common oilfield biocide, Tetrakishydroxymethylphosphonium sulfate (THPS), is known to remove FeS scale from oil and gas wells.
While it is effective at dissolving FeS by chelation, there can be challenges related to low pH, especially if the injection system is made from carbon steel.
While THPS can be detrimental to the injection system, once it is injected, it is not usually harmful to production equipment due to its dilution with the production fluids.
In addition, THPS may not be as effective in the presence of other inorganic scale, such as calcite and barite.
Specific inorganic scale inhibitors must then be employed to remediate those types of deposition.
In developing the multi-functional chemistry, the primary goal of ChampionX researchers was to determine if an alternative FeS-dissolving active could be identified that had equivalent – or better – performance to THPS but did not pose corrosivity issues with carbon steel.
![]() |
Figure 2 ... solid scale build-up on the probe |
The following tests were performed to understand the potential chemistries’ FeS dissolution, corrosivity, corrosion inhibition and scale inhibition performance: Static bottle testing; FeS dissolution test; corrosivity and corrosion inhibition studies; and scale inhibition testing.
A full analysis of the procedures and the results across each test scenario are detailed in the Society of Petroleum Engineers (SPE) paper, IPTC-22249-MS.
In summary, the testing showed that a non-THPS active alternative was more compatible with carbon steel than THPS.
FeS dissolution testing showed it performed better than THPS at dissolving FeS once the FeS was precipitated in solution.
Further studies revealed that when coupled with a scale inhibitor, whether for calcite or barite inhibition, the multi-functional chemistries performed well in a series of laboratory tests, including linear polarisation resistance (LPR) bubble cells for corrosion inhibition and dynamic scale loop (DSL) testing for scaling tendency.
Further testing would be required to determine the stoichiometry ratio between the chelating agents (THPS versus new FeS dissolver) and the Fes.
FIELD EVALUATION
![]() |
Figure 3 ... solid analysis results from scale collected at multiple facilities |
As proven in laboratory tests, a single, multi-functional product can remediate Fes deposition, inhibit scale formation, and minimise corrosion.
This novel chemistry was used by a major public operator to remediate scale and solids deposition during saltwater disposal (SWD) in the Midland and Delaware Basins.
Operational challenges included tank-level monitor fouling, filter fouling and downtime related to mechanical removal of solid deposits.
The operator, who had relied on minimising solids build-up to maintain safe and economical produced water injection and disposal, was experiencing scale precipitation on the tank level monitoring probes at six of their saltwater injection facilities, causing major system issues (Figure 1).
The most expensive and time-consuming problem was the rate at which the tank-level monitors were failing. Once they failed, the system had to be shut down for manual cleaning.
Scale build-up was severe enough to require expensive mechanical removal every three to four weeks.
In addition, the filter pods located before the high-pressure injection pumps had to be cleaned frequently.
Solids collected from the probes were a combination of carbonate and FeS scale with varying levels of organic proportions (Figures 2 and 3).
While carbonate scaling tendencies from water analysis on the inlet were low, due to the large volume of water traveling through each facility, major scaling issues were still observed.
Water collected from the inlet to the facility was dark grey and had low transmittance.
A treatment upstream of the SWD with one of the novel, multi-functional chemistries at a continuous dose rate of 35 ppm was proposed with an additional treatment at the inlet.
![]() |
Figure 4 ... summary of field observations and water samples from SWD tanks |
This formulation was also recommended as a standalone treatment at 25 ppm on the lines feeding the smaller facilities.
Over a four-month period, careful field observations were made to determine if the new treatment program was working.
A visible reduction in turbidity and opaqueness of the water in the tanks (Figure 4) was evident.
Since the application of the multi-functional product, the tank level monitors did not fail due to FeS and calcite scaling.
Notably, significant variability in the water sent to public SWDs can make treatment validation difficult with varying throughput and total filtered solids data.
A further complication arises from the fact that performing FeS performance testing in the field is difficult due to the presence of oxygen once the sample is collected.
To prove product and program performance analytically, both soluble and insoluble iron measurements were taken.
Total and filtered iron were tracked during this new chemical application.
Average soluble and insoluble iron collected at the largest SWD facility clearly showed an increasing trend in soluble iron as well as an overall decrease in the insoluble iron compared to the untreated sample.
The recommended treatment of the multi-functional formulation in this SWD application was a success and provided:
• Safer, more effective daily operations.
• Unfailing tank level probes since the application was started.
• Significantly improved water quality.
• Reduced facility downtime by not having to clean tank probes
• Calculated average reduction of 5,600 lbs (2,540 kg) of insoluble iron per year.
CONCLUSIONS
Through comprehensive laboratory investigations, ChampionX developed an alternative multi-functional product, which could effectively dissolve FeS better than THPS and counter corrosion issues when in contact with carbon steel.
The performance was then verified in a SWD application where there was visible solid deposition from produced water going into the system.
This had caused the tank-level monitoring probes to fail, necessitating regular, full system shutdowns for manual cleaning.
Continuous application of the multi-functional chemistry containing the novel, non-corrosive FeS dissolver eliminated the need for system shutdowns to clean the tank level monitors and reduced the frequency for filter changing.
The water quality visibly improved, becoming clear and transparent.
The soluble iron trends were reversed after the product was applied, indicating FeS was being dissolved.
Overall, the method used to identify a multi-functional product to address FeS and calcite scale was successful.
REFERENCES
• Wylde, J J, Okocha, C, Smith, R, Mahmoudkhani, A, Kelly, C J, 2016. Dissolution of Sulfide Scale: A Step Change with a Novel, High Performance, Non-Mineral Acid Chemical. SPE International Oilfield Scale Conference and Exhibition, Aberdeen, Scotland, UK. SPE-179880-MS
• Chen T, Wang Q, Chang F, Aljeaban N, 2019. Recent Development and Remaining Challenges of Iron Sulfide Scale Mitigation in Sour Gas Wells. International Petroleum Technology Conference, IPTC-19315-MS.
Ana Ferrer, PhD, is RD&E Program Leader at ChampionX. She has seven years of experience working in the oil and gas chemicals industry and has extensive knowledge of corrosion management, with a specific focus on developing corrosion inhibitor test methods and products.
Brian Bennett, RD&E Group Leader at ChampionX, has worked in the oil and gas sector for 14 years. He has developed many corrosion inhibitor products, including corrosion inhibitors for deployment in Arctic regions and in high temperature applications.