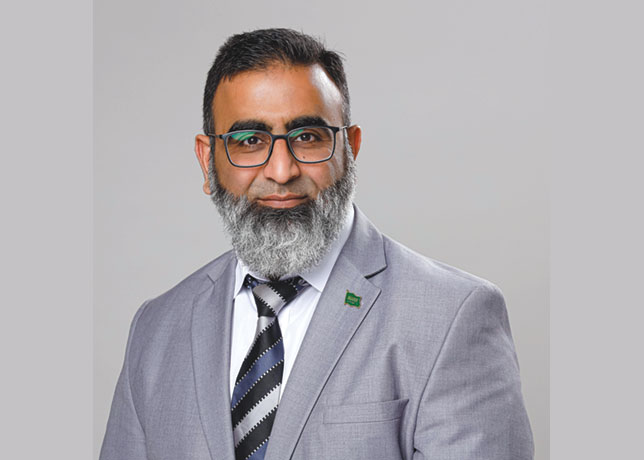
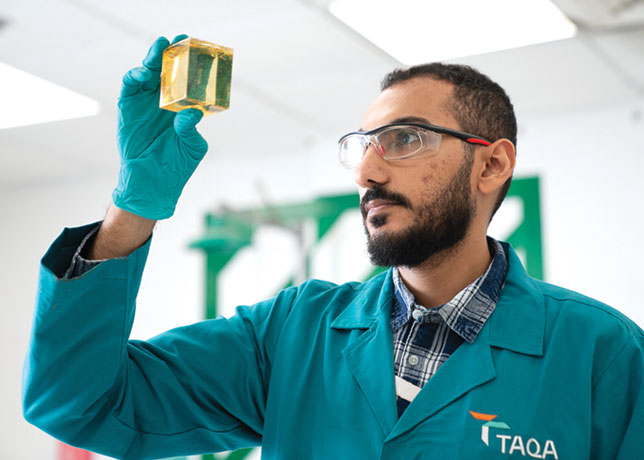
Optimising sealant material and precise placement can improve the efficiency of cement squeezing, overcoming traditional difficulties and high costs associated with complex, low-success-rate slurries, say TAQA experts
Workover is a critical operation in the oil and gas industry, serving a distinct purpose to optimise the well performance. Globally, millions of dollars are spent on workover operations each year.
Typical workover may include tasks such as repairing damaged equipment or a leak, sustained casing pressure (SCP), cleaning out the wellbore, stimulating the well to improve flow, or even replacing the completion.
Workover operations are essential for maintaining the productivity and endurance of oil and gas wells.
Squeeze cementing falls under such workover activity which is used to repair the tubular leaks as well as to remediate the SCP.
Wajid Ali, Raid Bukhamseen, Faisal Abdullah Al-Turki, and Mouloud Bouaraki explored the best industry practices to improve the squeeze job efficiency by proper selection of sealant material and accurate placement of the treatment.
During the squeeze operation, the cement is forced through perforations in casing/tubing, cement cavities (Figure 1) and/or between the cement and the surrounding environment in order to create a dependable barrier.
Many materials can be used to seal; however, the success ratio is extremely low for solid laden materials if it is attempted in low injectivity conditions.
![]() |
Figure 1 ... cement failure with cracks in the cement sheath Source: https://www.pvisoftware.com/white-paper/Common-Well-Cementing-Problems-and-Solutions.pdf |
While the advancement of the oil and gas industry led to having many options available for the successful placement of squeeze jobs in a normal injectivity environment, the low injectivity conditions significantly limit the available options and introduce a major challenge creating the need for a completely new solution.
WHY IS SQUEEZE OPERATION REQUIRED AT OILFIELD WELLS?
Assurance of well integrity is critical and important throughout the entire well's lifecycle. Any leak in well’s tubular can undermine the production potential of the well and become a serious health, safety and environment (HSE) risk.
Apart from the leak, the pressure build-up between cemented casings annuli, also known as SCP, has been a major challenge all around the world that mainly occurs due to a compromise of cement sheath integrity.
This compromise allows the fluids to migrate through micro-channels from the formation all the way to the surface. These channels are usually too tight to inject any particle-laden fluids.
![]() |
Figure 2 ... an ARC Resin cured sample |
Generally, microfine cement systems with proprietary formulations are squeezed to repair the leaks and microchannels.
However, these systems are often ineffective in sealing the leak or channels because of the high concentration of solids present within these systems.
This challenge prompted the cementing technologists at TAQA to explore new cementing solutions, to achieve reliable long-term zonal isolation in these extremely tight injectivity conditions.
FLUID SELECTION METHODOLOGY
Tubular leaks and micro-annular gaps as narrow as a few microns can allow gas leakage depending upon the differential pressure.
The flow paths that allow for the wellbore fluid influx may be present at either the pipe/cement or cement/formation interfaces.
In order to penetrate and seal such narrow gaps, a specialised sealant was required with a superior tendency to penetrate deeper and eventually deliver a dependable barrier.
As a result of collaboration between the operator and TAQA, an epoxy resin (named ARC Resin) was developed which could penetrate through these microcracks due to its solid-free nature while providing excellent bonding properties.
SOLUTION
ARC Resin (Figure 2) is preferred to repair the tight leaks and SCP by injecting the resin directly into the leak or microchannel.
The resin system is a compound that begins in a viscous (liquid) state and hardens with temperature and/or time.
![]() |
Table 1 |
It comprises epoxy resin that crosslinks when a crosslinker is introduced into the system (Table 1).
A reactive diluent is used to adjust the viscosity of the final mixture in order to achieve the deepest possible penetration.
It gives a predictable and controllable pumping time, ranging from a few minutes to several hours at over a wide range of temperatures.
The density of the base resin ranges from 66-69 lbm/cu ft. The density can be adjusted based on the requirement by adding lightweight additives or weighing agents. It consists of three major components.
The mechanical properties of this product can be tailored to meet a variety of wellbore challenges.
The resin system can withstand impurities in the wellbore and achieve a set state with high bond strength. The resin can effectively fill the cracks and defects on the cement surface, improving the wellbore annulus’s tightness and strength.
The carefully timed setting of resin ensures optimum penetration and placement before the resin cures up and ensures the leak or flow path is permanently sealed.
The cured resin has the ability to achieve exceptional shear bonding with both formation and casing due to the superior strength and chemical resistance observed during experimental and field operation (Weinmann 2004; Eoff et al. 2001).
Resin also provides highly desirable properties in terms of performance issues and cost in some cases.
VALUE ADDITION TO CUSTOMERS
Well integrity is a critical compliance requirement during oil and gas drilling operations.
The use of resin to repair microchannels exhibited a higher success rate and improved reliability in comparison with the conventional particles-laden fluids, which helped to decrease costs associated with additional remedial treatments.
The novel technology that TAQA has introduced allowed the operators to overcome a unique set of challenges while staying on schedule and under budget.
REFERENCES
1- SPE 19061: Innovative Epoxy Resin Formulation by Khawlah Alanqari, Abdullah Al-Yami, Vikrant Wagle, and Mohammed Al-Jubran, Saudi Aramco.
2- SPE 195873: Lessons Learned from Casing-Casing Annulus Repair Utilizing Rigless Operation Approach in Offshore Oil Field by Abdullah Al-Dhafeeri, Saudi Aramco; Sultan Al-Aklubi and Shebl Abo Zkery, Al-Khafji Joint Operations.
3- SPE 196503: Applying Epoxy Resin Technology on Remediation for 3.5 in. Casing Leak: Case Study, South Sulige Gas Field by Yufei Sun, Anyu Fang, Wenmin Fan, Zhiyong Chen, and Sheming Liu, PetroChina; Yang Wang, Li Li, and Xiaoming Zhang, Halliburton; Chunlong Luo, CentReal.
4- SPE 21953: Resin Systems as Evolving Solution Within the Industry to Replace the Conventional Remedial Cementing while Eliminating the Sustained Casing Pressure SCP by Wajid Ali, Faisal Abdullah Al-Turki, and Athman Abbas, TAQA: Abdullah Saleh Al-Yami, Vikrant Wagle, and Abdullateef Ahmed Dahmoush, Saudi Aramco.
5- White Paper: Common Well Cementing Problems and Solutions by Gunnar DeBruijn
6- Weinmann, Daniel. (2004). New Epoxy Resin Technologies to Meet Tough Demands of Offshore Platform Coatings. Paper presented at the CORROSION 2004, New Orleans, Louisiana, March 2004.
7- Eoff, Larry & Dalrymple, E. & Reddy, Bobba & Everett, Don. (2001). Structure and Process Optimization for the Use of a Polymeric Relative-Permeability Modifier in Conformance Control. 10.2523/64985-MS.