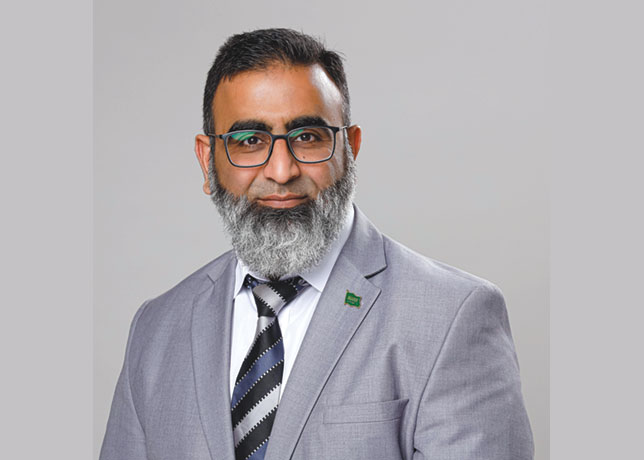
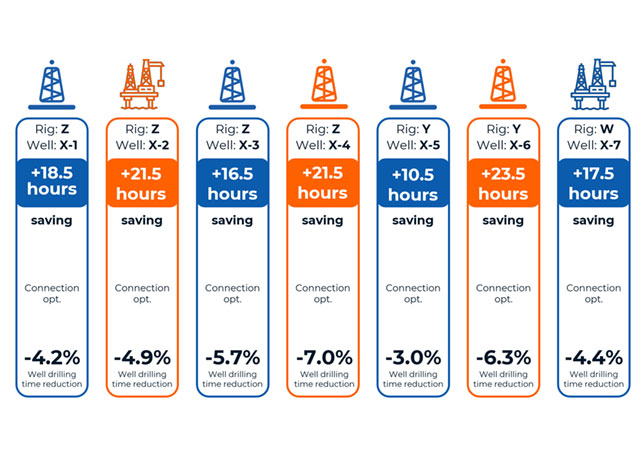
WellsX ECO’s digital twin optimises wellbore cleanout, reduces reaming, and enhances connection practices with real-time insights and automated benchmarking for improved drilling efficiency and decision-making
The WellsX ECO digital system, equipped with a dynamic digital twin, helps mitigate complications related to wellbore cleanout, stuck pipe, and wellbore instability.
It also aids in selecting best practices for eliminating these complications.
A set of engineering tools combined in one system with the dynamic digital twin allows to select and implement best connection practices and reduce wellbore reaming time.
Usually, it is required to perform several wellbore reamings before the connection, according to the drilling programme. But it is not always mandatory to perform more than one wellbore reaming before the connection.
DEFINING THE NEED TO PERFORM EXTRA WELLBORE REAMING
While performing wellbore reaming operations (with and without RPMs) before connection, the digital twin calculates T&D and hydraulics in real-time and compares calculated values against sensors readings.
In case of deviation, the system notifies all participants about the violated technological parameter. The following parameters are calculated and visualised on the main real-time drilling plot next to sensors readings: hook load, surface torque, SPP, ECD. In the meantime, hook load and surface torque sensor readings are plotted on T&D broomstick, displaying FFs trend.
T&D broomstick recalculates automatically based on actual trajectory, fluid parameters, and BHA. These tools provide a complete picture of wellbore conditions while well construction is in process.
DEFINE NEW PIPE CONNECTION PRACTICE EFFICIENCY
The ecosystem has implemented algorithms of automatic technological activity recognition based on sensor readings data.
The system recognises the activity set while pipe connection after the stand is drilled down and calculates weight-weight time.
User sets connection time standards for each section, then the system calculates deterioration and improvement time.
Thus, engineers can analyse connections practice efficiency in real-time and compare pipe connection time between wells and sections.
CORRECT WELLBORE TREATMENT PROCEDURES AND CONTINUOUS REAL-TIME IMPROVEMENTS
Implementation of a digital ecosystem for the remote drilling monitoring process (RTOC) opened an area for drilling practices improvement and optimisation without compromising technology aspects.
The focus was directed on instantaneous ROP as well as connection practice improvement, predominantly on pre-connection (weight–slip) and post-connection practice (slip-weight), while the connection itself (slip-slip) were not in the optimisation plan considering that they are performed manually and that optimisation of it could increase HSE risk.
The post-well analysis of available data led to the conclusion that connection practice differed from rig to rig, driller to driller, and that a uniform approach was lacking.
In general, traditionally applied weight-slip connection practice considered working stand three to four times up and down with rotation and circulation after drilling stand down regardless of whether the wellbore conditions dictated so or not. Then, MWD surveys were taken, followed by a slip-slip connection. The pre-connection time (weight-slip), while drilling, consumed 25-30 min/connection on average.
The post-connection time (slip-weight) was spending 8-10 min/connection and included the required time to establish drilling parameters after the connection and to pump sweep as per the drilling program schedule.
The reason behind this conservative approach in connection practice lay in tradition and was justified by the avoidance of bad hole cleaning and stuck pipe scenario without any positive indications.
The optimisation measures were related to increasing instantaneous ROP, reducing the number of working stand up and down at pre-connection, changing the frequency of MWD surveys, and pumping sweeps using the on-fly method.
Applied measures in drilling practice were supported by monitoring the well condition via ecosystem solution, making sure no worsening wellbore condition nor an indication of hole cleaning issues. Digital twin was giving an excellent clue with the frequency of 1 HZ of what the drilling parameters were expected to be, while the smart alarm system was alerting RTOC engineers timely.
Therefore, planned optimisation was successfully put in place while non-productive time has not been induced.
The optimised measures were implemented and established as a standard procedure, observing the significant time reduction effects (Figure1).
The successful implementation of the digital ecosystem with a live digital twin ensured high data quality and allowed to optimise drilling, tripping and wellbore treatment practices.
One of the main benefits achieved is a significant reduction in well construction time, optimising weight-to-weight and drilling time.
The current downhole state of a well is evaluated each second on the edge device and in real-time by a digital twin, and a suite of optimisation build-in features serves as a firm foundation for real-time decision-making in the field and RTOC.
The automated digital platform provided a real-time benchmarking of currently and historically drilled comparative wells, utilised drilling technology applications, ensuring contractors' compliance with the best-recommended practices, aggregated and evaluated in real time the efficiency of a current set of recommendations to continuously augment and improve the knowledge set.
The system deployed on a client’s premises and a dedicated edge compute IIOT device on each location allowed to automatically evaluate wellbore conditions in real-time and manage the effectiveness of activities performed downhole.
Realtime data augmented by dynamic digital twin insights of the downhole process deliberately serves as a ground for real-time decision making, advising when additional wellbore treatment procedures are necessary, hence continuously improving best practices implementation.
The method described above is just one part of the continuous cycle of well construction improvements the client has achieved using a unified digital drilling system.
This approach, which we may called a Smart Real-Time Operations Center (RTOC), integrates well design, real-time support, and performance analysis into a single systematic framework.
This allows the client to effectively leverage analytical data, facilitating strategic planning and optimizing decision-making for future operations.
By implementing this systematic approach, the client has elevated their RTOC operations to a new level, achieving several fundamental improvements:
• Accident reduction: The use of the digital ecosystem and RTOC has significantly reduced accidents during drilling operations, enhancing the safety of both personnel and equipment.
• Non-productive time reduction: The digital ecosystem and RTOC have led to a substantial reduction in non-productive time, resulting in more efficient operations and cost savings for the company.
• 24/7 operations control: The in-house RTOC provides continuous monitoring, ensuring that any issues or anomalies can be promptly addressed, regardless of the time of day.
• Continuous improvement: Each new well benefits from the structured use of past drilling experiences, fostering a constant cycle of improvement.
After implementing the (RTOC) approach in-house, the client achieved notable improvements in well construction efficiency, as confirmed by internal statistics.
Based on these successful outcomes, the client management decided to launch a new line of business: remote RTOC services.
This strategic move allowed the company to successfully enter new markets and significantly enhance overall profitability.