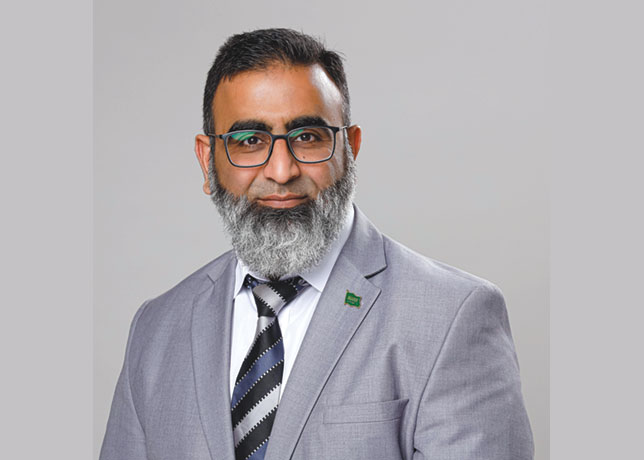
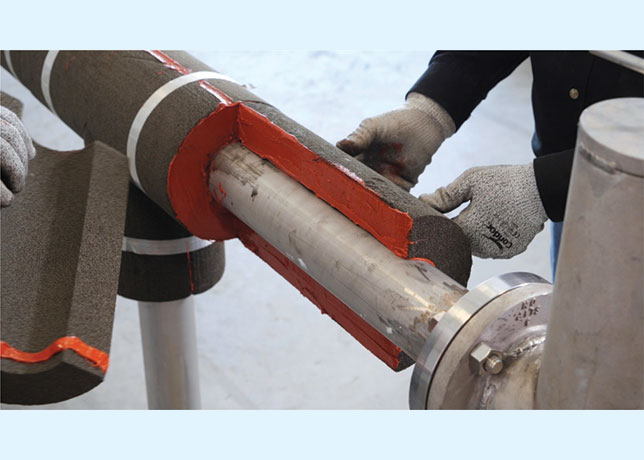
A new study finds FOAMGLAS® sealed system to significantly reduce corrosion under insulation in petrochemical pipes, addressing multi-billion-dollar industry challenge
Corrosion and corrosion under insulation (CUI) are multi-billion-dollar problems that affect the oil and gas industry worldwide.
Piping and equipment that process or carry water, steam, gas, and petrochemicals must perform reliably under harsh industrial and environmental conditions.
Despite many options for wrapping, insulating and protecting these vital pieces of infrastructure, pipes and equipment are constantly vulnerable to corrosion.
Beneath these layers of protection, corrosion can advance, often undetected.
When CUI takes hold, it compromises not only the piping and equipment systems, but also the productivity of processes and the safety of facility personnel.
HOW DOES CUI HAPPEN?
CUI is a common problem for insulated pipes in almost any industry. However, the ideal conditions for developing CUI often characterise gas and petrochemical processing environments.
The presence of heat, humidity, chemical agents and certain weather conditions contribute to CUI that can develop more quickly and cause more damage.
CUI can occur when moisture infiltrates the insulation system. It is typically fed by four factors: water, oxygen, a corrosive chemical, and the right temperature conditions.
![]() |
CUI is a common problem for insulated pipes |
Moisture under insulation is difficult to detect, and may sit in contact with a pipe for a long period of time, causing corrosion to go completely unnoticed until a pipe begins to leak or fails entirely.
All corrosion begins with moisture, which is everywhere and unavoidable. Some of the main moisture sources and risk factors to watch for include:
• Rainwater/environmental moisture: Rainwater or moisture condensed in the air can by itself can be corrosive. As this moisture contacts pipe jackets and sealants, or picks up other environmental elements, it can take on more corrosive characteristics.
• Sprinkler systems: When these systems are activated, they can often introduce vast amounts of water to a small area, potentially soaking insulation.
• Power washing: Regular maintenance procedures could introduce corrosion risks through water and/or cleaning agents.
• Cold temperatures: Pipes operating at temperatures well below freezing tend to be at low risk for corrosion (because of the lack of oxygen), but pipes (or sections) that frequently experience freezing and melting below their insulation are particularly vulnerable to corrosion.
• Warmer temperatures: -4-175 deg C is prime corrosion risk temperature range for most metal pipes. These temperatures are not quite hot enough to evaporate all moisture, allowing permeable insulation to potentially become waterlogged and in constant contact with the pipe.
• High-temperature systems at rest: When pipes are carrying high-temperature substances, corrosion risk is lower because of evaporation. But when these systems are shut down, moisture can set in and so can corrosion.
WATER PLUS CHEMISTRY: CREATING A MORE CORROSIVE MIXTURE
The moisture that kicks off corrosion may be simple water condensation or rainwater for example.
But often that water comes into contact with other substances that change its chemical composition.
As water flows through the insulation itself, sealants, jackets, the pipe material or its coatings, corrosive effects water can be amplified.
Sometimes corrosion is accelerated by electrolytes or salts in the moisture, which creates a current between different types of metal in the pipe and insulation, jacket or other components.
This type of corrosion, called galvanic corrosion, is a concern in coastal areas, where salts are carried on the moisture in the air.
The other common type of corrosion is alkaline/acidic corrosion caused when a basic or acidic substance mixes with the water contacting the pipe.
For example, with pipes that carry heated contents (over 250 deg F or 121 deg C) water may evaporate from the pipe surface but migrate to the edges of insulation.
Here the water vapour can condense, mix with sealants and other components and create a corrosive acidic or alkaline mixture. Alkalinity will often produce pitting on aluminum pipes, leading to weak spots and leaks.
MATERIALS AND SYSTEMS THAT REDUCE THE RISK OF CUI
Moisture can never be completely removed from the equation in a petrochemical pipe situation, so a recommended strategy is to look for materials and systems that resist moisture and can be fully sealed against moisture encroachment.
Many engineers specify cellular glass insulation as an effective option to help protect against CUI.
Composed of materials like sand, soda ash and limestone, FOAMGLAS® cellular glass insulation is formed when those materials are heated to extremely high temperatures.
The resulting chemical reaction creates millions of hermetically sealed glass cells that are impervious to moisture both liquid water and water vapor.
Insulation itself is only part of the story. System designers should be aware of how other components in the system, including jackets and sealants, can add to (or detract from) the system’s moisture barrier.
When FOAMGLAS® cellular glass insulation is paired with compatible system accessories, such as high-performance sealants, it becomes an even more robust option to help mitigate CUI.
The ‘FOAMGLAS® Sealed system’ uses the impermeability of FOAMGLAS® insulation in combination with a patented joint sealant to keep moisture out of the system.
The neutral-curing joint sealant has been specially developed for use with FOAMGLAS® insulation systems, it does not contribute to corrosion and allows you to provide compartmentalisation in your insulation system to limit the spread of corrosion.
A recent study conducted by industrial forensics analytics firm RJ Lee Group evaluated the performance of the FOAMGLAS® Sealed System for pipes.
The study used a modified ASTM B117 procedure and Standard Practice for Operating Salt Spray (Fog) Apparatus in order to replicate typical environmental conditions for many petrochemical operations.
The insulated and sealed pipe was exposed to a 5 per cent salt solution in rain or rain/fog conditions for 28 days and then examined for rust under the insulation layer.
At the conclusion of the study, the pipe protected by the FOAMGLAS® Sealed System showed no visible signs of rust.
CONCLUSION
CUI is a costly and ever-present challenge in gas and petrochemical processing settings. While the greatest cause of corrosion moisture can never be eliminated from these working environments, by understanding the conditions that promote CUI and looking for materials and installation techniques that help mitigate it, the risks and expense of CUI can be reduced, helping to keep plants running safely and efficiently.