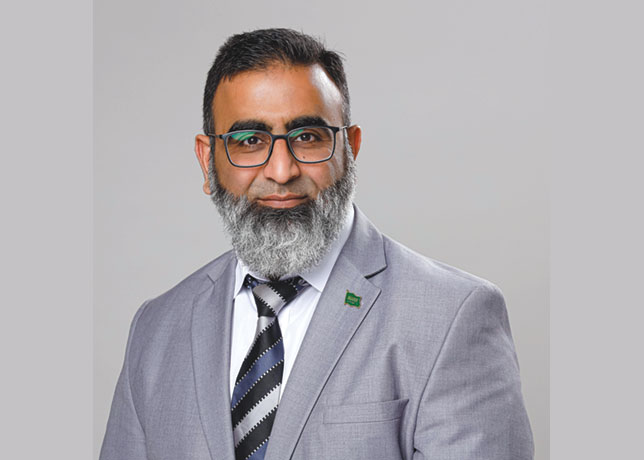
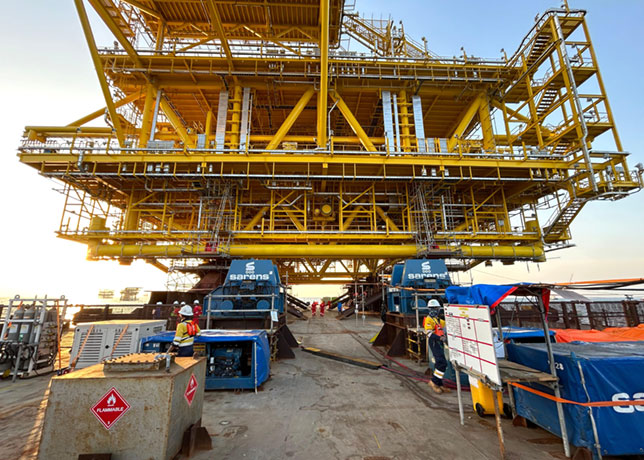
Saudi Arabia advances its energy goals with the Marjan oil field expansion and the world's largest green hydrogen plant, boosting oil output and transitioning to renewables by 2026
Saudi Arabia is advancing its energy and sustainability goals through two transformative projects: the expansion of the Marjan oil field and the construction of the world’s largest green hydrogen plant in Neom. These initiatives underscore the Kingdom's commitment to boosting oil production and transitioning to renewable energy.
The Marjan Increment Program (MIP) Package 2 represents a crucial step in expanding the Marjan oil field's infrastructure.
This phase includes developing oil, water, and gas injection platforms, along with constructing the Marjan GOSP-4 offshore oil and gas separation plant.
Situated in the Arabian Gulf, about 85 km northeast of Tanajib and about 260 km northeast of Dhahran, the project aims to enhance oil processing capacity from 600,000 to 800,000 barrels per day, leveraging advanced engineering and construction methods to meet increasing energy demands. It is located in medium water depths, between 29m and 52 m.
It will provide ESP and future gas lift, tie-in platforms and wellhead facilities to increase crude oil production.
MIP SCOPE OF WORKS & PROJECT EXECUTION
The execution of this complex initiative is being undertaken by the Subsea7-LTEH consortium, operating under a long-term agreement with Saudi Aramco, tasked with the comprehensive engineering, procurement, construction, installation, and commissioning (EPCIC) scope.
A critical component of this effort involves Sarens’ specialised role in installing three topside TP platforms (TP11, TP12 and TP13) using the floatover method. Sarens has already supplied a complete mooring system for floatover operation.
For this purpose, Sarens has been contracted by Subsea7 to supply a mooring system to assist floatover operation that includes cross wire winch, cross wire dyneema cable, docking line winch, docking winch dyneema cable, hydraulic power unit, line tension monitor, tugger winch, tugger cable, directional aids such as swivel guide and universal roller guide.
The selection of this material was made based on floatover engineering simulations, taking into account the winch capacity required for positioning the floatover barge during docking and mating operation phases.
The following factors were taken into consideration: the not-to-exceed (NTE) weight for T&I engineering is 4,800 metric tonnes (MT) for TP11 and TP12 topsides, and 5,800 MT for TP13 topsides.
The NTE weight excludes here the temporary T&I elements, such as gratings, sea fixings, etc.
The winches and related equipment were transported from Belgium to India, delivered to the Mundra port in Mumbai, and then transported by road from Mundra to L&T's Hazira modular fabrication shipyard, where the topsides were loaded out to floatover barge.
Sarens sent a supervisor and a technician to oversee the installation and commissioning of the mooring winches, barge draft sensor system, and auxiliary equipment on floatover barge at the Hazira yard.
The floatover barge transported the Topside platform from the L&T Hazira yard in India and sailed to Saudi waters for installation in the Marjan field.
Sarens personnel travelled to Saudi Arabia and boarded the floatover barge offshore to operate the winches for positioning floatover barge during docking/mating operation.
This process was repeated for the second and third Topside. All three topsides have been safely and successfully installed.
Sarens has extensive experience in the region’s oil and gas sector. Together with McDermott, the company took part of the heavy lifting and load out operations at Jabel Ali as well as at Batam for Marjan Field Package 1, as well as the upgrade and improvement works of PT Pertamina refinery in Balikpapan, Indonesia.
Also, for North Field Oil projects (Qatar Energy) Sarens was contracted by Seatrium to conduct the weighing, loadout and ballasting for two Bridges units, two Jackets and two Topsides utilising up to 132 a/l for the Gallaf 2 project in Batam, Indonesia.
GREEN HYDROGEN BECOMING A REALITY
Construction on the world’s largest green hydrogen plant at Oxagon City, in Neom, Saudi Arabia, is well underway on the ground with full production due to start by the end of 2026.
The site of the Neom Green Hydrogen Company (NGHC) at Oxagon is the ideal spot for the facility thanks to the abundant natural resources and strategic location for global shipping.
The project with a global impact is a key part of the Kingdom’s Vision 2030 to tackle climate change, transitioning to carbon-free fuel and a carbon-free future world.
Powered solely by renewable electricity, the plant will produce up to 600 tonnes of green hydrogen per day, which will be used to decarbonise industries and sectors such as transport and heavy industry. This could save the planet from up to 5 million tonnes of CO2 annually.
Sarens collaborated with Deugro and Air Products in the transportation projects.
During the first stage, Sarens had to work on the route preparation, including bridge bypasses, construction, and civil work.
All the handling with the authorities' requirements, along with coordination with various parties to secure the required permits, were carried out by Sarens.
Moreover, Sarens received and transported the cold boxes and the ammonia converter. During these 12 months of work, challenges included limited access to facilities, remote location in the desert with adverse weather conditions such as heavy winds, rising sand, fog, and intense heat.
Sarens’ support as a partner has allowed NGHC to start project planning at an early stage, which has been critical to the success and has enabled significant progress on the ground.
Commenting on the project, Nour Jamal, Project Manager, Sarens, says: "This project is unique in its nature. This is considered the heaviest and most difficult load in the history of Neom Port due to the challenges faced starting from preparation and mobilisation phase, coordination with various stakeholders granting approvals on time. The situation in the Red Sea affected the mobilisation of Sarens equipment from Belgium to Saudi Arabia and we were forced to receive the equipment at Dammam port at the eastern side of KSA and mobilise via road to Neom at the far west side of KSA."
By Abdulaziz Khattak