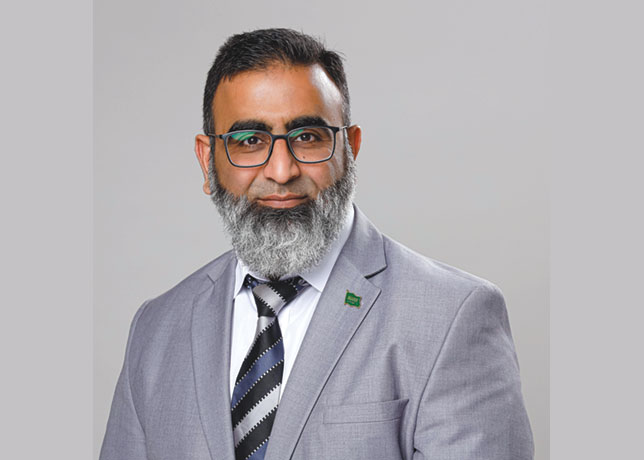
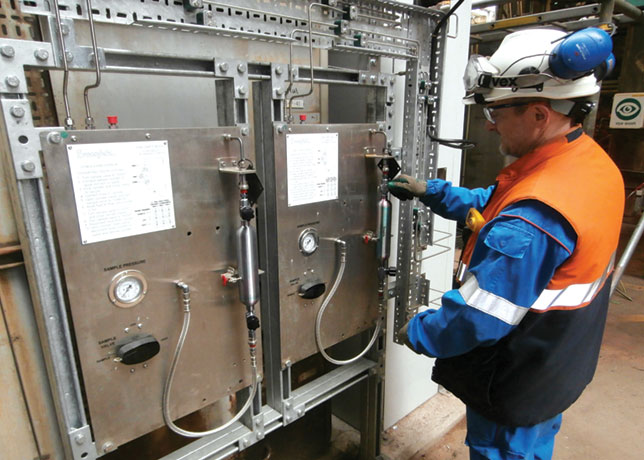
Swagelok offers customisable solutions for various applications, ensuring safety and accuracy. Its rigorous testing and lifetime warranty, combined with expert support, enhance sampling performance and compliance
Swagelok has developed standard grab sampling system designs to meet the needs of customers seeking safe, reliable, and representative sampling in a wide variety of applications.
The company’s standard grab sampling panel designs can be easily customised with additional components, instrumentation, or enclosures, to meet your unique application requirements.
All Swagelok grab sampling assemblies are rigorously tested and are backed by the Swagelok Limited Lifetime Warranty.
![]() |
Minhajullah Syed ... grab sampling system design specialist at Swagelok Saudi Arabia |
"Our highly trained, certified engineers work with your team to identify issues affecting sample quality and opportunities for enhancing safety and system performance. Read on to learn how customers have benefited from Swagelok grab sampling systems and supporting services," says Minhajullah Syed, a specialist with a focus on grab sampling system design.
CUSTOMER CASE STUDIES
At the core of Swagelok’s commitment to excellence lies a series of compelling case studies that demonstrate how its solutions have transformed the operations of diverse clients.
These case studies provide an in-depth look at the unique challenges faced by customers and the tailored strategies implemented to address them.
• Customised sampling cabinet minimises safety risks while simplifying sampling: The customer challenge wanted to improve efficiency and protect its staff.
The customer required non-pressurised liquid samples to be taken according to a specific process to ensure a representative sample.
No electrical components could be used in the sampling process to avoid static potential and fire risks, and operators could not be exposed to the sample.
Swagelok engineers assisted with the design support and fabrication of a sampling cabinet that isolated the system media from the user during the sampling process by using a door to create a separate enclosed area.
![]() |
A Swagelok grab sample valve |
The operator had access to the switches needed for each step, minimising potential for errors and making the system easier to operate.
As a result, the customer now receives more reliable and accurate samples much faster than before, with increased safety.
• Sample system analysis allows refinery to demonstrate environmental compliance: The customer was looking to improve its sample quality.
It had been experiencing problems with "wet" gas sampling for years, with condensable liquids such as off-gas and fuel gas falling out of the gas stream.
The liquids created issues with pressure regulators and other components in the grab sampling panel, and despite numerous expensive investigative and troubleshooting efforts, problems persisted.
The daily requirement for compliance samples could only be met by operators collecting samples at open-to-atmosphere sample points, which is both dangerous and not permitted by environmental groups.
A team of Swagelok sampling specialists worked with the refinery’s unit operators and process engineers to develop a solution.
![]() |
A Swagelok Saudi Arabia field engineer at work |
The gas samples were shown to have liquids that were carryover from another part of the facility and were unnecessary to the gas sample itself.
Once this was determined, the condensate was removed using a knockout pot within the grab sample system without affecting the composition of the sample stream.
Consequently, the use of the knockout pot kept samples dry and allowed the refinery to operate within environmental compliance limits.
• Swagelok Sampling System Training leads to successful grab sampling optimisation engagement: A large refinery needed to standardise its grab sample panels across their operations, replacing simple tap-off filter sample connections with a safer, higher-quality sampling process.
After attending Swagelok® Process Analyzer Sampling System (PASS) training, the customer invited a Swagelok field engineer to educate them on how to implement their standardisation initiative.
The engineer used animated flow diagrams to demonstrate the suggested solution, which required a slight variation to the switching design of their grab sampling panels.
As a result, Swagelok grab sampling panels provided a standardised, easy-to-use solution for upgrading the customer’s obsolete sampling systems.
Replacing the panels improved the customer’s ability to safely capture representative samples.
The support Swagelok provided has led to additional product support through the refinery, including sample probes, tubing bundles, and Swagelok® heated regulator assemblies.
Swagelok Saudi Arabia offers comprehensive assistance with its Grab Sampling Evaluation and Advisory Services.
The local engineering team can visit facilities to assess grab sampling systems, utilising Swagelok’s proprietary onsite inspection mobile application to document its findings.
It will recommend strategies for enhancing the accuracy and timeliness of samples, while also focusing on cost reduction and safety risk mitigation.
The team can also provide guidance on resolving or preventing installation issues and to collaborate on design improvements based on industry best practices.