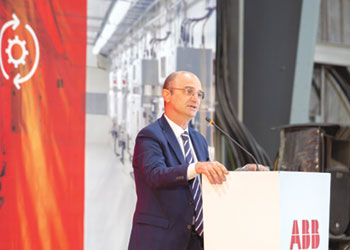
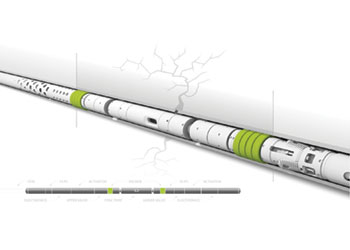
TAQA’s CHALLENGER system offers real-time two-way communication and continuously monitors downhole pressure and temperature in the isolated zone, above top packer element and below lower packer element
Located in the south-west of Norway, the TAQA Well Intervention Center of Excellence is specialised in designing and implementing electrically operated Coiled Tubing (CT) downhole systems which at present do not exist in the marketplace.
One of such key technologies developed by TAQA in co-operation with its clients is the electric straddle packer system, also referred to as the CHALLENGER™ system.
THE CHALLENGER™ SYStEM – A DIFFERENTIATING ENABLER
The CHALLENGER™ straddle packer system is designed for through-tubing services and is conveyed on coiled tubing (CT).
Utilising mechanical packers, it is used to provide pressure isolation across zones of interest, therefore, allowing selective fluid placement.
This way, perforations, inflow control devices (ICDs), screens and other zones of interest can be treated to enhance production, provide injection of water control chemicals, scale treatments, and other similar operations.
The integral downhole system consists of several modules, such as two packer elements, valves, a tension/compression sub, an electronics module and a CCPL for detection of casing collars and perforations.
All functions are controlled electrically from surface via the CT internal cable, which is resistant to acid.
The length between the two packers can be adjusted, and fluid pumped through the CT exits between them. Pressure and temperature sensors are installed above, in between and below the packers, and provide continuous real- time information to surface.
The combination of electric activation of the packers and the placement of the specific sensors provides unique benefits over conventional systems, such as:
• Undisturbed downhole pressure diagnostics in between the packers, as pumping through the CT is not required for the activation of the packers.
• Packers stay set when pumping through the CT is stopped, allowing the monitoring of pressure decline curves, indicating the reservoir’s response to the treatment.
• Individual activation of one mechanical packer or both for increased operational flexibility.
• Manipulation of the CT from surface is not required for setting and un-setting of the packers, which extends the horizontal reach of the system.
• The pressure/temperature sensor below the packers can be used to identify pressure breakthrough during a treatment, typically caused by insufficient cement quality around the casing.
• Due to the selective application of the treatment fluids and pressure monitoring while pumping, the fluid volumes are typically smaller and hence more economical as with conventional systems.
During one operation, the CHALLENGER™ system was used to acid-stimulate seven perforations in a carbonate reservoir, all in a single run.
Exceptional depth control for setting the packers was required, since the blank pipe sections in between the perforation intervals were as short as 2 ft.
In another application, the position (open or close) of 10 ICDs was to be investigated. The ability to hold the packers in the set-position without pumping through the CT was critical to determining the ICDs position by monitoring the trapped pressure between the packers. The position of all 10 ICDs was confirmed in one run.
Due to the long horizontal section of the well, the CHALLENGER™ system was well suited for the operation since no additional force manipulation from surface was required to set and unset the packers.
In addition, the packers had to be set in different internal diameters above and below the ICDs, creating additional hydraulic forces on the CHALLENGER™ system.
The built-in tension/compression sub was critical to the success of the operation, since monitoring of those forces was possible, avoiding unintentional downhole movement and hence damage to the packers.
Today, the CHALLENGER™ system is available for 4.5-inch tubing/casing, downhole ambient pressures of up to 10,000 psi and temperatures of 320 deg F (160 deg C).