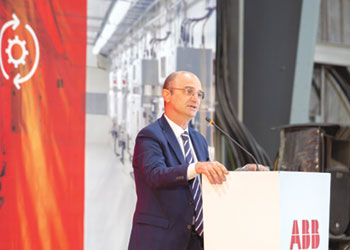
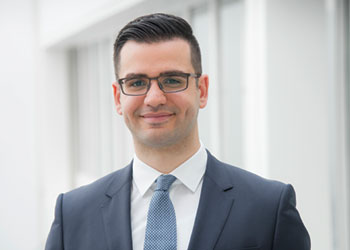
To unlock the potential of hydrogen in the energy transition, clean hydrogen must be complemented with hydrogen with lower GHG footprints and this can be done by choosing the right hydrogen-production technology, Adam Samir Kadhim, Product Line Director, Topsoe, tells OGN
To limit global warming, reducing greenhouse gas (GHG) emissions, such as methane (CH2) and carbon dioxide (CO2 ), is crucial.
Hydrogen production accounts for 3 per cent of global CO2 emissions but its potential in the net-zero carbon economy is massive as it can fuel the decarbonisation of challenging, hard-to-abate sectors and also serve as a long-distance energy carrier.
The Hydrogen Council sees hydrogen production increasing seven fold by 2050, highlighting the urgency to decarbonise production.
Conventionally, hydrogen has been produced from fossil feedstocks without CO2 capture, resulting in high carbon intensity (CI) hydrogen (traditionally called ‘gray’).
To decarbonise production, methods such as steam or water electrolysis, fueled by renewable electricity, have emerged that produce clean or next-to-zero CI hydrogen.
However, the large-scale deployment of clean or ‘green’ hydrogen is currently hampered by insufficient availability of renewable power.
Hence, to unlock the potential of hydrogen in the energy transition, clean hydrogen must – for now – be complemented with hydrogen with lower GHG footprints that is low- and ultra-low CI.
This low-carbon hydrogen (sometimes called ‘blue’) can be produced by combining traditional production methods with carbon capture and permanent storage.
ASSESSMENT OF LOW CI HYDROGEN'S ENVIRONMENTAL IMPACT
![]() |
SynCOR™ is an advanced autothermal reforming process and the preferred |
A well-to-gate lifecycle analysis is needed to accurately assess the environmental impact of hydrogen production. This includes GHG emissions associated with natural gas production, transport, hydrogen production, CO2 capture, transport, underground storage, and energy consumption.
Carbon intensity (CI), the amount of CO2e emitted per kilogramme of produced hydrogen, is a key metric for evaluating GHG emission reduction.
To assess how the CI level of hydrogen production can be cut, it is necessary to look at two innovative production processes in particular, and the CO2 capture methods.
Several production methods are currently available, such as steam methane reforming (SMR), which is the most common method; heat-exchange reforming (HTER) reactor and modified steam methane reforming (SMR-B); and convection reforming, also known as Haldor Topsoe Convection Reformer (HTCR), which has good suitability for lower capacity requirements.
However, SynCOR™ and eREACT™ stand out as the two best-in-class technologies when it comes to lowering CI – and both require no high Capex flue gas technologies.
ADVANCED AUTOTHERMAL REFORMING WITH LOW OPEX AND CAPEX
SynCOR reforming is an advanced autothermal reforming process but unlike other ATR processes, SynCOR operates at a significantly lower steam-to-carbon ratio and takes place within a single reactor.
In the SynCOR reactor, process gas enters and combines with oxygen and additional steam, undergoing combination of oxygen combustion and steam reforming simultaneously.
Among the various low-CI hydrogen technologies, the SynCOR process demonstrates the lowest Opex.
Its steam-to-carbon ratio of 0.6 is 3-5 times less than SMR or conventional ATR systems, meaning smaller equipment and piping sizes, which is particularly advantageous at larger scales where standard size ranges can be maintained even at high capacities.
External fuel demand is exceptionally low, enabling a high carbon-recovery rate of over 99 per cent without the need for capturing carbon in the flue gas.
This makes SynCOR highly suitable for low- and ultra-low CI hydrogen production – and for deployment in mega-scale plants.
Currently, the largest operational SynCOR reactor produces 500 kNm3/hour of hydrogen, with a single-train capacity limit of 825 kNm3/hour.
ELECTRIFIED STEAM METHANE REFORMING
Another super-promising method for hydrogen production is electrified steam methane reforming, known as eREACT.
Here the main reforming reactions take place within a catalytic reactor heated by an electrical current. This eliminates the need for hydrocarbon fuel as a heat source, consequently eliminating flue-gas emissions from the reformer.
The energy density of the process allows for a significantly smaller reactor size compared to traditional SMR units.
Importantly, almost all of the CO2 present in the shifted process gas can be economically recovered using a CO2-removal unit. This makes eREACT an excellent choice in scenarios where electricity prices are favorable.
The eREACT process has undergone successful pilot-scale testing and a demonstration plant is planned.
CO2 REMOVAL TECHNOLOGIES
Efficient carbon capture is crucial and currently three CO2 removal options are available on the market:
• CO2 removal from process gas: After natural gas is reformed into syngas, CO2 can be captured at high pressure through a solvent absorption-based process. This method requires less energy and capital expenditure compared to CO2 removal from flue gas.
• CO2 removal from PSA off gas: During hydrogen purification in a pressure swing adsorption (PSA) unit, CO2 exits the unit with an off gas. Cryogenic-separation technology can be employed to condense the CO2, allowing it to be transported as a dense phase fluid.
• CO2 removal from flue gas: CO2 generated by the combustion of fuel gas and PSA off gas can also be captured. This solution can be suitable for revamping existing plants or for implementation in new small-capacity plants.
Integration with the hydrogen-production process is a crucial factor in selecting carbon-capture technology. Topsoe offers customers solutions that combine hydrogen production and carbon capture in a single facility under a unified technology license.
CHOOSING THE RIGHT HYDROGEN-PRODUCTION TECHNOLOGY
Production capacity, hydrogen yield, process carbon intensity, and the levelised cost of hydrogen (LCOH) are some key determinants in selecting suitable technology.
• Production capacity: Small capacities favour HTCR and eREACT due to their compact design, while SynCOR excels at higher capacities with low Capex and strong economy of scale.
• Carbon intensity (CI): SMR-B has the lowest inherent CI among conventional technologies, while eREACT offers a significant improvement. CO2 capture from process gas reduces CI further, particularly in SynCOR and eREACT, making them ideal for ultra-low CI production.
• Levelised cost of hydrogen (LCOH): SynCOR demonstrates the lowest LCOH, benefiting from high yields, lower Capex and Opex.
Consequently, SynCOR is the preferred choice for mega-scale low-CI production. However, eREACT is a good option under specific conditions such as favorable natural gas and electricity costs, or smaller capacities.
In short, decarbonisation needs innovative solutions, and low- and ultra-low-CI hydrogen produced through SynCOR and eReact are highly promising options.
SynCOR, for instance, enables the generation of hydrogen with less than 0.1 kg CO2 per kg of hydrogen produced, while eliminating over 99 per cent of process CO2.
Additionally, when Topsoe’s hydrogen process portfolio is pair with FidelisH2™ technology (under exclusive license) the solution enables the production of hydrogen with a possible lifecycle carbon intensity of 0 kgCO2e/kgH2. Now that’s progress!