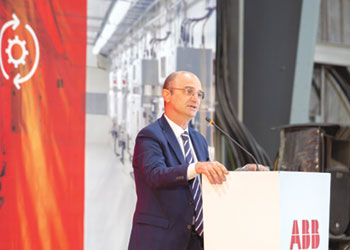
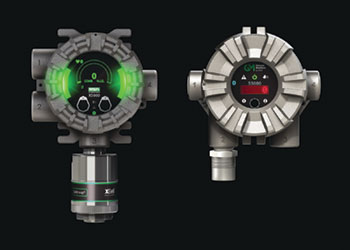
The General Monitors® S5000 gas monitor and its innovative XCell® sensors, demonstrate MSA’s commitment to helping enhance the level of safety for workers who may be exposed to harmful gases
In support of Saudi Arabia’s Vision 2030, Mohammed Hassan Sherbiny for Commerce (Sherbiny), long-time local partner of MSA Safety, established its new manufacturing division Atheel, where the General Monitors® S5000 gas detector is locally assembled.
Both firms are long-established suppliers to Aramco for fixed flame and gas detection products and systems.
By providing local assembly capabilities and complete industrial solutions with engineering and technical services through Sherbiny, this partnership enhances MSA’s ability to serve customers in the region with faster delivery times, while also strengthening MSA’s technical support capacity and customer service.
The General Monitors® S5000 gas monitor and its innovative XCell® sensors, demonstrate MSA’s commitment to helping enhance the level of safety for workers who may be exposed to harmful gases, including hydrogen sulfide and carbon monoxide.
At the same time, the enhanced performance and self-diagnostics offered by the innovative sensor technology also help to lower the total cost of ownership for the owner.
THE TECHNOLOGY BEHIND THE SENSORS
MSA’s advanced sensor technology is called TruCal® and offers many benefits to the user and their associates working in hazardous areas:
• Enhanced levels of safety.
• Multiple sensor status checks per day.
• Self-calibrations in the event of sensor drift due to changes in the environment.
• Extended manual gas calibrations up to two years.
• Automatic monitoring on the sensor inlet for blockages.
• High levels of overall performance, with better stability and measurement accuracy.
• Long sensor life, with an ionic non-consuming technology.
• Industry-leading 3-year sensor warranty for peace of mind.
• Longer shelf life for the sensor, up to 3 years, reducing stocking costs.
Today, the best practice for the oil and gas industry is to calibrate gas detectors that use electrochemical cells every 90 days.
Such calibrations are necessary to determine whether the traditional electrochemical sensors can detect the target gas or whether their inlet is blocked.
This is usually only discovered during a manual gas calibration when gas is applied to the sensor.
![]() |
The S5000 gas monitor demonstrate MSA’s commitment to workers' safety |
However, between these manual calibrations, the electrochemical could be unable to detect gas at any time. This is the fundamental reason why frequent, labour-intensive, expensive servicing has been required for these types of sensors. TruCal technology reduces this uncertainty as it performs a sensor self-check four times a day.
TruCal technology is incorporated in MSA’s patented XCell H2S and CO electrochemical sensors.
The pulse check within the sensor provides a reliable sensor interrogation method that identifies and corrects for changes in output sensitivity (sensor drift).
The pulse check uses MSA’s patented technology to calculate gas response by applying an electronic pulse to the sensor and analysing the response curve of the last manual gas calibration.
Through proprietary algorithms, MSA can quantify positive and negative drift that results in real-time accuracy adjustments (self-calibrations) during the pulse check providing accurate sensitivity and functionality. This latest technology is referred to as Adaptive Environmental Compensation (AEC) and occurs every six-hours, which allows for manual gas calibrations to be extended up to two years.
The second part of Trucal is called Diffusion Supervision. In an industry-first, Diffusion Supervision monitors the sensor’s inlet for blockages, which would prevent gas from reaching the electrochemical cell inside.
Should the inlet of traditional sensors become blocked, the sensor cannot identify this condition and go into fault. This is one of the reasons why frequent manual gas calibrations are recommended.
• A sensor design: The revolutionary electrochemical sensor design uses a type of electrolyte, which reacts with the specific target gas.
The electrolyte is now an ionic liquid, which has a lower vapour pressure so doesn’t evaporate and most importantly is not consumed during the chemical reaction that occurs when the target gas is present.
Instead of the one- to two-year sensor life (depending on application and environment) of MSA’s traditional electrochemical sensors, users can now expect a sensor life of more than five years, supported by its industry-leading three-year sensor warranty.
• Rugged and easy-to-use transmitter: The S5000 Stainless Steel 316 Transmitter design has also been enhanced, with a touch screen display for menu access, as well as a brighter display for an easy visual status indication.
In addition to the enhanced interface, the S5000 offers LED indicators for normal operation, fault and alarm indication.
An easy retrofit of the detector is possible because it shares the exact mounting footprint as the previous model – the S4000 series, making upgrades quick and easy as the existing installation accessories and cabling can be reused. This also means there is not requirement for any hot work.
• User-friendly interface: MSA also introduced Bluetooth® communication for the point gas monitors for the first time.
Through the MSA Connect app, the transmitter’s menu can be accessed over the encrypted and secure wireless communication. This allows for faster initial configuration of the device, saving valuable time and also for remotely accessing the transmitter when located in inaccessible locations.
Various XCell sensors can also be fitted with the new X/S5000 CalGard Remote Calibration Adapter, which allows for the sensor to be remotely calibrated and not just a simple bump test like a gassing adapter permits. This provides safe and accurate calibrations without having to apply gas directly to the sensor.
• Do more with less, utilising the dual sensor capability: The S5000’s dual sensing technology doubles the sensing power while reducing the capex of the transmitters and also reduces the installation cost as less cabling, cable trays, junction boxes and other installation accessories are required.
One or both sensors can be remotely mounted up to 100 m from the transmitter, giving greater flexibility to the user by positioning the sensor exactly where they are required, whilst still being able to easily access the transmitter.
• Summary of the technology behind MSA’s truly smart gas monitor: MSA’s TruCal technology determines whether a sensor is installed, operating within its predetermined sensitivity limits, is corrected to account for any drift since the last pulse check event and checks the inlet is unblocked. TruCal enables six actions, including that it:
1. Validates that the sensor is operating normally.
2. Compensates for sensitivity drift due to changing environmental conditions.
3. Recommends when a full calibration should be performed.
4. Warns when a sensor needs to be replaced in the near future, by indicating the sensor life as 'good' or 'fair.'
5. Checks the inlet of the sensor is not blocked preventing gas detection.
6. Alerts the end user if the device is no longer able to monitor the area, by initiating a fault signal.
In conclusion, MSA’s revolutionary S5000 with TruCal technology sets a high standard for performance and reliability and is now assembled locally by Sherbiny in the Kingdom of Saudi Arabia.