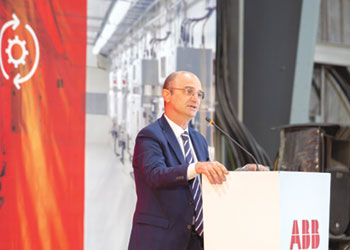
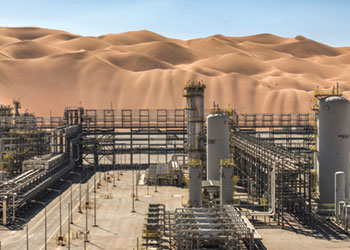
Much of Saudi Arabia's oil and gas reserves are situated in distant and harsh environments, posing substantial obstacles to translating potential into actual output. Nevertheless, Aramco has displayed an unwavering determination to successfully initiate projects that contribute to fulfilling the world's energy needs
Aramco over the years has developed several mega projects with investment of billions of dollars to increase its oil and gas production as well as in the downstream sectors.
"We are explorers at heart, always searching for new frontiers. At Saudi Aramco, a new frontier can be exploring a new geographic area, creating a new technology, entering a new partnership or enabling new opportunities for our business," says Aramco.
When it comes to petroleum geology, Saudi Arabia is home to some of the best in the world. Much of this geology is located in remote, inhospitable places. However, that hasn’t stopped Aramco from meeting those challenges and investing in projects that help meet global energy demand.
A look at three challenging mega projects undertaken by the energy giant:
MANIFA
Manifa oil field project is extraordinary and Aramco's work at Manifa demonstrates what can be achieved when creativity, determination, and engineering prowess are applied to deliver solutions to the seemingly impossible.
The journey began in 1957, when the Manifa oil field was discovered – a huge six-reservoir field stretching 45 km long and 18 km wide, lying in less than 15 m of water. However, it’s not just a treasure trove of oil and gas hiding beneath the bay, but also a delicate habitat of seagrass and coral reefs. The turquoise waters are teeming with marine life, from pearl oysters to sea snakes, shrimps, crabs, dolphins and sea turtles, including the endangered Hawksbill turtle. It’s also a safe haven for migratory birds. As the oil lay just beneath the shallow waters, it presented a major environmental challenge. Conventional shallow water drill rigs could damage the fragile marine environment. A risk Aramco wasn’t willing to take.
![]() |
Manifa project |
Manifa Bay plays an essential role for humans too. It acts as the lifeblood for fishermen and their communities. With an ecosystem sensitive to overfishing and pollution, preserving this underwater ‘museum’ was critical to Aramco's objectives.
In 2006, with an initial investment of $10 billion, the adventure to find the best way to produce oil from a shallow, ecologically-delicate, offshore oil field sprang into action.
To avoid damaging the fragile ecosystem, Aramco engineers devised a radical new approach. They shunned the easy option of building 30 offshore platforms, and came up with the idea to convert over 70 per cent of the field into an onshore field.
This meant creating 27 man-made islands, each one the size of 10 soccer pitches, all made from 45 million cu m of sand reclaimed from the seabed. The islands would act as onshore drill sites above the offshore oil field, and would be linked by a 41-km causeway with 13 bridges to keep the ocean currents circulating naturally.
Aramco designers and engineers spent 4 million hours on the design phase alone, with 136,149 engineering drawings and plans to perfect the 27 islands, 13 bridges, 13 offshore platforms, 15 onshore drill sites, 350 new wells, injection facilities, multiple pipelines, and a 420-megawatt heat and electricity plant.
Below ground, the challenges were no less demanding. As the six enormous reservoirs of up to 40 km long are stacked one on top of the other, Aramco had to invent new technology from scratch. So it built the nuclear magnetic resonance tool especially for Manifa, to create real-time 3D profiles of the reservoir layers. This allowed geologists to accurately tap into reserves at extreme distances, through a heavy layer of tar, from wells on the surface.
In 2013, oil production began three months ahead of schedule and more than $1 billion under budget. By July 2013, the project’s first milestone to produce 500,000 barrels of oil per day was achieved, and by 2017 the ultimate target of 900,000 per day was reached.
SADARA
Sadara is not just another project; it is the cornerstone of Aramco's downstream strategy to become a leading global integrated energy and chemicals enterprise.
![]() |
Sadara plant |
Aramco partnered with The Dow Chemical Company for this project because of its technical competence in producing high volumes of speciality chemicals. This capability, combined with Aramco's refining expertise and ability to produce and leverage high volumes of versatile feedstocks, made the prospect of joining forces very attractive.
The name Sadara means ‘in the lead’ in Arabic. It was chosen to reflect the company's quest for progressive leadership, superior performance, and its commitment to becoming the global leader in petrochemicals production.
In 2011, construction began on the $20-billion Sadara mega-project. Located in Jubail Industrial City II on the east coast of Saudi Arabia, the site was chosen because of its strategic access to growing chemicals markets in the region and in Asia.
Plans for Sadara featured 26 integrated world-scale manufacturing plants that could produce more than three million tons of performance plastics and high-value chemicals per year. Of the 26 plants, 14 would be capable of producing specialty chemical products that have never been produced in the Kingdom before.
In 2016, Sadara marked a historic landmark with the startup of its mixed feed steam cracker, making it the first chemicals facility in the GCC countries to crack naphtha. The cracker, which breaks ethane and naphtha to form new molecules, including ethylene and propylene, enables the production of a diversified range of plastics and chemical products designed to meet the rigorous standards of sectors such as advanced packaging, construction, electronics, furniture, and the automobile industry.
In another first for the Gulf region, Sadara produces toluene diisocyanate (TDI). TDI is mainly used in the production of flexible polyurethane foam for furniture, mattresses, cushioning, and car seats. TDI also has a variety of industrial uses, such as coatings, adhesives, sealants, specialty foams, and other products.
Sadara is the largest chemical complex ever built in a single phase. Sadara has 4,300+ employees .
Sadara’s full value is seen in an economic ripple effect of industrial clusters, value parks, and the development of the knowledge-based research, engineering, and service firms to support them.
SHAYBAH
In the 1940s and ‘50s, geologists were trying to piece together a puzzle: What was the full extent of the Kingdom’s subsurface petroleum structures? Early explorers delved into some of the harshest, most desolate environments in the world to answer this question. In 1948 they discovered the Ghawar field – the largest crude oil field in the world – on the edge of the Rub’ al-Khali. But what lay undiscovered beyond it, deep in the heart of the Empty Quarter?
In 1968, in the middle of Rub’ al-Khali desert, approximately over 500 miles from Aramco's headquarters in Dhahran, Aramco discovered a vast oil field, guarded by dunes of red and golden sand 1,000 ft (333 m) tall and regularly buffeted by winds of up to 80 kmph (50 mph). And where temperature in summer routinely reaches 122 deg F (50 deg C). The terrain, climate, and complexity of logistics, however, meant that development was out of the question, so the field lay silent for another 30 years.
By the time of Aramco's major expansion phase in the 1990s, advances in technology – and in its own engineering capabilities – had given it the confidence and ability to take on more challenging projects. So it turned its attention back to that massive oil field deep in the Rub’ al-Khali.
With the ideas, strategy, and design in place, construction began in 1995. Approximately 13 million cu m of sand was moved. A 386-km road was built through the desert; and a fully operational airport too. A 645-km pipeline was laid to processing facilities further north. 145 oil wells drilled. Three gas oil separation plants (GOSPs) built. And finally, extensive support and residential facilities were put in place, to house people staying in one of the most remote places on Earth for weeks at a time.
By 1998, with endurance, commitment, and determination, Aramco overcame tremendous obstacles, and completed the project a whole year ahead of schedule. It took a colossal 50 million man-hours to do so.
• Information for this article has been derived from Aramco's website.