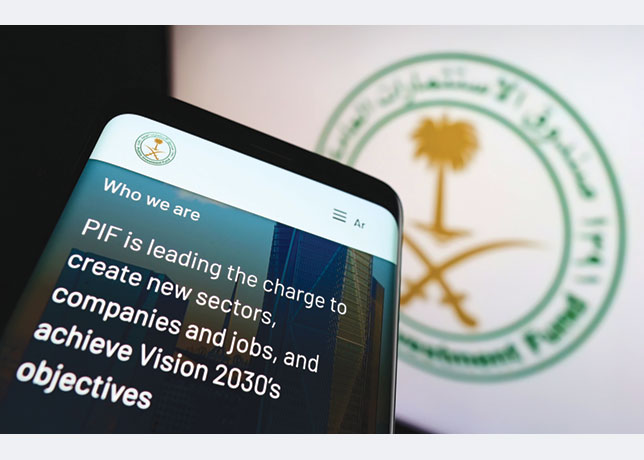

In an era where data reigns supreme, Endress+Hauser is harnessing the power of artificial intelligence (AI) and digital transformation to revolutionise industrial process engineering. Speaking to OGN, Jan Strohmeier, Digitalization Manager, underscores the shift towards a data-centric future
The process industry is undergoing a significant transformation as it rapidly embraces a data-centric future.
Traditionally, this sector has relied heavily on manual processes and conventional methods for monitoring and controlling operations.
However, with advancements in technology and the rise of Industry 4.0 principles, there is a growing recognition of the immense value that data can bring to the industry.
One of the key drivers behind the shift towards a data-centric future is the increasing availability of sensors, connected devices, and Industrial Internet of Things (IIoT) technology.
![]() |
The Micropilot FWR30 is a cloud connected radar level sensor |
These advancements enable the collection of vast amounts of real-time data from various stages of the process, including equipment performance, environmental conditions, and product quality metrics.
As Jan Strohmeier, Digitalization Manager, Endress+Hauser, states: 'More than 40 million Endress+Hauser instruments in use worldwide are constantly creating a huge amount of data and valuable information for the users. And Endress+Hauser is constantly developing new and enhanced measuring devices for the process industry.'
With the new generation of devices, there is more intelligence inside and more data generated.
'With the additional information about the device and the application, new outcomes can be generated. This will ensure our products are future ready,' says Strohmeier.
By leveraging this data, companies in the process industry can gain valuable insights into their operations, identify patterns and trends, and make informed decisions to optimise efficiency, reduce costs, and improve overall performance.
![]() |
The Memosens technology has revolutionised liquid |
For example, companies can deploy predictive maintenance strategies by monitoring equipment performance and identifying signs of potential failures before they occur.
This proactive approach helps minimise unplanned downtime, improves equipment reliability, and extends asset lifespan, ultimately reducing maintenance costs and enhancing overall operational efficiency.
Strohmeier says: 'Endress+Hauser is committed to supporting its customers along the road to digitalisation. The Endress+Hauser cloud solution Netilion makes use of specific data from production processes and serves to increase efficiency alongside conventional plant topology.'
One example is the cloud connected IIoT radar FWR30 level sensor from Endress+Hauser and the Battery Magnetic Flow Meter that sends data directly via 3G/LTE into the company’s Netilion ecosystem.
Strohmeier says: 'We have thought about brownfield installation and have solutions to enable any field device to be connected securely to the cloud using digital field protocols like Hart to send the data into the cloud via an Edge device.'
Alternatively, Bluetooth or Wireless Hart connection can be used when installing new cables but that is not feasible.
![]() |
Netilion ... an award-winning cloud-based IIoT ecosystem designed |
When developing a cloud solution, it is of the highest importance to ensure cybersecurity from the device till the cloud.
Endress+Hauser has developed the Netilion Ecosystem with security and data privacy as the backbone of the solution.
'Users can empower themselves and their teams with the right data. With just two steps – registering and connecting devices – customers can digitalise their plants and start benefitting immediately,' says Strohmeier.
Another significant aspect of the data-centric future in the process industry is its impact on quality control and regulatory compliance.
With stringent quality standards and regulatory requirements, companies must ensure that their products meet specified criteria and adhere to regulatory guidelines.
By implementing data analytics tools and systems, companies can monitor product quality in real-time, identify deviations from standards, and take corrective actions to maintain compliance and uphold product integrity.
A good example here would be the Memosens technology from Endress+Hauser that has revolutionised liquid analysis technology.
It converts the measured value to a digital signal and transfers it inductively to the transmitter, eliminating the problems associated with moisture at the sensor connector.
With the digital sensor, the sensor cable is not part of the measuring loop anymore and, therefore, makes sensor replacement in the field fast and easy.
With this decupling of sensor and cable, it will be possible to perform any calibration in the laboratory under controlled condition rather than in the harsh and sometimes hazarders field environment.
Version 2.0 has increased the memory size within the sensor to be able to store eight times more data, such as calibration histories and load matrices, paving the way for true predictive maintenance and enhanced IIoT services.
Additionally, the data-centric approach facilitates collaboration and integration across the entire value chain, from suppliers to customers.
By sharing relevant data and insights with partners and stakeholders, companies can improve supply chain visibility, enhance communication, and foster innovation, leading to greater efficiency and sustainability across the industry.
Strohmeier adds: 'While digitalising plants, customers can create digital twins of all their assets and build the initial connections with them. This will be the first step to many future functionalities and improvements. Users get an overview of what equipment is currently installed, create lists, organise assets the way they like and increase their knowledge about their installed base and make their plants transparent.'
There are several benefits to this for users, including:
• Reducing their maintenance efforts by getting evaluations of obsolescence and standardisation possibilities of their equipment and reduce the complexity in the field and reduce spare part stock.
• Get to know which assets are not available anymore and automatically receive replacement recommendations; act consequently and increase reactivity thereby reducing risk and increasing plant’s uptime. Netilion analytics use present and past information to reveal improvement potential that users would have never thought of before.
• Handling documentation becomes effective as there will be less supporting documentation to manage.
• Once users have collected the data of an asset, it is instantly available on all their devices and wherever they are.
In conclusion, Strohmeier says: 'Endress+Hauser strives to create a unified and memorable journey for the customer from the first contact till the after sales support. And data has emerged as a game changer for this, paving the way for unprecedented levels of efficiency, quality, and innovation. Organisations harnessing the power of data will not only thrive but also lead the way towards a more sustainable, agile, and interconnected future.