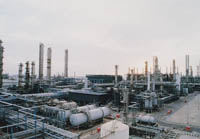
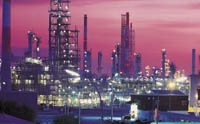
PROVIDING ECONOMIES of scale and operating some of the most advanced systems available, Saudi Aramco Mobil Refinery Company (Samref) is an industry pioneer for reliability, utilisation of assets and safety record.
The refinery, which with a processing capacity of approximately 320,000 bpd of Arabian Light crude, is one of the largest in the world, also boasts one of the world's largest vacuum towers.
The joint venture Yanbu plant consists of single-train process units which provide important economies of scale, according to the company.
A primary upgrade process is fluid catalytic cracking (FCC), whereby heavier oil is converted into lighter, higher value products.
Other important upgrading processes are Hydrofluoric Acid Alkylation, Visbreaking, Continuous Reforming, Isomerisation and Catalytic Hydro-Desulphurisation (CHD).
Samref receives Arabian Light crude, ethane gas and mixed butane NGL streams from tankage at the Saudi Aramco crude terminal in Yanbu and the Yanbu NGL plant directly supplied by the 1,400 km East-West pipeline from Dhahran.
Most finished products are blended in-line as they are pumped directly to shipping berths at the oil terminal close to the refinery.
Commercial production at the refinery began in November 1984 with a rated processing capacity of 263,000 bpd.
Debottlenecking of units, installation of new facilities and the application of processing improvements have, since the beginning, helped to substantially increase capacity.
The refinery has a number of key performance indicators (KPIs) to measure its performance. The KPIs not only include measures of production performance but also of safety, environment and efficient use of energy.
While Samref's performance in these areas has been steadily improving over its history, the last few years has, in particular, seen the refinery become internationally recognised as either exceeding or approaching pacesetter levels in many aspects of its business.
The design of the refinery provides flexibility to produce a wide range of products for specific markets. The long term strategy includes plans to diversify into the production of petrochemical feedstocks to satisfy growing domestic demand.
Environmental controls are an integral aspect of Samref's operations, and the refinery has procedures in place to ensure that stringent emission standards are fully met.
The plant's facilities have been designed to enable recovery of more than 400 tonnes of pure sulphur per day from its feedstock in order to produce low sulphur products.
Samref also says that it spends approximately $1 million every year on disposal of waste to minimise the effect on the environment.
Around 1,000 tonnes per year (tpy) of spent catalyst is recycled to the construction industry by processing it through a cement plant rather than sending it to landfill.