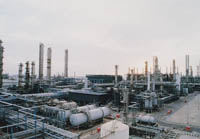

With the Gulf's rapid development over the past decades, the use of reinforced concrete has emerged as the most widely-used construction material due to its versatility and durability.
However, many structures are today showing signs of spalling and deterioration due to processes that were little understood at the time of construction.
From high rise residential blocks to power and desalination plants, it is not uncommon to see extensive corrosion of the reinforcing steel caused by a number of factors such as inadequate specifications, poor workmanship practices and/or contamination by deleterious elements such as chloride salts which may have been cast into the concrete at the time of construction, or due to atmospheric exposure to chloride-rich coastal environment and sabkhas.
Understanding the cause and extent of reinforcement corrosion is the key to selecting an appropriate repair solution. One option is to simply repair visibly spalled areas by first breaking out the concrete to fully expose the corroding steel. The steel is then cleaned and primed and the patch reinstated with a pre-bagged repair mortar.
A protective coating is then normally applied to the surface of the structure to prevent further carbonation or chloride ingress.
Such an approach is effective in aesthetically upgrading the structure in the short term but does not necessarily address the problem of ongoing corrosion due to existing carbonation or chloride contamination.
One possible solution is to break out all contaminated concrete. This is effective but expensive, dusty, noisy and disruptive and may necessitate temporary propping of the structure due to mass concrete removal.
However, a number of corrosion control techniques are now available to the building owner or engineer to prolong the life of the structure and minimise future maintenance. These include Realkalisation, Chloride Extraction, Impressed Current Cathodic Protection (ICCP) and Galvanic Protection.
Realikalisation and Chloride Extraction
These treatments are carried out by applying currents to the reinforced concrete utilising temporary, surface-mounted anodes in electrolytic reservoirs. Commercially available under the Norcure brand name, these are highly effective, provable techniques used to solve a number of corrosion-related problems from basements contaminated from saline and groundwater leakage to historical monuments/buildings suffering from carbonation.
ICCP
This is a well-proven corrosion control technique and has been used to protect reinforced concrete structures since the 1970s.
The technique bears similarities to the realkalisation and chloride extraction processes in that a small current is passed through the reinforcing steel, and is a reliable option for structures where further chloride ingress cannot be prevented.
The current applied is sufficient to prevent anodic reactions at the steel reinforcement and render it cathodic, thereby protecting it from further corrosion. However, the current must be applied for the life of the system requiring a permanent anode system and rectifier units.
ICCP utilises either discrete or external anode systems. A typical discrete system comprises cylindrical, mixed metal oxide (MAYO) anodes connected by wire and grouted into drilled holes adjacent to the reinforcing steel. External systems can comprise either conductive paints or titanium mesh anodes which are covered by a thin layer of low resistivity mortar (termed 'overlay').
In addition to the cost of initial installation, ICCP also requires investment in regular monitoring to ensure that the system is operating effectively.
Galvanic protection
Galvanic protection utilises the sacrificial properties of zinc when coupled to steel, and has emerged as one of the most effective methods for the control of corrosion in reinforced concrete.
One system (Galvashield XP), is attached to the reinforcing steel at the edge of the required patch repair to prevent the setting up of 'incipient anodes' which in turn lead to future deterioration of zones outside the patch.
Galvashield CC is another system recently made available and comprises cylindrical, mortar encased zinc anodes wired together in sequence and inserted into drilled holes in grid configuration. When connected to the steel reinforcement the grid impresses a galvanic current through the steel reinforcement, suppressing anodic reactions and controlling corrosion.
No external rectifier is required as the galvanic anodes are effectively self-powered. The zinc anodes slowly corrode sacrificially over their lifetime and display intelligent behaviour by adjusting current output to reflect environmental conditions. Optional monitoring can provide the building owner or specifier with current output and polarisation data if required.
This form of discrete galvanic protection system is a lower cost option than realkalisation, desalination and ICCP. It can provide long-term, maintenance-free protection.
It is particularly useful for those seeking an easy-to-install system with no ongoing monitoring costs. It is suitable for all types of structures including prestressed and post tensioned structures where ICCP, realkalisation and desalination are often precluded due to potential hydrogen evolution and the associated risk of steel embrittlement.
Conclusion
Concrete repair can be an expensive business.
It is labour intensive, access costs are often high, and there may be a consequential loss of income due to temporary closure of the structure.
By embracing the technologies described above, Fosroc/Fosam can offer the building owner or specifier a full range of repair and protection options to ensure that their concrete repair solution addresses not only visible defects but the hidden corrosion that, if left unchecked, may incur even more costly and disruptive repair works in the future.